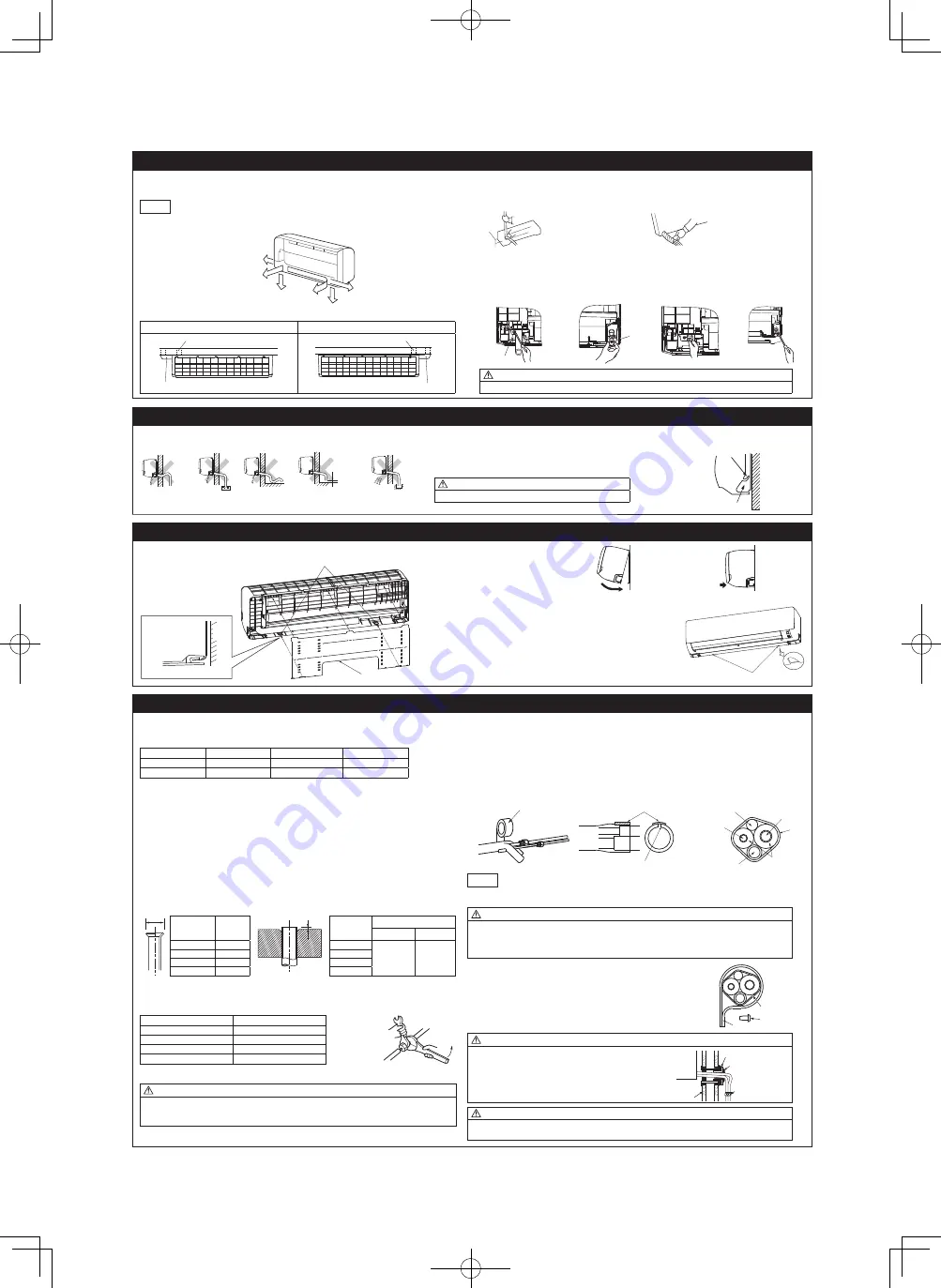
'19 • PAC-DB-333
- 71 -
6. FORMING PIPING AND DRAIN HOSE
1. Forming piping
Piping is possible in the right, rear, downward, left, left rear or left downward direction.
NOTE
Suf
fi
cient care must be taken not to damage
the panels when connecting pipes.
g
n
i
p
i
p
e
d
i
s
d
n
a
h
t
h
g
i
R
g
n
i
p
i
p
e
d
i
s
d
n
a
h
t
f
e
L
Piping in the left direction
Piping in the left rear direction
Piping in the right rear direction
Piping in the right direction
Forming of pipings.
• Hold the bottom of the piping and
fi
x direction
before stretching it and shaping it.
Taping of the exterior
• Tape only the portion that goes through the wall.
• Always tape the wiring with the piping.
Pipings
Drain hose
2. Drain change procedures
(1) Remove the screw and drain hose.
(2) Remove the drain cap by hand or pliers.
(3) Insert the drain cap which was removed at procedure (2) securely using a hexagonal wrench etc.
(4) Install the drain hose and screw securely.
)
4
(
)
3
(
)
2
(
)
1
(
Screw
cap
CAUTION
Incorrect installation of drain hose and cap can cause water leakage.
7. DRAINAGE WORK
• Arrange the drain hose in a downward angle.
• Avoid the following drain piping.
Higher than
specified
Wavy
The drain hose
tip is in water.
The gap to the ground
is 5 cm or less.
The drain hose tip
is in the gutter.
Odor from
the gutter
• Pour water to the drain pan located under the heat exchanger, and ensure that the water is discharged outdoor.
• When extended drain hose is present inside the room, insulate it securely with heat insulator available in the market.
Gutter
Wall
Pipe space
Since this air-conditioner is designed to collect dew drops on the rear surface to the
drain pan, do not install the connecting wire above the gutter.
CAUTION
Incorrect drainage work can cause water leakage.
8. INSTALLING INDOOR UNIT
Installing the indoor unit to installation board
Indoor unit
Base latch (2 locations)
Installation board
Indoor unit base latch
Installation board
Wall
(1) Pass the pipe through the hole in
the wall, and hook the upper part
of the indoor unit to the installation
board.
(2) Gently push the
lower part to
fi
x
the indoor unit
base lower latch to
installation board.
Removing the indoor unit from installation board
Base latch
(1) Push up at the marked portion of the indoor unit base latch,
and slightly pull it toward you (both right and left hand sides).
(The indoor unit base latch can be removed from the installation
board.)
(2) Push up the indoor unit upward so that it can be removed from
installation board.
9. CONNECTING PIPING WORK
1. Preparation of connecting pipe
1.1. Selecting connecting pipe
Select connecting pipe according to the following table.
Model SRK63
Model SRK71/80
Model SRK100
Gas pipe
ø12.7
ø15.88
ø15.88
Liquid pipe
ø6.35
ø6.35
ø9.52
• Pipe wall thickness must be greater than or equal to 0.8 mm (ø15.88:1.0mm).
• Pipe material must be O-type (Phosphorus deoxidized seamless copper pipe ICS 23.040.15, ICS
77.150.30).
1.2. Cutting connecting pipe
(1) Cut the connecting pipe to the required length with pipe cutter.
(2) Hold the pipe downward and remove the burrs. Make sure that no foreign material enters the pipe.
(3) Cover the connecting pipe ends with the tape.
2. Piping work
2.1. Flaring pipe
(1) Take out
fl
are nuts from the operation valves of indoor unit and engage them onto connecting pipes.
(2) Flare the pipes according to table and
fi
gure shown below.
Flare dimensions for R32 are different from those for conventional refrigerant.
Although it is recommended to use the
fl
aring tools designed speci
fi
cally for R32 or R410A, conven-
tional
fl
aring tools can also be used by adjusting the dimension B with a
fl
are adjustment gauge.
A
Copper pipe
outer diameter
A
B
Copper pipe
outer diameter
B [Rigid (clutch) type]
R32 or R410A Conventional
5
3
.
6
ø
1
.
9
5
3
.
6
ø
0-0.5
1.0-1.5
2
5
.
9
ø
2
.
3
1
2
5
.
9
ø
7
.
2
1
ø
6
.
6
1
7
.
2
1
ø
8
8
.
5
1
ø
7
.
9
1
8
8
.
5
1
ø
2.2 Connecting pipes
(1) Connect pipes on both liquid and gas sides.
(2) Tighten nuts to speci
fi
ed torque shown in the table below.
(Do not turn)
Liquid side
Gas side
Operation valve size (mm)
Tightening torque (N·m)
ø6.35 (1/4")
14-18
ø9.52 (3/8")
34-42
ø12.7 (1/2")
49-61
ø15.88 (5/8")
68-82
CAUTION
• Do not apply refrigerating machine oil to the
fl
ared surface. It can cause refrigerant leakage.
• Do not apply excess torque to the
fl
ared nuts. The
fl
ared nuts may crack resulting in refrigerant
leakage.
3. Heating and condensation prevention
(1) Dress the connecting pipes (both liquid and gas pipes) with insulation to prevent it from heating and
dew condensation.
Use the heat insulating material which can withstand 120°C or higher temperature. Make sure that insu-
lation is wrapped tightly around the pipes and no gap is left between them.
(2) Wrap the refrigerant pipings of indoor unit with indoor unit heat insulation using tape.
(3) Cover the
fl
are-connected joints (indoor side) with the indoor unit heat insulation and wrap it with an in-
sulation pad (standard accessory provided with indoor unit).
(4) Wrap the connecting pipes, connecting cable and drain hose with the tape.
)
4
(
)
3
(
)
2
(
Tape
Insulation pad
Position it so that the slit area faces upward.
Connecting cable
Liquid pipe
Drain hose
Gas pipe
Insulation
Tape
NOTE
Locations where relative humidity exceeds 70%, both liquid and gas pipes need to be dressed with 20mm or
thicker heat insulation materials.
CAUTION
• Improper insulation can cause condensate(water) formation during cooling operation.
Condensate can leak or drip causing damage to household property.
• Poor heat insulating capacity can cause pipe outer surface to reach high temperature during heating
operation. It can cause cable deterioration and personal injury.
4. Finishing work
Pipe
assembly
(h)Screw
(h)Clamp
(1) Make sure that the exterior portion of connecting pipes, connecting cable
and drain hose is wrapped properly with tape. Shape the connecting pipes
to match with the contours of the pipe assembly route.
(2) Fix the pipe assembly with the wall using clamps and screws. Pipe assem-
bly should be anchored every 1.5m or less to isolate the vibration.
(3) Install the service cover securely. Water may enter the unit if service cover
is not installed properly, resulting in unit malfunction and failure.
WARNING (only for R32)
• To avoid the risk of
fi
re or explosion, the
fl
ared connection
must/shall be installed outdoors.
• Reusable mechanical connectors and
flfl
ared joints are not
allowed indoors.
CAUTION
Make sure that the connecting pipes do not touch the components within the unit. If pipes touch the
internal components, it may generate abnormal sounds and/or vibrations.
10. HOW TO OPEN, CLOSE, REMOVE AND INSTALL
THE AIR INLET PANEL
11. HOW TO REMOVE AND INSTALL FRONT PANEL
1. Open
Pull the air inlet panel at both ends of lower part
and release latches, then pull up the panel until
you feel resistance.
(The panel stops at approx. 60° open position)
2. Close
Hold the panel at both ends of lower part, lower
it downward slowly, then push it slightly until the
latch works.
3. Removing
Open the panel by 80° (as shown in the right
illustration) and then pull it forward.
4. Installing
Insert the panel arm into the slot on the front
panel from the position shown in right illustra-
tion, hold the panel at both ends of lower part,
lower it downward slowly, then push it slightly
until the latch works.
Air inlet panel
Panel arm
Approx. 80°
1. Removing
(1) Remove the air inlet panel and the air
fi
lters.
(2) Remove the 8 screws.
(3) Remove the 5 upper latches and then front
panel can be removed.
2. Installing
(1) Cover the unit with the front panel and
fi
x 5
upper latches.
(2) Secure the front panel with the 8 screws.
(3) Install the air inlet panel and the air
fi
lters.
Front panel
Air inlet panel
Air filter
Screw
Latch
E
C
A
F
R
E
T
N
I
N
A
R
O
F
N
O
I
T
C
E
N
N
O
C
L
A
N
I
M
R
E
T
.
3
1
L
O
R
T
N
O
C
E
T
O
M
E
R
G
N
I
L
L
A
T
S
N
I
.
2
1
Mount the batteries
(1) Slide and take out the cover of backside.
(2) Mount the batteries [R03 (AAA, Micro),
×2 pieces] in the body properly.
(Fit he poles with the indication marks + &
−
)
(3) Set the cover again.
NOTE
• Do not use new and old batteries together.
• In case the unit is not operated for a long time,
take out the batteries
Installing remote control holder
(1) Select the place where the unit can receive
signals.
(2) Fix the holder to pillar or wall with wood
screws.
To install wired remote control,
superlink etc., interface kit is
needed.
(1) Remove the air inlet panel and
front panel.
(2) Remove the control cover.
(Remove the screw.)
(3) There is a terminal
(respectively marked with CNS)
for the indoor control board.
While connecting an interface,
connect to the respective
terminal securely with the
connection harness supplied
with an optional “Interface
connection kit SC-BIKN-E and
SC-BIKN2-E” and fasten the
connection harness onto the
indoor control box with the
clamp and screw supplied with
the kit.
For more details, refer to the
user’s manual of “Interface
connection kit SC-BIKN-E and
SC-BIKN2-E”.
Indoor unit PCB
Screw
Control cover
CNS terminal
Cover
Wood screws
ø3.5 X 16
Remote control
Battery
14. INSTALLING TWO AIR-CONDITIONERS IN THE SAME ROOM
15. PUMP DOWN WORK
In case two air-conditioners are installed in the same room, apply this setting so that one unit can be
operated with only one remote control.
For the environmental protection, be sure to pump down when relocating or disposing of the unit. Pump
down is the method of recovering refrigerant from the indoor unit to the outdoor unit before the connect-
ing pipes are removed from the unit. When pump down is carried out, forced cooling operation is needed.
Setting one remote control
(1) Slide and take out the cover and batteries.
(2) Cut the switching line next to the battery
with wire cutters.
(3) Set the batteries and cover again.
Cut
Setting one indoor unit
(1) Turn off the power source and turn it on after
1 minute.
(2) Send the signal by pressing the ACL switch
on the remote control that was set according
to the procedure described on the left side.
(3) Check that the reception buzzer sound
“peep” is emitted from the indoor unit. Since
the signal is sent about 6 seconds after the
ACL switch is pressed, point the remote
control to the indoor unit for a while.
NOTE
If no reception buzzer is emitted, restart the set-
ting from the beginning.
Reception
peep
TIME SET
UP ACL
Forced cooling operation
(1) Turn off the power source and turn it on
again after 1 miniute.
(2) Press the ON/OFF button continuously for at
least 5 seconds. Then operation will start.
For the detail of pump down, refer to the instal-
lation manual of outdoor unit.
Unit ON/OFF button
16. INSTALLATION CHECK AND TEST RUN
After
fi
nishing the installation work, check the following points again before turning on the power. Conduct a test run and ensure that the unit operates properly.
At the same time, explain to the customer how to use the unit and how to take care of the unit following the user’s manual.
Before test run
Before test run, check following points.
Power source voltage complies with the rated voltage of
air-conditioner.
Earth leakage breaker and circuit breaker are installed.
Power cable and connecting cable are securely
fi
xed to
the terminal block.
Both liquid and gas operation valves are fully open.
No gas leaks from the joints of the operation valves.
Indoor and outdoor side pipe joints have been insulated.
Hole on the wall is completely sealed with putty.
Drain hose and cap are installed properly.
Screw of the lid is tightened securely.
Test run
Check following points during test run.
Indoor unit receives signal of remote control.
Air-conditioning operation is normal.
There is no abnormal noise.
Water drains out smoothly.
Display of remote control is normal.
After test run
Explain the operating and maintenance methods to the
user according to the user’s manual.
Keep this installation manual together with user’s
manual.
NOTE
During restart or change in operation mode, the unit will not start
operating for approximately 3 minutes. This is to protect the unit
and it is not malfunction.
RLD012A018
Wall
Seal hole with putty
Flared joint outside
for indoor unit
Indoor
unit
Wall hole cover
Right
Rear
Downward
Left
rear
Left downward
Left
RLD012A018.indd 2
5/31/2018 10:18:44 AM