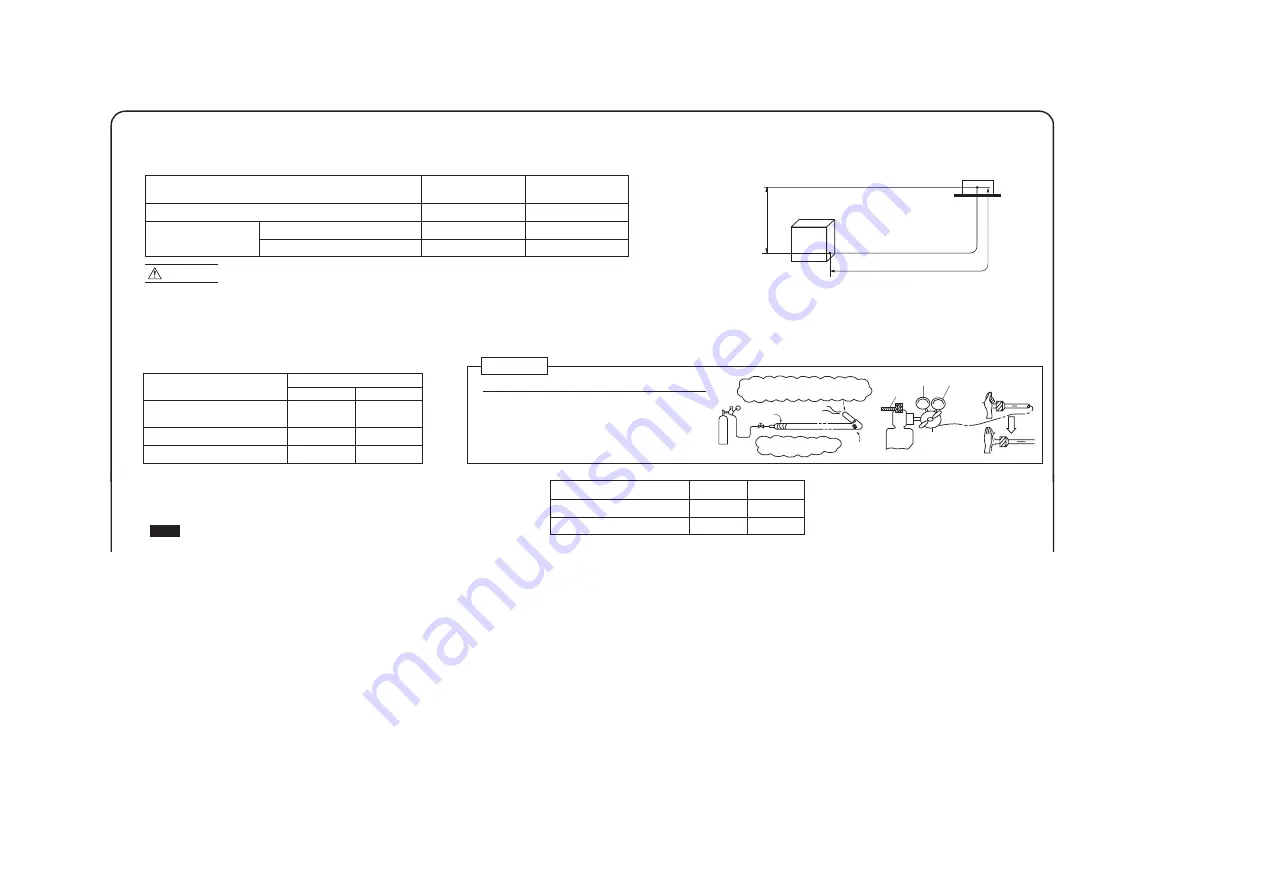
-
279
-
'13 • P
A
C-T
-197
INSTALLATION MANUAL FOR OUTDOOR UNIT
RWC012A038
Accessories for outdoor unit
• Model name and power source
• Refrigerant piping length
• Piping, wiring and miscellaneous small parts
• Indoor unit installation manual
Necessary tools for the installation work
Wrench key (Hexagon) [4m/m]
Vacuum pump
Vacuum pump adapter (Anti-reverse flow type)
(Designed specifically for R410A)
Gauge manifold (Designed specifically for R410A)
Charge hose (Designed specifically for R410A)
Flaring tool set (Designed specifically for R410A)
Gas leak detector (Designed specifically for R410A)
Gauge for projection adjustment
(Used when flare is made by using conventional flare tool)
9
10
11
12
13
14
15
16
Plus headed driver
Knife
Saw
Tape measure
Hammer
Spanner wrench
Torque wrench [14.0
~
62.0N·m (1.4
~
6.2kgf·m)]
Hole core drill (65mm in diameter)
1
2
3
4
5
6
7
8
Grommet (Heat pump type only)
Drain elbow (Heat pump type only)
Q’ty
4
1
1
2
Option parts
Sealing plate
Sleeve
Inclination plate
Putty
Drain hose (extension hose)
Piping cover
(for insulation of connection piping)
Q’ty
1
1
1
1
1
1
Check before installation work
a
b
c
d
e
f
1. HAULAGE AND INSTALLATION
(Take particular care in carrying in or moving the unit, and always perform such an operation with two or more persons.)
Intake
The height of a wall is 1200mm or less.
(
service
space
)
Intake
Outlet
CAUTION
When a unit is hoisted with slings for haulage, take into consideration the offset of its gravity center position.
If not properly balanced, the unit can be thrown off-balance and fall.
1) Delivery
2) Portage
3) Selecting the installation location
5) Installation space
L
3
L
2
L
4
L
1
Model 40, 50, 60
Example installation
Size
L1
L2
L3
L4
Open
100
100
250
280
75
80
Open
280
Open
80
250
180
Open
80
Open
(mm)
I
II
III
IV
6) Installation
Pad
Over 500mm
• Deliver the unit as close as possible to the installation site before removing it from
the packaging.
• When you have to unpack the unit for a compelling reason before you haul it to
the installation point, hoist the unit with nylon slings or ropes and protection pads
so that you may not damage the unit.
• The right hand side of the unit as viewed from the front (diffuser side) is heavier.
A person carrying the right hand side must take heed of this fact. A person
carrying the left hand side must hold with his right hand the handle provided on
the front panel of the unit and with his left hand the corner column section.
(1) If the unit is installed in the area where the snow will accumulate, following measures are required.
The bottom plate of unit and intake, outlet may be blocked by snow.
1 Install the unit on the base so that the bottom is
higher than snow cover surface.
Since drain water generated by defrost control may freeze, following measures are required.
• Do not execute drain piping work by using a drain elbow and drain grommets (accessories).
[Refer to Drain piping work.]
Determine refrigerant pipe size pursuant to the following guidelines
based on the indoor unit specifications.
Without nitrogen gas, a large quantity of foreign matters
(oxidized film) are created, causing a critical failure from
capillary tube or expansion valve clogging.
2 Install the unit under or provide the roof on site.
Be sure to select a suitable installation place in consideration of following conditions.
• A place where it is horizontal, stable and can endure the unit weight and will not allow vibration transmittance
of the unit.
• A place where it can be free from possibility of bothering neighbors due to noise or exhaust air from the unit.
• A place where the unit is not exposed to oil splashes.
• A place where it can be free from danger of flammable gas leakage.
• A place where drain water can be disposed without any trouble.
• A place where the unit will not be affected by heat radiation from other heat source.
• A place where snow will not accumulate.
• A place where the unit can be kept away 5m or more from TV set and/or radio receiver in order to avoid any
radio or TV interference.
• A place where good air circulation can be secured, and enough service space can be secured for maintenance
and service of the unit safely.
• A place where the unit will not be affected by electromagnetic waves and/or high-harmonic waves generated
by other equipment.
• A place where chemical substances like sulfuric gas, chloric gas, acid and alkali (including ammonia), which
can harm the unit, will not be generated and not remain.
• If a operation is conducted when the outdoor air temperature is -5 lower, the outdoor unit should be installed
at a place where it is not influenced by natural wind.
• A place where strong wind will not blow against the outlet air blow of the unit.
2. REFRIGERANT PIPING WORK
1) Restrictions on unit installation and use
2) Determination of pipe size
30m or less
20m or less
20m or less
L
H
H
L
H
Outdoor unit
Indoor unit
Restrictions
Marks appearing in the
drawing on the right
Main pipe length
When the outdoor unit is positioned higher,
When the outdoor unit is positioned lower,
Elevation difference between
indoor and outdoor units
Plug the end of the pipe with tape, or other
material, and fill the pipe with nitrogen gas.
Only use nitrogen gas (N
2
)
Taping
<N2>
Nitrogen
Brazing
Station valve
Primary side
Secondary side
0.5MPa
Hand
Relief valve
Nitrogen
gas
Brazing must be performed under a nitrogen gas flow.
About brazing
When pipe is brazing.
4) Caution about selection of installation location
• Walls surrounding the unit in the four sides are not
acceptable.
• There must be a 1-meter or larger space in the above.
• When more than one unit are installed side by side,
provide a 250mm or wider interval between them as a
service space. In order to facilitate servicing of
controllers, please provide a sufficient space between
units so that their top plates can be removed easily.
• Where a danger of short-circuiting exists, install guide
louvers.
• When more than one unit are installed, provide sufficient
intake space consciously so that short-circuiting may not
occur.
• Where piling snow can bury the outdoor unit, provide
proper snow guards.
1 Anchor bolt fixed position
Fasten with bolts
(M10-12)
Use a thicker block to anchor deeper.
Use a long block to extend the width.
• In installing the unit, fix the unit’s legs with bolts specified on the above.
• The protrusion of an anchor bolt on the front side must be kept within 15mm.
• Securely install the unit so that it does not fall over during earthquakes or strong winds, etc.
• Refer to the above illustrations for information regarding concrete foundations.
• Install the unit in a level area. (With a gradient of 5mm or less.) Improper installation can result in a
compressor failure, broken piping within the unit and abnormal noise generation.
2 Notabilia for installation
(2) If the unit can be affected by strong wind, following measures are required.
Strong wind can cause damage of fan (fan motor), or can cause performance degradation, or can trigger
anomalous stop of the unit due to rising of high pressure.
1 Place the unit outlet side is turned to the wall.
2 Install so the direction of the air from the
blowing outlet will be perpendicular to the
direction of the wind.
• Check the following points in light of the indoor unit specifications and the installation site.
• Observe the following restrictions on unit installation and use. Improper installation can result in a compressor failure or performance degradation.
• The use restrictions appearing in the table above are applicable to the standard pipe size combinations shown in the table below.
Where an existing pipe system is utilized, different one-way pipe length restrictions should apply depending on its pipe size.
For more information, please see “5. UTILIZATION OF EXISTING PIPING.”
Dimensional restrictions
ø12.7
Flare
ø12.7
ø12.7
Gas pipe
ø6.35
Flare
ø6.35
ø6.35
Model 40, 50, 60
Liquid pipe
Outdoor unit connected
Refrigerant piping (branch pipe L)
Indoor unit connected
Notabilia as a unit designed for R410A
• Do not use any refrigerant other than R410A. R410A will rise to pressure about 1.6 times higher than that of a conventional refrigerant.
A cylinder containing R410A has a pink indication mark on the top.
• A unit designed for R410A has adopted a different size indoor unit operation valve charge port and a different size check joint provided in the unit to prevent the charging of a wrong refrigerant by mistake.
The processed dimension of the flared part of a refrigerant pipe and a flare nut’s parallel side measurement have also been altered to raise strength against pressure.
Accordingly, you are required to arrange dedicated R410A tools listed in the table on the left before installing or servicing this unit.
• Do not use a charge cylinder. The use of a charge cylinder will cause the refrigerant composition to change, which results in performance degradation.
• In charging refrigerant, always take it out from a cylinder in the liquid phase.
• All indoor units must be models designed exclusively for R410A. Check connectable indoor unit models in a catalog, etc. (A wrong indoor unit, if connected into the system, will impair proper system operation)
CAUTION
• Read the “SAFETY PRECAUTIONS” carefully first of all and strictly follow it during the installation work in order
to protect yourself.
• The precautionary items mentioned below are distinguished into two levels, and
.
: Wrong installation would cause serious consequences such as injuries or death.
: Wrong installation might cause serious consequences depending on circumstances.
Both mentions the important items to protect your health and safety so strictly follow them by any means.
• Be sure to confirm no anomaly on the equipment by commissioning after completed installation and explain the
operating methods as well as the maintenance methods of this equipment to the user according to the owner’s
manual.
• Keep the installation manual together with owner’s manual at a place where any user can read at any time.
Moreover if necessary, ask to hand them to a new user.
• For installing qualified personnel, take precautions in respect to themselves by using suitable protective
clothing, groves, etc., and then perform the installation works.
• Please pay attention not to fall down the tools, etc. when installing the unit at the high position.
• If unusual noise can be heard during operation, consult the dealer.
• The meanings of “Marks” used here are shown as follows:
• This installation manual deals with outdoor units and general installation specifications only. For indoor units, refer to page 212.
• When install the unit, be sure to check whether the selection of installation place, power supply specifications, usage limitation (piping length, height differences between indoor and outdoor units, power
supply voltage and etc.) and installation spaces.
SAFETY PRECAUTIONS
WARNING
Never do it under any circumstances.
Always do it according to the instruction.
CAUTION
WARNING
CAUTION
WARNING
CAUTION
• Carry out the electrical work for ground lead with care.
Do not connect the ground lead to the gas line, water line, lightning conductor or telephone line’s ground lead. Incorrect grounding can cause unit faults such as electric shocks due to short-circuiting.
• Installation must be carried out by the qualified installer.
If you install the system by yourself, it may cause serious trouble such as water leaks,
electric shocks, fire and personal injury, as a result of a system malfunction. Do not
carry out the installation and maintenance work except the by qualified installer.
• Install the system in full accordance with the installation manual.
Incorrect installation may cause bursts, personal injury, water leaks, electric
shocks and fire.
• Be sure to use only for household and residence.
If this appliance is installed in inferior environment such as machine shop and etc.,
it can cause malfunction.
• When installing in small rooms, take prevention measures not to
exceed the density limit of refrigerant in the event of leakage, referred
by the formula (accordance with ISO5149).
If the density of refrigerant exceeds the limit, please consult the dealer and install
the ventilation system, otherwise lack of oxygen can occur, which can cause serious
accident.
• Use the original accessories and the specified components for
installation.
If parts other than those prescribed by us are used, It may cause water leaks,
electric shocks, fire and personal injury.
• Install the unit in a location with good support.
Unsuitable installation locations can cause the unit to fall and cause material
damage and personal injury.
• Ensure the unit is stable when installed, so that it can withstand
earthquakes and strong winds.
Unsuitable installation locations can cause the unit to fall and cause material
damage and personal injury.
• Ventilate the working area well in the event of refrigerant leakage during
installation.
If the refrigerant comes into contact with naked flames, poisonous gas is produced.
• Use the prescribed pipes, flare nuts and tools for R410A.
Using existing parts (for R22 or R407C) can cause the unit failure and serious
accidents due to burst of the refrigerant circuit.
• Tighten the flare nut by torque wrench with specified method.
If the flare nut were tightened with excess torque, this may cause burst and
refrigerant leakage after a long period.
• Do not open the operation valves for liquid line and gas line until
completed refrigerant piping work, air tightness test and evacuation.
If the compressor is operated in state of opening operation valves before
completed connection of refrigerant piping work, air can be sucked into refrigerant
circuit, which can cause bust or personal injury due to anomalously high pressure
in the refrigerant.
• The electrical installation must be carried out by the qualified electrician
in accordance with “the norm for electrical work” and “national wiring
regulation”, and the system must be connected to the dedicated circuit.
Power supply with insufficient capacity and incorrect function done by improper
work can cause electric shocks and fire.
• Be sure to shut off the power before starting electrical work.
Failure to shut off the power can cause electric shocks, unit failure or incorrect
function of equipment.
• Be sure to use the cables conformed to safety standard and cable
ampacity for power distribution work.
Unconformable cables can cause electric leak, anomalous heat production or fire.
• This appliance must be connected to main power supply by means of a
circuit breaker or switch (fuse:16A) with a contact separation of at least
3mm.
• Arrange the wiring in the control box so that it cannot be pushed up
further into the box. Install the service panel correctly.
Incorrect installation may result in overheating and fire.
• Use the prescribed cables for electrical connection, tighten the cables
securely in terminal block and relieve the cables correctly to prevent
overloading the terminal blocks.
Loose connections or cable mountings can cause anomalous heat production or fire.
• Be sure to fix up the service panels.
Incorrect fixing can cause electric shocks or fire due to intrusion of dust or water.
• Be sure to switch off the power supply in the event of installation,
inspection or servicing.
If the power supply is not shut off, there is a risk of electric shocks, unit failure or
personal injury due to the unexpected start of fan.
• Stop the compressor before removing the pipe after shutting the
operation valve on pump down work.
If the pipe is removed when the compressor is in operation with the operation valve
open, air would be mixed in the refrigeration circuit and it could cause explosion
and injuries due to abnormal high pressure in the cooling cycle.
• Only use prescribed option parts. The installation must be carried out
by the qualified installer.
If you install the system by yourself, it can cause serious trouble such as water
leaks, electric shocks, fire.
• Be sure to wear protective goggles and gloves while at work.
• Earth leakage breaker must be installed.
If the earth leakage breaker is not installed, it can cause electric shocks.
• Ensure that no air enters in the refrigerant circuit when the unit is
installed and removed.
If air enters in the refrigerant circuit, the pressure in the refrigerant circuit
becomes too high, which can cause burst and personal injury.
• Do not processing, splice the power cord, or share a socket with other power plugs.
This may cause fire or electric shock due to defecting contact, defecting insulation
and over-current etc.
• Do not bundling, winding or processing for the power cord. Or, do not
deforming the power plug due to tread it.
This may cause fire or heating.
• Do not run the unit with removed panels or protections.
Touching rotating equipments, hot surfaces or high voltage parts can cause
personal injury due to entrapment, burn or electric shocks.
• Do not perform any change of protective device itself or its setup
condition.
The forced operation by short-circuiting protective device of pressure switch and
temperature controller or the use of non specified component can cause fire or
burst.
• Use the circuit breaker for all pole correct capacity. Circuit breaker
should be the one that disconnect all poles under over current.
Using the incorrect circuit breaker, it can cause the unit malfunction and fire.
• Install isolator or disconnect switch on the power supply wiring in
accordance with the local codes and regulations.
The isolator should be locked in OFF state in accordance with EN60204-1.
• After maintenance, all wiring, wiring ties and the like, should be returned
to their original state and wiring route, and the necessary clearance from
all metal parts should be secured.
• Secure a space for installation, inspection and maintenance specified in
the manual.
Insufficient space can result in accident such as personal injury due to falling from
the installation place.
• Take care when carrying the unit by hand.
If the unit weights more than 20kg, it must be carried by two or more persons. Do
not carry by the plastic straps, always use the carry handle when carrying the unit
by hand. Use gloves to minimize the risk of cuts by the aluminum fins.
• Dispose of any packing materials correctly.
Any remaining packing materials can cause personal injury as it contains nails and
wood. And to avoid danger of suffocation, be sure to keep the plastic wrapper
away from children and to dispose after tear it up.
• Be sure to insulate the refrigerant pipes so as not to condense the
ambient air moisture on them.
Insufficient insulation can cause condensation, which can lead to moisture
damage on the ceiling, floor, furniture and any other valuables.
• When perform the air conditioner operation (cooling or drying operation)
in which ventilator is installed in the room. In this case, using the air
conditioner in parallel with the ventilator, there is the possibility that
drain water may backflow in accordance with the room lapse into the
negative pressure status. Therefore, set up the opening port such as
incorporate the air into the room that may appropriate to ventilation (For
example; Open the door a little). In addition, just as above, so set up the
opening port if the room lapse into negative pressure status due to
register of the wind for the high rise apartment etc.
• Do not install the unit in the locations listed below.
•Locations where carbon fiber, metal powder or any powder is floating.
•Locations where any substances that can affect the unit such as sulphide gas,
chloride gas, acid and alkaline can occur.
•Vehicles and ships.
•Locations where cosmetic or special sprays are often used.
•Locations with direct exposure of oil mist and steam such as kitchen and
machine plant.
•Locations where any machines which generate high frequency harmonics are
used.
•Locations with salty atmospheres such as coastlines.
•Locations with heavy snow (If installed, be sure to provide base flame and snow
hood mentioned in the manual).
•Locations where the unit is exposed to chimney smoke.
•Locations at high altitude (more than 1000m high).
•Locations with ammonic atmospheres.
•Locations where heat radiation from other heat source can affect the unit.
•Locations without good air circulation.
•Locations with any obstacles which can prevent inlet and outlet air of the unit.
•Locations where short circuit of air can occur (in case of multiple units
installation).
•Locations where strong air blows against the air outlet of outdoor unit.
•Locations where something located above the unit could fall.
It can cause remarkable decrease in performance, corrosion and damage of
components, malfunction and fire.
• Do not install the outdoor unit in the locations listed below.
•
Locations where discharged hot air or operating sound of the outdoor unit can
bother neighborhood.
•
Locations where outlet air of the outdoor unit blows directly to an animal or
plants. The outlet air can affect adversely to the plant etc.
•
Locations where vibration can be amplified and transmitted due to insufficient
strength of structure.
•
Locations where vibration and operation sound generated by the outdoor unit
can affect seriously (on the wall or at the place near bed room).
•
Locations where an equipment affected by high harmonics is placed (TV set or
radio receiver is placed within 5m).
•
Locations where drainage cannot run off safely.
It can affect surrounding environment and cause a claim.
• Do not install the unit near the location where leakage of combustible
gases can occur.
If leaked gases accumulate around the unit, it can cause fire.
• Do not install the unit where corrosive gas (such as sulfurous acid gas etc.)
or combustible gas (such as thinner and petroleum gases) can accumulate
or collect, or where volatile combustible substances are handled.
Corrosive gas can cause corrosion of heat exchanger, breakage of plastic parts
and etc. And combustible gas can cause fire.
• Do not install nor use the system close to the equipment that generates
electromagnetic fields or high frequency harmonics.
Equipment such as inverters, standby generators, medical high frequency
equipments and telecommunication equipments can affect the system, and cause
malfunctions and breakdowns. The system can also affect medical equipment and
telecommunication equipment, and obstruct its function or cause jamming.
•
Do not install the outdoor unit in a location where insects and small
animals can inhabit.
Insects and small animals can enter the electric parts and cause damage or fire.
Instruct the user to keep the surroundings clean.
•
Do not use the base flame for outdoor unit which is corroded or damaged
due to long periods of operation.
Using an old and damage base flame can cause the unit falling down and cause
personal injury.
•
Do not use any materials other than a fuse with the correct rating in the
location where fuses are to be used.
Connecting the circuit with copper wire or other metal thread can cause unit
failure and fire.
•
Do not touch any buttons with wet hands.
It can cause electric shocks.
•
Do not touch any refrigerant pipes with your hands when the system is in
operation.
During operation the refrigerant pipes become extremely hot or extremely cold
depending the operating condition, and it can cause burn injury or frost injury.
•
Do not touch the suction or aluminum fin on the outdoor unit.
This may cause injury.
•
Do not put anything on the outdoor unit and operating unit.
This may cause damage the objects or injury due to falling to the object.
•
Do not use the unit for special purposes such as storing foods, cooling
precision instruments and preservation of animals, plants or art.
•
Do not clean up the unit with water.
Over 500mm
Heavy
Wind
direction
Wind
direction
Model 40·50·60
R410A REFRIGERANT USED
Intake
Outlet
312.5
24.3
14.8
290
89
510
201
351.6
Wires for connecting indoor
and outdoor units
Exterior tape
Gas piping
Insulation
Liquid piping
Band (procured locally)
Pipe cover (procured locally)
8) Heating and condensation prevention
Take care so that installed pipes may not touch components within a unit.
If touching with an internal component, it will generate abnormal sounds and/or vibrations.
4) On-site piping work
IMPORTANT
How to remove the side cover
Please remove the screw of a side cover and
remove to the front.
A
B
Flared pipe end : A
(mm)
ø6.35
ø12.7
Copper pipe
outer diameter
0
A –04
9.1
16.6
ø6.35
ø12.7
Copper pipe
outer diameter
0
~
0.5
1.0
~
1.5
Copper pipe protrusion for flaring : B
(mm)
In the case of a rigid (clutch) type
With an R410A tool With a conventional tool
CAUTION
Do not apply force beyond proper fastening torque in tightening the flare nut.
Tightening angle (
°
)
Tightening torque (N·m)
ø6.35 (1/4")
ø12.7 (1/2")
Recommended length of a tool handle (mm)
Operation valve size (mm)
5) Air tightness test
Gas side
operation valve
Check joint
Pressurize
Close
Outdoor unit
Indoor unit
<Work flow>
6) Evacuation
Pay attention to the following points in addition to the above for the R410A and compatible machines.
Air tightness test completed
Fill refrigerant
Vacuum gauge check
Vacuuming completed
Vacuuming begins
3) Refrigerant pipe wall thickness and material
NOTE
*Phosphorus deoxidized seamless copper pipe ICS 23.040.15, ICS 77.150.30
ø6.35
0.8
O-type pipe
ø12.7
0.8
O-type pipe
Pipe diameter [mm]
Minimum pipe wall thickness [mm]
Pipe material*
• Select refrigerant pipes of the table shown on the right wall thickness and material as specified
for each pipe size.
Although outdoor and indoor units themselves have been tested for air tightness at the factory, check the connecting pipes after the installation work for air tightness from the operation
valve’s check joint equipped on the outdoor unit side. While conducting a test, keep the operation valve shut all the time.
a) Raise the pressure to 0.5MPa, and then stop. Leave it for five minutes to see if the pressure drops.
b) Then raise the pressure to 1.5MPa, and stop. Leave it for five more minutes to see if the pressure drops.
c) Then raise the pressure to the specified level (4.15MPa), and record the ambient temperature and the pressure.
d) If no pressure drop is observed with an installation pressurized to the specified level and left for about one day, it is acceptable. When the ambient temperature fall 1
°
C, the pressure also
fall approximately 0.01MPa. The pressure, if changed, should be compensated for.
e) If a pressure drop is observed in checking e) and a) – d), a leak exists somewhere. Find a leak by applying bubble test liquid to welded parts and flare joints and repair it. After repair,
conduct an air tightness test again.
In conducting an air tightness test, use nitrogen gas and pressurize the system with nitrogen gas from the gas side. Do not use a medium other than nitrogen gas under any circumstances.
• Carry out the on site piping work with the operation valve fully closed.
• Give sufficient protection to a pipe end (compressed and blazed, or with an
adhesive tape) so that water or foreign matters may not enter the piping.
• Bend a pipe to a radius as large as practical (R100~R150). Do not bend a pipe
repeatedly to correct its form.
• Flare connection is used between the unit and refrigerant pipe. Flare a pipe after
engaging a flare nut onto it. Flare dimensions for R410A are different from
those for conventional R407C. Although we recommend the use of flaring tools
designed specifically for R410A, conventional flaring tools can also be used by
adjusting the measurement of protrusion B with a protrusion control gauge.
• The pipe should be anchored every 1.5m or less to isolate the vibration.
• Tighten a flare joint securely with a double spanner.
• To prevent a different oil from entering, assign dedicated tools, etc. to each refrigerant type. Under no circumstances must a
gauge manifold and a charge hose in particular be shared with other refrigerant types (R22, R407C, etc.).
• Use a counterflow prevention adapter to prevent vacuum pump oil from entering the refrigerant system.
• This
unit
contains factory charged refrigerant covering 15m of refrigerant piping and additional refrigerant charge on
the installation site is not required for an installation with up to 15m refrigerant piping.
When refrigerant piping exceeds 15m, additionally charge an amount calculated from the pipe length and the above
table for the portion in excess of 15m.
• If an existing pipe system is used, a required refrigerant charge volume will very depending on the liquid pipe size.
For further information, please see “5. UTILIZATION OF EXISTING PIPING.”
* When an additional charge volume calculation result is negative, it is not necessary to charge refrigerant additionally.
• For an installation measuring 15m or shorter in pipe length, please charge the refrigerant volume charged for
shipment at the factory, when you recharge refrigerant after servicing etc.
Fix both liquid and gas operation valves at the valve main bodies as illustrated on the right, and then fasten them,
applying appropriate fastening torque.
Select pipes having a wall thickness larger than the specified minimum pipe thickness.
14
~
18
49
~
61
45
~
60
30
~
45
150
250
1
2
Run the vacuum pump for at least one hour after the vacuum
gauge shows –0.1MPa or lower. (–76cmHg or lower)
When the system has remaining moisture
inside or a leaky point, the vacuum gauge
indicator will rise.
Check the system for a leaky point and
then draw air to create a vacuum again.
Confirm that the vacuum gauge indicator does not rise even if
the system is left for one hour or more.
(three-way valve)
Charge hose (Designed specifically for R410A)
Compound pressure gauge
Pressure gauge
Gauge manifold
(Designed specifically for R410A)
Handle Hi
Vacuum pump
Vacuum pump adapter
(Anti-reverse flow type)
(Designed specifically for R410A)
Charge hose
(Designed specifically for R410A)
Check joint
-0.1MPa
(-76cmHg)
Handle Lo
Operation valve
Operation valve
(two-way valve)
Operation valve cap
Operation valve cap
Operation valve cap
tightening torque (N·m)
Check joint blind nut
tightening torque (N·m)
ø6.35 (1/4")
ø12.7 (1/2")
20
~
30
25
~
35
10
~
12
Operation valve size
(mm)
Securely tighten the operation valve cap and the check joint blind nut after adjustment.
(1) Dress refrigerant pipes (both gas and liquid pipes) for heat insulation and prevention of dew condensation.
• Improper heat insulation/anti-dew dressing can result in a water leak or dripping causing damage to household effects, etc.
(2) Use a heat insulating material that can withstand 120
°
C or a higher temperature. Poor heat insulating capacity can cause heat insulation problems or cable
deterioration.
• All gas pipes must be securely heat insulated in order to prevent damage from dripping water that comes from the condensation formed on them during a cooling
operation or personal injury from burns because their surface can reach quite a high temperature due to discharged gas flowing inside during a heating operation.
• Wrap indoor units’ flare joints with heat insulating parts (pipe cover) for heat insulation (both gas and liquid pipes).
• Give heat insulation to both gas and liquid side pipes. Bundle a heat insulating material and a pipe tightly together so that no gaps may be left between them and
wrap them together with a connecting cable by a dressing tape.
• Both gas and liquid pipes need to be dressed with 20mm or thicker heat insulation materials above the ceiling where relative humidity exceeds 70%.
(1) Calculate a required refrigerant charge volume from the following table.
Formula to calculate the volume of additional refrigerant required
7) Additional refrigerant charge
Additional charge volume (kg) = { Main length (m) – Factory charged volume 15 (m) } x 0.02 (kg/m)
0.02
1.50
15
Model 40, 50, 60
Put down the refrigerant volume calculated from the pipe length onto the caution label attached
on the service panel.
• Since R410A refrigerant must be charged in the liquid phase, you should charge it, keeping the container
cylinder upside down or using a refrigerant cylinder equipped with a siphon tube.
• Charge refrigerant always from the liquid side service port with the operation valve shut. When you find it
difficult to charge a required amount, fully open the outdoor unit valves on both liquid and gas sides and
charge refrigerant from the gas (suction) side service port, while running the unit in the cooling mode. In
doing so, care must be taken so that refrigerant may be discharged from the cylinder in the liquid phase
all the time. When the cylinder valve is throttled down or a dedicated conversion tool to change liquid
phase refrigerant into mist is used to protect the compressor, however, adjust charge conditions so that
refrigerant will gasify upon entering the unit.
• In charging refrigerant, always charge a calculated volume by using a scale to measure the charge
volume.
• When refrigerant is charged with the unit being run, complete a charge operation within 30minutes.
Running the unit with an insufficient quantity of refrigerant for a long time can cause a compressor failure.
(2) Charging refrigerant
NOTE
Additional charge volume (kg)
per meter of refrigerant piping
(liquid pipe ø6.35)
Refrigerant volume charged
for shipment at the factory
(kg)
Installation’s pipe length (m)
covered without additional
refrigerant charge
The screw of the
side cover is
tightened securely.
Side cover
Do not hold the valve cap area with a spanner.
Use a torque wrench. If a torque wrench is
not available, fasten the flare nut manually
first and then tighten it further, using the
left table as a guide.
RWC012A038
4. ELECTRICAL WIRING WORK
For details of electrical cabling, refer to the indoor unit installation manual.
H
05
R
N
R
4or5
G
1.5
Harmonized cable type
300/500 volts
Natural-and/or synth. rubber wire insulation
Polychloroprene rubber conductors insulation
Stranded core
Number of conductors
One conductor of the cable is the earth conductor
(yellow/green)
Section of copper wire (mm
2
)
H05RNR4G1.5 (Example) or 245IEC57
Electrical installation work must be performed by an electrical installation service provider qualified by a power provider of the country.
Electrical installation work must be executed according to the technical standards and other regulations applicable to electrical installations in the country.
• Do not use any supply cord lighter than one specified in parentheses for each type below.
• braided cord (code designation 60245 IEC 51)
• ordinary tough rubber sheathed cord (code designation 60245 IEC 53)
• flat twin tinsel cord (code designation 60227 IEC 41)
Use polychloroprene sheathed flexible cord (code designation 60245 IEC57) for supply
cords of parts of appliances for outdoor use.
• Ground the unit. Do not connect the grounding wire to a gas pipe, water pipe, lightning rod
or telephone grounding wire.
If improperly grounded, an electric shock or malfunction may result.
• A grounding wire must be connected before connecting the power cable. Provide a
grounding wire longer than the power cable.
• The installation of an impulse withstanding type earth leakage breaker is necessary. A
failure to install an earth leakage breaker can result in an accident such as an electric shock
or a fire.
• Do not turn on the power until the electrical work is completed.
• Do not use a condensive capacitor for power factor improvement under any circumstances.
(It dose not improve power factor, while it can cause an abnormal overheat accident)
• For power supply cables, use conduits.
• Do not lay electronic control cables (remote control and signaling wires)
and other cables together outside the unit. Laying them together can
result in the malfunctioning or a failure of the unit due to electric noises.
• Fasten cables so that may not touch the piping, etc.
• When cables are connected, make sure that all electrical components
within the electrical component box are free of loose connector coupling
or terminal connection and then attach the cover securely. (Improper
cover attachment can result in malfunctioning or a failure of the unit, if
water penetrates into the box.)
• Never use a shield cable.
• SRC-ZMXA-S complies with the DRED (Demand Response Enabling
Devices) standard AS/NZS4755.3.1 and supports demand response
modes 1, 2, and 3 (DRM1, 2, and 3). Since the air conditioner limits the
electric power or energy by receiving the DRED input signal, the sense
of cooling operation or heating operation may deteriorate over time. The
outdoor unit of this air conditioner is equipped with a terminal block for
DRED input and supports ELV (Extra-Low Voltage) complying with
AS/NZS60335.1.
CAUTION
CAUTION
Interconnecting and
grounding wires
(minimum)
Switch breaker
Over current protector
rated capacity
Power source
(minimum)
15A, 30mA, 0.1sec or less
30A
16A
2.0mm
2
1.5mm
2
X 4
Earth leakage breaker
Phase
Single-phase
• The specifications shown in the above table are for units without heaters. For units with heaters, refer to the installation
instructions or the construction instructions of the indoor unit.
• Switchgear or Circuit breaker capacity which is calculated from MAX. over current should be chosen along the
regulations in each country.
• The cable specifications are based on the assumption that a metal or plastic conduit is used with no more than three
cables contained in a conduit and a voltage drop is 2%. For an installation falling outside of these conditions, please
follow the internal cabling regulations. Adapt it to the regulation in effect in each country.
Switchgear or Circuit Breaker
Power cable, indoor-outdoor connecting wires
• Always perform grounding system installation work with the power cord unplugged.
• Connect a pair bearing a common terminal number with an indoor-outdoor connecting wire.
• In cabling, fasten cables securely with cable clamps so that no external force may work on terminal connections.
• Grounding terminals are provided in the control box.
N L
1 2/N 3
1 2/N 3
Safety
breaker
16A
Earth
leakage
circuit
breaker
Earth
Earth
Power supply
Indoor unit
Outdoor unit
Model SRC-ZMX-S
N L
D1 D2 D3 C
D1 D2 D3
Safety
breaker
16A
Earth
leakage
circuit
breaker
Power supply
DRED*
Outdoor unit
1 2/N 3
1 2/N 3
Indoor unit
Model SRC-ZMXA-S
C
Connecting cable between outdoor unit and DRED shall be double insulation layer, polychloroprene sheathed (>50V)
with size 4 x (0.5mm
2
to 2.0mm
2
) cable or flexible cord, where the maximum allowable length is 30m.
When wire length exceeds
30m, use 2.5mm
2
wires.
When wire length exceeds
30m, use 2.5mm
2
wires.
*Demand
response
enabling
devices
Power cable, indoor - outdoor connecting wire circuit diagram
Model SRC-ZMX-S
Model SRC-ZMXA-S
<Table of pipe size restrictions>
◎
: Standard pipe size
○
: Usable
△
: Restricted to shorter pipe length limits
Additional charge volume (kg) =
{Main pipe length (m) - Length covered without additional
charge shown in the table (m)} X Additional charge volume
per meter of pipe shown in the table (kg/m)
Liquid pipe
Gas pipe
Usability
Maximum one-way pipe length
Length covered without additional charge
Usability
Maximum one-way pipe length
Length covered without additional charge
Usability
Maximum one-way pipe length
Length covered without additional charge
Pipe size
40
50
60
Additional charge volume per meter of pipe
0.02kg/m
ø6.35
ø12.7
◎
30
15
◎
30
15
◎
30
15
0.06kg/m
ø9.52
ø12.7
△
10
5
△
10
15
△
10
5
Formula to calculate additional charge volume
NO
Are the existing units our products?
NO
NO
NO
NO
NO
NO
Is the existing pipe system to reuse free of corrosion, flaws or dents?
Repair the damaged parts.
Remove those branches.
Repair the damaged parts.
Check the pipe system for air tightness on the site.
Repair the damaged parts.
No loose pipe supports
NO
YES
START
The existing pipe system is reusable.
The existing pipe system is not reusable.
Install a new pipe system.
YES
YES
YES
YES
YES
Are an outdoor unit and an indoor unit connected to the
existing pipe system to reuse?
Is the unit to install in the existing pipe system a
twin-triple-double-twin model?
Is the existing pipe system to reuse free of gas leaks?
(Check whether refrigerant charge was required frequently for
the system before)
Are heat insulation materials of the existing pipe system to
reuse free of peel-offs or deterioration?
(Heat insulation is necessary for both gas and liquid pipes)
Change the branching pipe to a specified type.
Does the existing pipe system to reuse satisfy all of the following?
(1) The pipe length is 30m or less.
(2) The pipe size conforms to the table of pipe size restrictions.
(3) The elevation difference between the indoor and outdoor units
conforms to the following restrictions.
Where the outdoor unit is above: 15m or less
Where the outdoor unit is below: 15m or less
Which of the following refrigeration oils
does the existing unit use?
Suniso, MS, Barrel Freeze, HAB, Freol,
ether oil, ester oil
Please make an
inquiry for
reusability.
Change
Change is impossible.
Can Use
Can not Use
Repair is impossible.
Air tightness is impossible.
Remove is impossible
Repair is impossible.
Repair
Repair
Repair
Some loose pipe supports
Air tightness is OK
Remove
Check whether an existing pipe system is reusable or not by using the following flow chart.
Are not there any loose pipe supports?
Are there any branch pipes with no indoor unit connected?
NO
• Please consult with our distributor in the area,
if you need to recover refrigerant and charge it
again.
• Any combinations of pipe sizes not listed in the
table are not usable.
※
If you obtain a negative figure as a result of calculation, no additional
refrigerant needs to be charged.
Example) When an 60 is installed in a 10m long existing pipe system
(liquid ø9.52, gas ø12.7), the quantity of refrigerant to charge
additionally should be (10m-5m) x 0.06kg/m = 0.3 kg.
<Where the existing unit can be run for a cooling operation.>
Carry out the following steps with the excising unit (in the order of (1), (2), (3) and (4))
(1) Run the unit for 30 minutes for a cooling operation.
(2) Stop the indoor fan and run the unit for 3 minutes for a cooling operation (returning liquid)
(3) Close the liquid side operation valve of the outdoor unit and pump down (refrigerant recovery)
(4) Blow with nitrogen gas.
※
If discolored refrigeration oil or any foreign matters is discharged by
the blow, wash the pipe system or install a new pipe system.
• For the flare nut, do not use the old one, but use the one supplied with the outdoor unit.
Process a flare to the dimensions specified for R410A.
<Where the existing unit cannot be run for a cooling operation.>
Wash the pipe system or install a new pipe system.
• If you choose to wash the pipe system, please contact our distributor in the area.
WARNING
※
Check with the flow chart developed for a case
where an existing pipe system is reused for a
twin-triple-double-twin model published as a
technical data sheet.
Always use an earth leakage circuit breaker designed for inverter circuits to prevent
a faulty operation.
Use cables for interconnection wiring to avoid loosening of the
wires. CENELEC code for cables Required field cables.
In case of faulty wiring connection, the indoor unit stops,
and then the run lamp turns on and the timer lamp blinks.
INSTALLATION TEST CHECK
POINTS
After installation
Power cables and connecting wires are securely fixed to the terminal block.
The power supply voltage is correct as the rating.
The drain hose is fixed securely.
Operation valve is fully open.
No gas leaks from the joints of the operation valve.
The pipe joints for indoor and outdoor pipes have been insulated.
The reverse flow check cap is attached.
The cover of the pipe cover (A) faces downward to prevent rain from entering.
Gaps are properly sealed between the pipe covers (A) (B) and the wall surface / pipes.
The screw of the side cover is tightened securely.
Check the following points again after completion of the
installation, and before turning on the power. Conduct a test run
again and ensure that the unit operates properly.
Explain to the customer how to use the unit and how to take care
of the unit following the instruction manual.
5. UTILIZATION OF EXISTING PIPING
Clearance
3. DRAIN PIPING WORK
• Execute drain piping by using a drain elbow and drain grommets
supplied separately as accessories, where water drained from
the outdoor unit is a problem.
• Water may drip where there is a larger amount of drain water.
Seal around the drain elbow and drain grommets with putty or
adequate caulking material.
• Condensed water may flow out from vicinity of operation valve
or connected pipes.
• Where you are likely to have several days of sub-zero
temperatures in a row, do not use a drain elbow and drain
grommets. (There is a risk of drain water freezing inside and
blocking the drain.)
• When condensed water needs to be led to a drain, etc., install the unit
on a flat base (supplied separately as an optional part) or concrete
blocks.
Then, please secure space for the drain elbow and the drain hose.
Do not put a grommet on
this hole.
This is a supplementary
drain hole to discharge
drain water, when a large
quantity of it is gathered.
Drain elbow
Grommet
Drain hose
(To be procured on the installer’s part)
CAUTION
Cable name plate
• It holds cables in place and protect the terminal connection
from external force.
• This clamp is for the cable in the outside diameter 9
~
15mm.
Please adjust it when not suitable.
• Please be sure to carry out D-type (type III) grounding work.
• It has stuck on the lid of a control box.
Grounding terminal
Power supply terminal block
Cable clamp
Indoor - Outdoor
connecting wire
Power cable
DRED cable
(Demand response
enabling devices)
• Earth wire shall
be Yellow/Green
(Y/G) in color
and longer than
other AC wires
for safety reason.
Summary of Contents for V Multi 100VNX
Page 98: ... 97 13 PAC T 197 Models FDT100VF1 125VF 140VF H H H H H C B A F G D G PJF000Z285 A ...
Page 101: ... 100 13 PAC T 197 Models FDEN60VF 71VF1 C2 C1 A B A B D C1 C2 C1 C2 E G F C PFA003Z817 ...
Page 116: ... 115 13 PAC T 197 b Wireless remote control RCN E1R 60 17 150 Unit mm ...
Page 291: ... 290 13 PAC T 197 261 12 PAC T 173 ー K ...
Page 590: ... 589 13 PAC T 197 3 8 SUPER LINK E BOARD SC ADNA E F ...
Page 591: ... 590 13 PAC T 197 ...