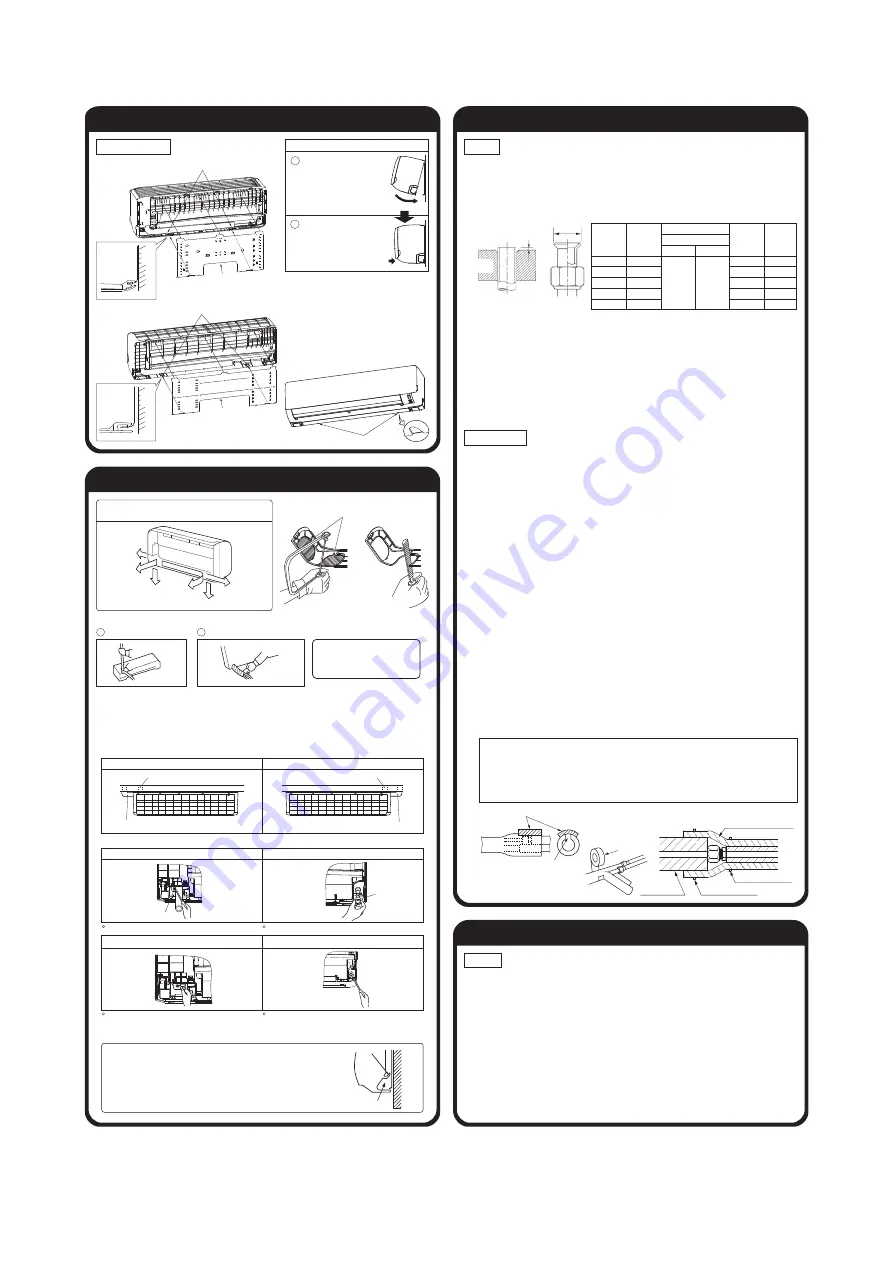
–
–
'17 • KX-T-259
⑨
Check list after installation
Check the following items after all installation work completed.
Check if;
The indoor and outdoor units are fixed securely?
Inspection for leakage is done?
Insulation work is properly done?
Water is drained properly?
Power source voltage is same as mentioned in the model name plate ?
There is mis-wiring or mis-connection of piping?
Earth wiring is connected properly?
Cable size comply with specified size?
Any obstacle blocks air flow on air inlet and outlet?
Check
Expected trouble
Falling, vibration, noise
Insufficient capacity
Water leakage
Water leakage
PCB burnt out, not working at all
PCB burnt out, not working at all
Electric shock
PCB burnt out, not working at all
Insufficient capacity
④
Installation of indoor unit (continued)
⑧
Wiring-out position and wiring connection (continued)
⑥
Refrigerant pipe
⑦
Drain pipe (continued)
Be sure to use new pipes for the refrigerant pipes. Use the flare nut attached to the product or
a nut compatible with JIS B 8607, Class 2.
Regarding whether existing pipes can be reused or not, and the washing method, refer to the instruction manual of the
outdoor unit, catalogue or technical data.
1) In case of reuse: Do not use old flare nut, but use the one attached to the unit or compatible with JIS B 8607, Class 2.
2) In case of reuse: Flare the end of pipe replaced partially for R410A.
Use phosphorus deoxidized copper alloy seamless pipe (C1220T specified in JIS H3300) for refrigeration pipe installation.
In addition, make sure there is no damage both inside and outside of the pipe, and no harmful
substances such as sulfur, oxide, dust or a contaminant stuck on the pipes.
Do not use any refrigerant other than R410A.
Using other refrigerant except R410A (R22 etc.) may degrade inside refrigeration oil. And air getting into
refrigeration circuit may cause over-pressure and resultant it may result in bursting, etc.
Store the copper pipes indoors and seal the both end of them until they are brazed in order to avoid any dust, dirt or
water getting into pipe. Otherwise it will cause degradation of refrigeration oil and compressor breakdown, etc.
Use special tools for R410A refrigerant.
Address setting
Remove the front panel of indoor unit and the control cover, it is possible to change address setting.
1. Remove the front panel
①
Remove the air inlet panel.
②
Remove the 2 screws in the cap of bottom panel. (Type 15 - 56 only)
③
Remove the 2 hooks of left and right side and then bottom panel can be removed. (Type 15
- 56 only)
④
Remove the screws (Type 15 - 56: 2 screws, Type 71, 90: 5 3 screws (in the cap))
⑤
Remove the upper latches and then front panel can be removed. (Type 15 - 56: 4 latches,
Type 71, 90: 5 latches)
2. Install the front panel
①
Cover the unit with the front panel and fix upper latches (Type 15 - 56: 4 latches, Type 71,
90: 5 latches)
②
Fix the front panel with the screws (Type 15 - 56: 2 screws, Type 71, 90: 5 3 screws
(in the cap))
③
Install the 2 hooks of left and right side and then bottom panel can be installed. (Type 15 - 56
only)
④
Fix the bottom panel with 2 screws in the cap. (Type 15 - 56 only)
⑤
Install the air inlet panel.
Caution
D
Protruding
dimension
Flare die
d
mm
6.35
9.52
12.7
15.88
19.05
For R410A Conventional tool
Pipe dia.
Min. pipe
wall thickness
Protruding dimension for flare, mm
Rigid (Clutch type)
Flare O.D.
Flare nut
tightening torque
0
-
0.5
0.7
-
1.3
D
mm
8.9
-
9.1
12.8
-
13.2
16.2
-
16.6
19.3
-
19.7
23.6
-
24.0
N·m
14
-
18
34
-
42
49
-
61
68
-
82
100
-
120
mm
0.8
0.8
0.8
1
1.2
1. Remove the flare nut and blind flanges on the pipe of the indoor unit.
※
Make sure to loosen the flare nut with holding the nut on pipe side with a spanner and giving torque to the
nut with another spanner in order to avoid unexpected stress to the copper pipe, and then remove them.
(Gas may come out at this time, but it is not abnormal.)
Pay attention whether the flare nut pops out. (as the indoor unit is sometimes pressured.)
2. Make a flare on liquid pipe and gas pipe, and connect the refrigeration pipes on the indoor unit.
※
Bend radius of pipe must be 4D or larger. Once a pipe is bent, do not readjust the bending.
Do not twist a pipe or collapse to 2/3D or smaller.
※
Do a flare connection as follows:
Make sure to loosen the flare nut with holding the nut on pipe side with a spanner and giving
torque to the nut with another spanner in order to avoid unexpected stress to the copper pipe,
and then remove them.
When fastening the flare nut, align the refrigeration pipe with the center of flare nut, screw
the nut for 3-4 times by hand and then tighten it by spanner with the specified torque
mentioned in the table above. Make sure to hold the pipe on the indoor unit securely by a
spanner when tightening the nut in order to avoid unexpected stress on the copper pipe.
3. Cover the indoor unit’s flare-connected joints, after they are checked for a gas leak, with an
indoor unit heat insulating material and then wrap them with a tape with an attached insula-
tion pad placed over the heat insulating material’s slit area.
Make sure to insulate both gas pipes and liquid pipes completely.
※
Incomplete insulation may cause dew condensation or water dropping.
Use heat-resistant (120 °C or more) insulations on the gas side pipes.
In case of using at high humidity condition, reinforce insulation of refrigerant pipes.
Surface of insulation may cause dew condition or water dropping, if insulations are not
reinfoced.
4. Refrigerant is charged in the outdoor unit.
As for the additional refrigerant charge for the indoor unit and piping, refer to the installation
manual attached to the outdoor unit.
Work procedure
Refrigerating machine oil should not be applied to the threads of union or external surface of flare. It
is because, even if the same tightening torque is applied, the oil is likely to decrease the slide friction
force on the threads and increase, in turn, the axial component force so that it could crack the flare
by the stress corrosion.
Refrigerating machine oil may be applied to the internal surface of flare only.
Caution:
Arrange the drain hose in a downward angle
Avoid the following drain piping.
When the extended drain hose is present inside the room, always use a shield pipe (prepare
on site) and ensure it is thermally insulated
Shield pipe
Drain hose
Extended drain hose
When it is exposed indoor.
3 Pour water to the drain pan located under the heat exchanger, and ensure that water is discharged
the outdoor.
(For removal of the front panel, refer to
⑧
Wiring-out position and wiring connection
in this manual.
1. A general-purpose hard PVC pipe VP16 can be connected to the drain hose tip as a part of
drain piping.
2. Drain piping must be given a descending grade so that drain water may flow smoothly and it
must not have any trap or bump within the system.
(The pipe can be routed through the left, right, rear or bottom of the unit)
Hard PVC pipes (VP16) laid indoors must be kept warm.
⑦
Drain pipe
Caution
Install the drain pipe according to the installation manual in order to drain properly.
Imperfection in draining may cause flood indoors and wetting the household goods,etc.
Do not put the drain pipe directly into the ditch where toxic gas such as sulfur, the other harmful and
inflammable gas is generated. Toxic gas would flow into the room and it would cause serious
damage to user’s health and safety (some poisoning or deficiency of oxygen). In addition, it may
cause corrosion of heat exchanger and bad smell.
Connect the pipe securely to avoid water leakage from the joint.
Insulate the pipe properly to avoid condensation drop.
Check if the water can flow out properly from both the drain outlet on the indoor unit and the end
of the drain pipe after installation.
Make sure to make descending slope of greater than 1/100 and do not make up-down bend and/or trap in
the midway. In addition, do not put air vent on the drain pipe. Check if water is drained out properly from
the pipe during commissioning. Also, keep sufficient space for inspection and maintenance.
Fixing of indoor unit
Shaping of pipes and drain hoses
<In case of piping in the right rear direction>
Shaping of pipes
Tape wrapping
Pipe
Drain hose
Make sure that wires are connected
securely onto the terminal block,
before you wrap them with a tape
after shaping the pipe.
Installation
board
Indoor unit base latch
Wall
Installation board
Indoor unit
Latch (2 locations)
Installation board
Installation
board
Indoor unit base latch
Wall
Indoor unit
Latch (2 locations)
Type 71, 90
Type 15~56
t)PXUPSFNPWFUIFJOEPPSVOJUGSPN
the
installation board
①
Push up at the marked portion of the indoor unit
base lower latch, and slightly pull it toward you.
(both right and left hand sides) (The indoor unit
base lower latch can be removed from the
installation board)
②
Push up the indoor unit upward so that it can be
removed from installation board.
Latch
2
1
Gently push the lower part to
secure the unit.
Pass the pipe through the hole
in the wall, and hook the upper
part of the indoor unit to the
installation board.
Cut out the panel smoothly along the
line in case of side or bottom piping.
Piping is possible in the rear, left, left rear, left downward,
right or downward direction.
Right
Right rear
Right
downward
Left
rear
Left downward
Left
Tape only the portion that goes through the wall.
Always tape the wiring with the piping.
The connecting wires must be wrapped together with the pipe.
Hold the bottom of the
piping and fix direction
before stretching it and
shaping it.
Piping in the left direction
Piping in the right rear direction
Piping in the left rear direction
Piping in the right direction
[Top view]
t.BUUFSTPGTQFDJBMOPUJDFXIFOQJQJOHGSPNMFGUPSDFOUSBMSFBSPG
the unit.
Left-hand-side piping
Right-hand-side piping
[Drain hose changing procedures]
1. Remove the drain hose
2. Remove the drain cap.
Remove it with hand or pliers.
Remove the screw and drain hose, making it rotate.
3. Insert the drain cap.
4. Connect the drain hose.
Insert the drain cap which was removed at procedure “2”
securely using a hexagonal wrench etc.
Note: Be careful that If it is not inserted securely, water
leakage may occur.
Insert the drain hose securely, making rotate. And install the
screw.
Note: Be careful that If it is not inserted securely, water
leakage may occur.
screw
cap
Band (Prepare on site)
Band (Prepare on site)
Insulation
(Prepare on site)
Pipe cover (Prepare on site)
<The case of using reinforced insulation at the outside of unit>
Vinyl tape
Use an attached insulation pad for heat insulation.
Position it so that the slit area faces upward.
Higher than specified
Wavy
The drain hose
tip is in water.
The gap to the ground is
5 cm or less.
The drain hose
tip is in the gutter.
Odor from
the gutter
Electrical installation work must be performed according to the installation manual by an
electrical installation service provider qualified by a power provider of the country, and be
executed according to the technical standards and other regulations applicable to electrical
installation in the country.
Be sure to use an exclusive circuit.
Use specified cord, fasten the wiring to the terminal securely, and hold the cord securely in
order not to apply unexpected stress on the terminal.
Do not put both power source line and signal line on the same route. It may cause miscom-
munication and malfunction.
Be sure to do D type earth work.
●
●
●
●
●
●
●
●
●
●
●
●
●
●
●
●
●
●
●
●
●
●
●
●
●
●
●
●
For the details of electrical wiring work, see attached instruction manual for electrical wiring
work.
⑧
Wiring-out position and wiring connection
Signal side
terminal block
Power source side
terminal block
Earth
Band
Band
Superlink line
Remote control line
Power source line
In case of band is over length,
cut off the band.
①
Pull the air inlet panel at both ends of lower part and release latches, then pull up the panel until
you feel resistance. (The panel stops at approx 60 - 70° open position.)
②
Remove the screw and the lid.
③
Connect wiring securely to the terminal block.
④
Fix wiring the clamp securely, in order not to transmit unexpected stress on the terminal.
⑤
Fix the lid and the screw.
⑥
Close the air inlet panel.
(Note)
Connect wiring to the terminal block, check number on label of the terminal block.
Wall
Gutter
Pipe accommodating section
Since this air-conditioner has been designed to collect dew drops on the rear
surface to the drain pan, do not attach the power cable above the gutter.
Installation Steps
Signal side
terminal block
Power source side
terminal block
Earth
Band
Band
Superlink line
Remote control line
Power source line
PHA012D401
Type 15-56
Type 15-56
Type 71, 90
Type 15-56
Type 71, 90
Type 71, 90
Air inlet panel
Front panel
Front panel
Air inlet panel
Screw
Screw (in the cap)
Latch
Screw
Screw
Control cover
Control cover
Address switch
Bottom panel
Screw (in the cap)
Screw
Latch
Address switch
Lid
Type 15-56
Type 71, 90
Lid
⑤