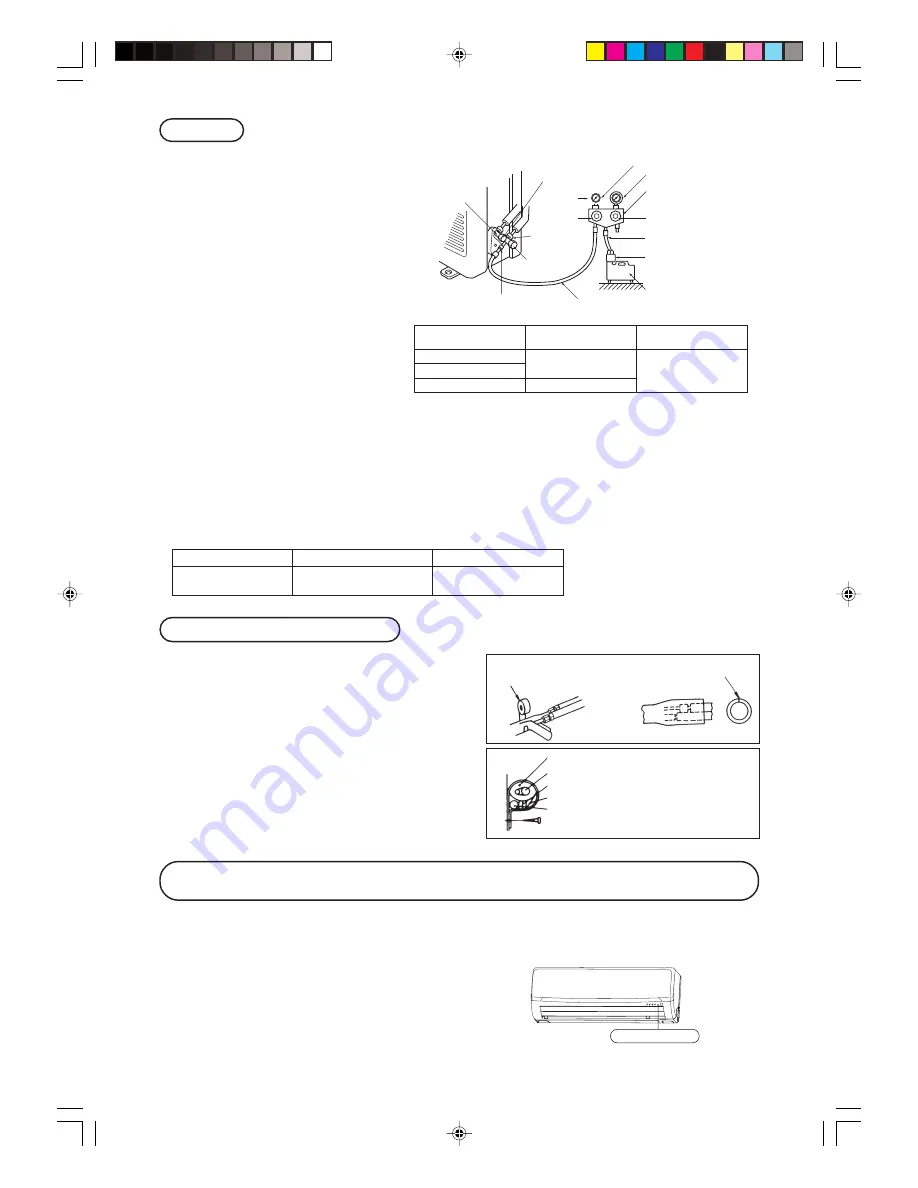
– 33 –
Insulation of connecting portion
1
Cover the connection portion of the refrigerant piping with the
pipe cover and seal them.
If neglecting to do so, moisture occurs on the piping and water
will drip out.
2
Finishing and fixing
a
Tie up the piping with wrapping tape, and shape it so that it conforms
to which the pipe is attached.
b
Fix them with clamps as right figure.
Vinyl tape
To cover the connecting portion with insula-
tion materials, cut upper portion and then seal
it with insulation materials.
Cover the exterior portion with cov-
ering tape and shape the piping so it
will match the contours of the route
that the piping to take. Also fix the
wiring and pipings to the wall with
clamps.
Insulation
Refrigerant piping
Electrical wiring
Covering tape
Drain hose
Tapping screw
♦
Additional refrigerant charge
Air purge
1
Tighten all flare nuts in the pipings both
indoor and outside wall so as not to
cause leak.
2
Connect service valve, charge hose,
manifold valve and vacuum pump as is
illustrated below.
3
Open manifold valve handle Lo to its
full width, and perform vacuum or
evacuation.
Continue the vacuum or evacuation op-
eration for 15 minutes or more and
check to see that the vacuum gauge
reads – 0.1 MPa (– 76 cmHg).
4
After completing vacuum operation,
fully open service valve (Both gas and
liquid sides) with hexagon headed
wrench.
5
Detach the charge hoses.
6
Check for possible leakage of gas in the
connection parts of both indoor and out-
door.
(three-way valve)
Charge hose (Designed specifically for R410A)
Compound pressure gauge
Pressure gauge
Gauge manifold
(Designed specifically for R410A)
Handle Hi
Vacuum pump
Vacuum pump adapter
(Anti-reverse flow type)
(Designed specifically for R410A)
Charge hose
(Designed specifically for R410A)
Check joint
-0.1MPa
(-76cmHg)
Handle Lo
Operation valve
Operation valve
(two-way valve)
Operation valve
cap
Operation valve
cap
Operation valve cap
tightening torque (N•m)
Check joint blind nut
tightening torque (N•m)
ø6.35 (1/4")
ø9.52 (3/8")
10~12
ø12.7 (1/2")
25~35
20~30
Operation valve size
(mm)
Securely tighten the operation valve cap and the check joint blind nut after adjustment.
¡
Since the system uses check joints differing in diameter from those found on the conventional models, a charge hose (for R22) presently in use is
not applicable.
Please use one designed specifically for R410A.
¡
Please use an anti-reverse flow type vacuum pump adapter so as to prevent vacuum pump oil from running back into the system.
Oil running back into an air-conditioning system may cause the refrigerant cycle to break down.
Model
SRK/C10YL-S, 13YL-S
SRK/C18YL-S
Additional refrigerant
Less than 15m : Not required
Not required
more than 15m : 20g/m
How to relocate or dispose of the unit
•
In order to protect the environment, be sure to pump down (recovery of
refrigerant).
•
Pump down is the method of recovering refrigerant from the indoor unit
to the outdoor unit when the pipes are removed from the unit.
<How to pump down>
1
Connect charge hose to check joint.
2
Liquid side : Close the liquid valve with hexagon wrench key.
Gas side : Fully open the gas valve.
Carry out cooling operation. (If indoor temperature is low, operate
forced cooling operation.)
3
After low pressure gauge become 0.01MPa, stop cooling operation and
close the gas valve.
¡
Forced cooling operation
Turn on a power supply again after a while after turn
off a power supply. Then press continually the ON/
OFF button 5 seconds or more.
Unit ON/OFF button
Summary of Contents for SRK10YL-S
Page 25: ... 24 ...