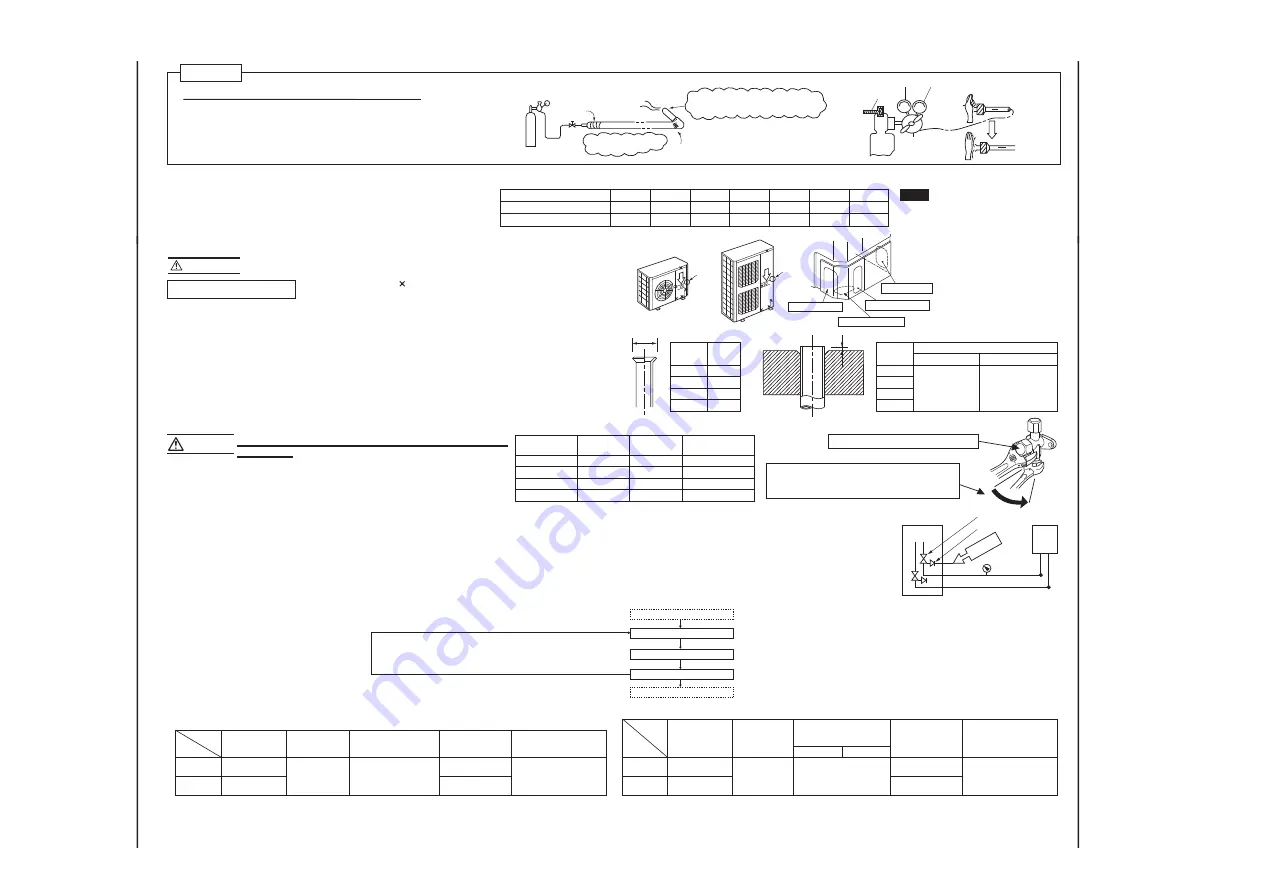
-
296
-
'13 • P
A
C-T
-197
INSTALLATION MANUAL FOR OUTDOOR UNIT
SAFETY PRECAUTIONS
PSB012D955F
2. REFRIGERANT PIPING WORK
1. HAULAGE AND INSTALLATION
(Take particular care in carrying in or moving the unit, and always perform such an operation with two or more persons.)
Inverter driven single split PAC
100VNX
~
140VNX,100VSX
~
140VSX
Designed for R410A refrigerant
[ Accessory ]
Check before installation work
●
Model name and power source
●
Refrigerant piping length
●
Piping, wiring and miscellaneous small parts
●
Indoor unit installation manual
Notabilia as a unit designed for R410A
●
Do not use any refrigerant other than R410A. R410A will rise to pressure about 1.6 times higher than that of a conventional refrigerant.
A cylinder containing R410A has a pink indication mark on the top.
●
A unit designed for R410A has adopted a different size indoor unit operation valve charge port and a different size check joint provided in the unit to prevent the charging of a wrong refrigerant by mistake.
The processed dimension of the flared part of a refrigerant pipe and a flare nut's parallel side measurement have also been altered to raise strength against pressure. Accordingly, you are required to arrange
dedicated R410A tools listed in the table on the right before installing or servicing this unit.
●
Do not use a charge cylinder. The use of a charge cylinder will cause the refrigerant composition to change, which results in performance degradation.
●
In charging refrigerant, always take it out from a cylinder in the liquid phase.
●
All indoor units must be models designed exclusively for R410A. Check connectable indoor unit models in a catalog, etc. (A wrong indoor unit, if connected into the system, will impair proper system operation)
CAUTION
CAUTION
When a unit is hoisted with slings for haulage, take into consideration the offset of its gravity
center position.
If not properly balanced, the unit can be thrown off-balance and fall.
●
The use restrictions appearing in the table above are applicable to the standard pipe size combinations shown in the table below. Where an existing pipe system is
utilized, different one-way pipe length restrictions should apply depending on its pipe size. For more information, see “ 6. UTILIZATION OF EXISTING PIPING.”
●
With the triple pipe connection, the way of use is different when the difference of one-way pipe length after the first branching point is 3m to 10m. For details, refer
to the above table and right figure.
●
When the 50V or 60V model is connected as an indoor unit, always use a
φ
9.52 liquid pipe for the branch (branching pipe – indoor unit) and a different
diameter joint supplied with the branching pipe set for connection with the indoor unit (
φ
6.35 on the liquid pipe side).
If a
φ
6.35 pipe is used for connection with a branching pipe, a refrigerant distribution disorder may occur, causing one of the indoor units to fall short of
the rated capacity.
●
A riser pipe must be a part of the main. A branching pipe set should be installed horizontally at a point as close to an indoor unit as possible.
A branching part must be dressed with a heat-insulation material supplied as an accessory.
●
For the details of installation work required at and near a branching area, see the installation manual supplied with your branching pipe set.
3) Refrigerant pipe wall thickness and material
●
Select refrigerant pipes of the table shown on the right wall thickness and material as
specified for each pipe size.
●
This unit uses R410A. Always use 1/2H pipes having a 1.0mm or thicker wall for
φ
19.05
or larger pipes, because O-type pipes do not meet the pressure resistance requirement.
a
)
b
)
c
)
d
)
e
)
f
)
g
)
h
)
Gauge manifold
Charge hose
Electronic scale for refrigerant charging
Torque wrench
Flare tool
Protrusion control copper pipe gauge
Vacuum pump adapter
Gas leak detector
Dedicated R410A tools
Pipe diameter
[mm]
Minimum pipe wall thickness
[mm]
Pipe material*
6.35
0.8
O-type pipe
9.52
0.8
O-type pipe
12.7
0.8
O-type pipe
15.88
1.0
O-type pipe
22.22
1.0
1/2H-type pipe
25.4
1.0
1/2H-type pipe
28.58
1.0
1/2H-type pipe
NOTE
*Phosphorus deoxidized seamless copper pipe C1220T, JIS
H
3300
1) Delivery
●
Deliver the unit as close as possible to the installation site before removing it from the packaging.
●
When some compelling reason necessitates the unpacking of the unit before it is carried in, use
nylon slings or protective wood pieces so as not to damage the unit by ropes lifting it.
2) Portage
●
The right hand side of the unit as viewed from the front (diffuser side) is heavier. A person
carrying the right hand side must take heed of this fact. A person carrying the left hand side
must hold with his right hand the handle provided on the front panel of the unit and with his
left hand the corner column section.
◎
This installation manual deals with outdoor units and general installation specifications only. For indoor units, refer to page 212.
◎
When install the unit, be sure to check whether the selection of installation place, power supply specifications, usage limitation (piping length, height
differences between indoor and outdoor units, power supply voltage and etc.) and installation spaces
Intake
(
service
space
)
Intake
Outlet
5) Installation space
●
Walls surrounding the unit in the four sides are not acceptable.
●
There must be a 1-meter or larger space in the above.
●
Where a danger of short-circuiting exists, install guide louvers.
●
When more than one unit are installed, provide sufficient intake space consciously so that short-circuiting may not occur.
●
Where piling snow can bury the outdoor unit, provide proper snow guards.
●
A barrier wall placed in front of the exhaust diffuser must not be higher than the unit.
L
3
L
2
L
4
L
1
Example installation
Size
L1
L2
L3
L4
Ⅰ
Open
300
150
5
Ⅱ
Open
5
300
5
Ⅲ
500
Open
150
5
(mm)
1) Restrictions on unit installation and use
2) Determination of pipe size
●
Determine refrigerant pipe size pursuant to the following guidelines based on the indoor unit specifications.
Pad
Wooden pallet
②
Notabilia for installation
Intake
Outlet
Fasten with bolts
(M10-12)
Use a thicker block to
anchor deeper.
Use a long block to extend the width.
190
200
580
20
410
20
①
Anchor bolt fixed position
●
In installing the unit, fix the unit’s legs with bolts specified on the left.
●
The protrusion of an anchor bolt on the front side must be kept within 15 mm.
●
Securely install the unit so that it does not fall over during earthquakes or strong winds, etc.
●
Refer to the left illustrations for information regarding concrete foundations.
●
Install the unit in a level area. (With a gradient of 5 mm or less.)
Improper installation can result in a compressor failure, broken piping within the unit and abnormal noise generation.
6) Installation
Plug the end of the pipe with tape, or other
material, and fill the pipe with nitrogen gas.
Only use nitrogen gas (N
2
)
Taping
<
N
2
>
Nitrogen
Brazing
Station valve
Primary side Secondary side
0.5MPa
Hand
Relief valve
Nitrogen
gas
●
Select pipes having a wall thickness larger
than the specified minimum pipe thickness.
Brazing must be performed under a nitrogen gas flow.
Without nitrogen gas, a large quantity of foreign matters (oxidized film) are
created, causing a critical failure from capillary tube or expansion valve clogging.
About brazing
Edging
1 piece
knock-out hole protection
Descriptions
Outdoor unit connected
Refrigerant piping (branch pipeL)
Flare
Flare
Flare
Flare
Flare
Flare
Gas pipe
Liquid pipe
Gas pipe
Liquid pipe
Gas pipe
Liquid pipe
One-way pipe length after the first
branching point
Dimensional
limitations
Elevation difference between
indoor and outdoor units
One-way pipe length after the
first branching point and second
branching point
One-way pipe length difference
from the first branching point to
the indoor unit
One-way pipe length difference
from the second branching point
to the indoor unit
One-way pipe length between the first
branching point from to the second
branching point
Main pipe length
Elevation difference between indoor units
One-way pipe length difference from the first branching point to the indoor unit
Marks appearting in the drawing
Model for outdoor units
Single type
Twin type
Triple type A
Triple type B
< 3m
≧
3m
L
100VN,125VN,100VS,125VS
≦
50m
≦
100m
≦
5m
≦
30m
≦
27m
≦
10m
≦
3m
≦
10m
≦
10m
≦
30m
≦
15m
≦
0.5m
140VN,140VS
100VN,125VN,100VS,125VS,
100VNX,125VNX,100VSX,125VSX
140VN,140VS,140VNX,140VSX
140VN,140VS,
140VNX,140VSX
When the outdoor unit is positioned higher,
When the outdoor unit is positioned lower,
140VN,140VS,
140VNX,140VSX
Twin type
Triple type
140VNX,140VSX
140VN,140VS,
140VNX,140VSX
100VNX,125VNX,100VSX,125VSX
100VN,125VN,100VS,125VS
≦
50m
≦
100m
140VN,140VS
140VNX,140VSX
100VNX,125VNX,100VSX,125VSX
H
−
−
−
−
−
−
−
−
−
−
−
−
−
L
H
L
+
L1
+
L2
+
L3
−
−
−
−
−
−
−
−
La
L1 (1)
L
L
L
L
+
La
+
L1
+
L2
+
L3
L
+
L1
+
L2
+
L3
L
+
La
+
L1
+
L2
+
L3
|
L2
−
L3
|
L
−
(La
+
L2), L1
−
(La
+
L3)
(1)
La
+
L2
,
La
+
L3
(1)
L1
,
L2
,
L3
h1, h2, h3
H
h1, h2, h3
|
L1
−
L2
|
,
|
L2
−
L3
|
,
|
L3
−
L1
|
−
−
−
−
−
−
−
−
−
L
+
L1
+
L2
L1
,
L2
|
L1
−
L2
|
L
H
h
Indoor unit connected
Capacity of indoor unit
Branching pipe set
Branching pipe set
Refrigerant piping (branch pipe L1,L2)
Indoor unit connected
Capacity of indoor unit
Indoor unit connected
Capacity of indoor unit
Refrigerant piping (branch pipe L1,L2,L3)
Indoor unit connected
Capacity of indoor unit
Branching pipe set
Refrigerant piping (branch pipe La)
Indoor unit connected
Refrigerant piping (branch pipe L2,L3)
In the case of a single type
In the case of a twin type
In the case of a triple type A
In the case of a triple type B
DIS-WA1
DIS-WA1
DIS-WA1
DIS-TA1
DIS-WA1
DIS-WA1
φ
15.88
φ
9.52
φ
9.52
φ
9.52
φ
15.88
φ
15.88
φ
9.52
φ
12.7
φ
6.35
φ
12.7
Model 50V
×
2
Model 71V
×
2
Model 50Vx3
Model 50V
×
3
φ
15.88
φ
9.52
φ
9.52
φ
9.52
φ
15.88
φ
15.88
φ
9.52
φ
15.88
φ
9.52
φ
15.88
φ
9.52
Refrigerant piping (branch pipe L1)
φ
12.7
φ
9.52
φ
15.88
φ
9.52
φ
9.52
φ
15.88
φ
9.52
φ
15.88
φ
15.88
φ
9.52
φ
12.7
φ
6.35
φ
12.7
φ
9.52
φ
12.7
φ
6.35
φ
12.7
φ
9.52
φ
12.7
φ
6.35
φ
12.7
Model 60V
×
2
Model 100V
Model 125V
Model 140V
Note (1) Install the indoor units so that L + L1 becomes the longest one-way pipe.
Keep the pipe length difference between L1 and (La + L2) or (La + L3) within 10m.
< Single type >
< Triple type >
< Triple type >
< Twin type >
Indoor unit
(The unit of which elevation difference from the outdoor unit is the largest.)
Indoor unit
(The unit of which elevation difference from the outdoor unit is the largest.)
L1
L2
L (riser)
Outdoor unit
Indoor unit
h
L
H
H
H
H
Outdoor unit
Indoor unit
L1
L2
L3
L (riser)
Outdoor unit
Indoor unit
Indoor unit
h3
h3
h1
h2
Type A
Type B
L (riser)
Outdoor unit
Indoor unit
Indoor unit
Indoor unit
L1
L2
L3
La
h1
h2
●
Check the following points in light of the indoor unit specifications and the installation site.
●
Observe the following restrictions on unit installation and use. Improper installation can result in a compressor failure or performance degradation.
7) To run the unit for a cooling operation, when the outdoor temperature
is –5°C or lower.
●
When the outdoor air temperature is -5°C or lower, provide a snow hood to the outdoor unit on site.
So that strong wind will not blow against the outdoor heat exchanger directly. Regarding outline of a snow hood,
refer to our technical manual.
●
We recommend you to read this “SAFETY PRECAUTIONS” carefully before the installation work in order to gain full advantage of the functions of the unit and to
avoid malfunction due to mishandling.
●
The precautions described below are divided into and . The matters with possibilities leading to serious consequences such as
death or serious personal injury due to erroneous handling are listed in the and the matters with possibilities leading to personal injury or
damage of the unit due to erroneous handling including probability leading to serious consequences in some cases are listed in .
These are
very important precautions for safety. Be sure to observe all of them without fail.
●
The meaning of "Marks" used here are as shown below.
●
For 3 phase power source outdoor unit,EN61000-3-2 is not applicable if consent by the utility company or nortification to the utility company is given before usage.
●
3phase power source unit, both indoor and outdoor, is suitable for installation in a commercial and light industrial environment. If installed as a house-hold
appliance it could cause electromagnetic interference.
●
5 and 6 HP units of single phase power source are equipment complying with IEC 61000-3-12.
●
Be sure to confirm no anomaly on the equipment by commissioning after completed installation and explain the operating methods as well as the maintenance
methods of this equipment to the user according to the owner's manual.
●
Keep the installation manual together with owner's manual at a place where any user can read at any time. Moreover if necessary, ask to hand them to a new user
Never do it under any circumstance.
Always do it according to the instruction
WARNING
WARNING
CAUTION
CAUTION
CAUTION
3) Selection of installation location for the outdoor unit
Be sure to select a suitable installation place in consideration of following conditions.
〇
A place where it is horizontal, stable and can endure the unit weight and will not allow vibration transmittance of the unit.
〇
A place where it can be free from possibility of bothering neighbors due to noise or exhaust air from the unit
〇
A place where the unit is not exposed to oil splashes.
〇
A place where it can be free from danger of flammable gas leakage.
〇
A place where drain water can be disposed without any trouble.
〇
A place where the unit will not be affected by heat radiation from other heat source.
〇
A place where snow will not accumulate.
〇
A place where the unit can be kept away 5m or more from TV set and/or radio receiver in order to avoid any radio or TV interference.
〇
A place where good air circulation can be secured, and enough service space can be secured for maintenance and service of the unit safely.
〇
A place where the unit will not be affected by electromagnetic waves and/or high-harmonic waves generated by other equipment.
〇
A place where chemical substances like sulfuric gas, chloric gas, acid and alkali (including ammonia), which can harm the
unit, will not be generated and not remain.
〇
A place where strong wind will not blow against the outlet air blow of the unit.
1.Install the outlet air blow side of the
unit to face a wall of building, or
provide a fence or a windbreak screen.
3.The unit should be installed on
the stable and level foundation.
If the foundation is not level,
tie down the unit with wires.
Over 500 mm
Wind direction
2.Install the outlet air blow side of
the unit in a position perpendicular
to the direction of wind.
Wind direction
4) Caution about selection of installation location
(1) If the unit is installed in the area where the snow will accumulate, following measures are required.
The bottom plate of unit and intake, outlet may be blocked by snow.
1.Install the unit on the base so
that the bottom is higher than
snow cover surface.
2.Provide a snow hood to
the outdoor unit on site.
3.Install the unit under eaves
or providen the roof on site.
Since drain water generated by defrost control may freeze, following measures are required.
●
Don’t execute drain piping work by using a drain elbow and drain grommets (optional parts). [Refer to Drain piping work.]
●
Recommend setting Defrost Control (SW3-1) and Snow Guard Fan Control (SW3-2). [Refer to Setting SW3-1, SW3-2.]
(2) If the unit can be affected by strong wind, following measures are required.
Strong wind can cause damage of fan (fan motor), or can cause performance degradation, or can trigger anomalous
stop of the unit due to rising of high pressure.
Regarding outline of a snow
hood, refer to our technical
manual.
One-way pipe length of
refrigerant piping
Model 100V
Model 125V
Model 140V
●
Installation must be carried out by the qualified installer.
If you install the system by yourself, it may cause serious trouble such as water leaks, electric shocks, fire and personal injury, as a result of a system
malfunction.
●
Install the system in full accordance with the instruction manual.
Incorrect installation may cause bursts, personal injury, water leaks, electric shocks and fire.
●
Use the original accessories and the specified components for installation.
If parts other than those prescribed by us are used, It may cause fall of the unit, water leaks, electric shocks, fire, refrigerant leak, substandard
performance, control failure and personal injury.
●
When installing in small rooms, take prevention measures not to exceed the density limit of refrigerant in the event of leakage
accordance with ISO5149.
Consult the expert about prevention measures. If the density of refrigerant exceeds the limit in the event of leakage, lack of oxygen can occur, which
can cause serious accidents.
●
Ventilate the working area well in the event of refrigerant leakage during installation.
If the refrigerant comes into contact with naked flames, poisonous gas is produced.
●
After completed installation, check that no refrigerant leaks from the system.
If refrigerant leaks into the room and comes into contact with an oven or other hot surface, poisonous gas is produced.
●
Hang up the unit at the specified points with ropes which can support the weight in lifting for portage. And to avoid jolting out of alignment,
be sure to hang up the unit at 4-point support.
An improper manner of portage such as 3-point support can cause death or serious personal injury due to falling of the unit
●
Install the unit in a location with good support.
Unsuitable installation locations can cause the unit to fall and cause material damage and personal injury.
●
Ensure the unit is stable when installed, so that it can withstand earthquakes and strong winds.
Unsuitable installation locations can cause the unit to fall and cause material damage and personal injury.
●
The electrical installation must be carried out by the qualified electrician in accordance with “the norm for electrical work” and “national
wiring regulation”, and the system must be connected to the dedicated circuit.
Power supply with insufficient capacity and incorrect function done by improper work can cause electric shocks and fire,
●
Be sure to shut off the power before starting electrical work.
Failure to shut off the power can cause electric shocks, unit failure or incorrect function of equipment.
●
Be sure to use the cables conformed to safety standard and cable ampacity for power distribution work.
Unconformable cables can cause electric leak, anomalous heat production or fire.
●
Use the prescribed cables for electrical connection, tighten the cables securely in terminal block and relieve the cables correctly to prevent
overloading the terminal blocks.
Loose connections or cable mountings can cause anomalous heat production or fire.
●
Arrange the wiring in the control box so that it cannot be pushed up further into the box. Install the service panel correctly.
Incorrect installation may result in overheating and fire.
●
Do not perform brazing work in the airtight room
It can cause lack of oxygen.
●
Use the prescribed pipes, flare nuts and tools for R410A.
Using existing parts (for R22 or R407C) can cause the unit failure and serious accidents due to burst of the refrigerant circuit.
●
Tighten the flare nut by using double spanners and torque wrench according to prescribed method. Be sure not to
tighten the flare nut too much.
Loose flare connection or damage on the flare part by tightening with excess torque can cause burst or refrigerant leaks which
may result in lack of oxygen.
●
Do not open the service valves for liquid line and gas line until completed refrigerant piping work, air tightness test
and evacuation.
If the compressor is operated in state of opening service valves before completed connection of refrigerant piping work, you
may incur frost bite or injury from an abrupt refrigerant outflow and air can be sucked into refrigerant circuit, which can cause
burst or personal injury due to anomalously high pressure in the refrigerant
●
Only use prescribed optional parts. The installation must be carried out by the qualified installer.
If you install the system by yourself, it can cause serious trouble such as water leaks, electric shocks, fire.
●
Do not perform any change of protective device itself or its setup condition
The forced operation by short-circuiting protective device of pressure switch and temperature controller or the use of non
specified component can cause fire or burst.
●
Be sure to switch off the power supply in the event of installation, inspection or servicing.
If the power supply is not shut off, there is a risk of electric shocks, unit failure or personal injury due to the unexpected start of fan.
●
Consult the dealer or an expert regarding removal of the unit.
Incorrect installation can cause water leaks, electric shocks or fire.
●
Stop the compressor before closing valve and disconnecting refrigerant pipes in case of pump down operation.
If disconnecting refrigerant pipes in state of opening service valves before compressor stopping, you may incur frost bite or
injury from an abrupt refrigerant outflow and air can be sucked, which can cause burst or personal injury due to anomalously
high pressure in the refrigerant circuit
●
Ensure that no air enters in the refrigerant circuit when the unit is installed and removed.
If air enters in the refrigerant circuit, the pressure in the refrigerant circuit becomes too high, which can cause burst and
personal injury.
●
Do not run the unit with removed panels or protections
Touching rotating equipments, hot surfaces or high voltage parts can cause personal injury due to entrapment, burn or electric
shocks.
●
Be sure to fix up the service panels.
Incorrect fixing can cause electric shocks or fire due to intrusion of dust or water.
●
Do not perform any repairs or modifications by yourself. Consult the dealer if the unit requires repair.
If you repair or modify the unit, it can cause water leaks, electric shocks or fire.
WARNING
●
Carry out the electrical work for ground lead with care
Do not connect the ground lead to the gas line, water line, lightning conductor or telephone line's ground lead. Incorrect grounding can cause unit faults such as
electric shocks due to short-circuiting. Never connect the grounding wire to a gas pipe because if gas leaks,it could cause explosion or ignition.
●
Use the circuit breaker for all pole with correct capacity.
Using the incorrect circuit breaker, it can cause the unit malfunction and fire.
●
Install isolator or disconnect switch on the power supply wiring in accordance with the local codes and regulations.
The isolator should be locked in accordanced with EN60204-1
.
●
Take care when carrying the unit by hand.
If the unit weights more than 20kg, it must be carried by two or more persons. Do not carry by the plastic straps, always use the carry handle when carrying the
unit by hand. Use gloves to minimize the risk of cuts by the aluminum fins.
●
Dispose of any packing materials correctly.
Any remaining packing materials can cause personal injury as it contains nails and wood. And to avoid danger of suffocation, be sure to keep the plastic
wrapper away from children and to dispose after tear it up.
●
Pay attention not to damage the drain pan by weld spatter when welding work is done near the indoor unit.
If weld spatter entered into the indoor unit during welding work, it can cause pin-hole in drain pan and result in water leakage. To prevent such damage, keep the indoor unit in its packing or cover it.
●
Be sure to insulate the refrigerant pipes so as not to condense the ambient air moisture on them.
Insufficient insulation can cause condensation, which can lead to moisture damage on the ceiling, floor, furniture and any other valuables.
●
Be sure to perform air tightness test by pressurizing with nitrogen gas after completed refrigerant piping work.
If the density of refrigerant exceeds the limit in the event of refrigerant leakage in the small room, lack of oxygen can occur, which can cause serious accidents.
●
Perform installation work properly according to this installation manual.
Improper installation can cause abnormal vibrations or increased noise generation.
●
Earth leakage breaker must be installed
If the earth leakage breaker is not installed, it can cause fire or electric shocks.
●
Do not use any materials other than a fuse with the correct rating in the location where fuses are to be used.
Connecting the circuit with copper wire or other metal thread can cause unit failure and fire.
●
Do not install the unit near the location where leakage of combustible gases can occur.
If leaked gases accumulate around the unit, it can cause fire.
●
Do not install the unit where corrosive gas (such as sulfurous acid gas etc.) or combustible gas (such as thinner and petroleum gases) can
accumulate or collect, or where volatile combustible substances are handled.
Corrosive gas can cause corrosion of heat exchanger, breakage of plastic parts and etc. And combustible gas can cause fire.
●
Secure a space for installation, inspection and maintenance specified in the manual.
Insufficient space can result in accident such as personal injury due to falling from the installation place..
●
When the outdoor unit is installed on a roof or a high place, provide permanent ladders and handrails along the access route and fences and handrails around the outdoor unit.
If safety facilities are not provided, it can cause personal injury due to falling from the installation place.
●
Do not install nor use the system close to the equipment that generates electromagnetic fields or high frequency harmonics
Equipment such as inverters, standby generators, medical high frequency equipments and telecommunication equipments can affect the system, and cause
malfunctions and breakdowns. The system can also affect medical equipment and telecommunication equipment, and obstruct its function or cause jamming.
●
Do not install the outdoor unit in a location where insects and small animals can inhabit.
Insects and small animals can enter the electric parts and cause damage or fire. Instruct the user to keep the surroundings clean.
●
Do not use the base flame for outdoor unit which is corroded or damaged due to long periods of operation.
Using an old and damage base flame can cause the unit falling down and cause personal injury.
●
Do not install the unit in the locations listed below
・
Locations where carbon fiber, metal powder or any powder is floating.
・
Locations where any substances that can affect the unit such as sulphide gas, chloride gas, acid and alkaline can occur.
・
Vehicles and ships
・
Locations where cosmetic or special sprays are often used.
・
Locations with direct exposure of oil mist and steam such as kitchen and machine plant.
・
Locations where any machines which generate high frequency harmonics are used.
・
Locations with salty atmospheres such as coastlines
・
Locations with heavy snow (If installed, be sure to provide base flame and snow hood mentioned in the manual)
・
Locations where the unit is exposed to chimney smoke
・
Locations at high altitude (more than 1000m high)
・
Locations with ammonic atmospheres
・
Locations where heat radiation from other heat source can affect the unit
・
Locations without good air circulation.
・
Locations with any obstacles which can prevent inlet and outlet air of the unit
・
Locations where short circuit of air can occur (in case of multiple units installation)
・
Locations where strong air blows against the air outlet of outdoor unit
It can cause remarkable decrease in performance, corrosion and damage of components, malfunction and fire.
●
Do not install the outdoor unit in the locations listed below.
・
Locations where discharged hot air or operating sound of the outdoor unit can bother neighborhood.
・
Locations where outlet air of the outdoor unit blows directly to an animal or plants. The outlet air can affect adversely to the plant etc.
・
Locations where vibration can be amplified and transmitted due to insufficient strength of structure.
・
Locations where vibration and operation sound generated by the outdoor unit can affect seriously. (on the wall or at the place near bed room)
・
Locations where an equipment affected by high harmonics is placed. (TV set or radio receiver is placed within 5m)
・
Locations where drainage cannot run off safely.
It can affect surrounding environment and cause a claim
●
Do not use the unit for special purposes such as storing foods, cooling precision instruments and preservation of animals, plants or art.
It can cause the damage of the items.
●
Do not touch any buttons with wet hands
It can cause electric shocks
●
Do not touch any refrigerant pipes with your hands when the system is in operation.
During operation the refrigerant pipes become extremely hot or extremely cold depending the operating condition, and it can cause burn injury or frost injury.
●
Do not clean up the unit with water
It can cause electric shocks
●
Do not operate the outdoor unit with any article placed on it.
You may incur property damage or personal injure from a fall of the article.
●
Do not step onto the outdoor unit.
You may incur injury from a drop or fall.
CAUTION
Heavy
<
Work flow
>
6) Evacuation
7) Additional refrigerant charge
(1) Calculate a required refrigerant charge volume from the following table.
Pay attention to the following points in addition to the above for
the R410A and compatible machines.
○
To prevent a different oil from entering, assign dedicated tools, etc. to each
refrigerant type. Under no circumstances must a gauge manifold and a charge
hose in particular be shared with other refrigerant types (R22, R407C, etc.).
○
Use a counterflow prevention adapter to prevent vacuum pump oil from
entering the refrigerant system.
Additional charge volume (kg) = { Main pipe length (m) – Length covered without additional charge 30 (m) } x 0.06 (kg/m) + Total length of branch pipes (m) x 0.06 (kg/m)
<Single type>
Formula to calculate the volume of additional refrigerant required
<Twin, triple, W-twin type>
8) Heating and condensation prevention
(1) Dress refrigerant pipes (both gas and liquid pipes) for heat insulation and prevention of dew condensation.
(2) Use a heat insulating material that can withstand 120
℃
or a higher temperature. Poor heat insulating capacity can cause heat insulation problems or cable deterioration.
- Improper heat insulation/anti-dew dressing can result in a water leak or dripping causing damage to household effects, etc.
- All gas pipes must be securely heat insulated in order to prevent damage from dripping water that comes from the condensation formed on them during a cooling operation or personal injury from
burns because their surface can reach quite a high temperature due to discharged gas flowing inside during a heating operation.
- Wrap indoor units’ flare joints with heat insulating parts (pipe cover) for heat insulation (both gas and liquid pipes).
- Give heat insulation to both gas and liquid side pipes. Bundle a heat insulating material and a pipe tightly together so that no gaps may be left between them and wrap them together with a
connecting cable by a dressing tape.
- Although it is verified in a test that this air conditioning unit shows satisfactory performance under JIS condensation test conditions,
both gas and liquid pipes need to be dressed with 20 mm
or thicker heat insulation materials above the ceiling where relative humidity exceeds 70%.
Wires for connecting indoor
and outdoor units
Exterior tape
Gas piping
insulation
Liquid piping
Band (accessory)
Pipe cover (accessory)
(2) Charging refrigerant
●
Since R410A refrigerant must be charged in the liquid phase, you should charge it, keeping the container cylinder upside down or using a refrigerant cylinder equipped with a siphon tube.
●
Charge refrigerant always from the liquid side service port with the operation valve shut. When you find it difficult to charge a required amount, fully open the outdoor unit valves on both liquid and gas sides and charge refrigerant from the gas
(suction) side service port, while running the unit in the cooling mode. In doing so, care must be taken so that refrigerant may be discharged from the cylinder in the liquid phase all the time. When the cylinder valve is throttled down or a dedicated
conversion tool to change liquid-phase refrigerant into mist is used to protect the compressor, however, adjust charge conditions so that refrigerant will gasify upon entering the unit.
●
In charging refrigerant, always charge a calculated volume by using a scale to measure the charge volume.
●
When refrigerant is charged with the unit being run, complete a charge operation within 30 minutes. Running the unit with an insufficient quantity of refrigerant for a long time can cause a compressor failure.
4. ELECTRICAL WIRING WORK
For details of electrical cabling, refer to the indoor unit installation manual.
5. TEST RUN
6. UTILIZATION OF EXISTING PIPING
3) Setting SW3-1, SW3-2, on-site
(1) Defrost control switching (SW3-1)
・
When this switch is turned ON, the unit will run in the defrost mode more frequently.
・
Set this switch to ON, when installed in a region where outdoor temperature falls below zero during the season the unit is run for a
heating operation.
(2) Snow guard fan control (SW3-2)
・
When this switch is turned on, the outdoor unit fan will run for 10 seconds in every 10 minutes, when outdoor temperature falls to 3
℃
or
lower and the compressor is not running.
・
When the unit is used in a very snowy country, set this switch to ON.
5) The state of the electronic expansion valve.
The following table illustrates the steady states of the electronic expansion valve.
Valve for a cooling operation
During a cooling operation
When power is turned on
When the unit comes to a normal stop
When the unit comes to an abnormal stop
Valve for a heating operation
During a heating operation During a cooling operation During a heating operation
Complete shut position
Full open position
Full open position
Full open position
Complete shut position
Full open position
Full open position
Complete shut position
Full open position
Full open position
2) Checking the state of the unit in operation
Use check joints provided on the piping before and after the four-way valve installed inside the
outdoor unit for checking discharge pressure and suction pressure.
As indicated in the table shown on the right, pressure detected at each point will vary
depending on whether a cooling or heating operation has been selected.
SWITCHES FOR ON-SITE SETTING
SW5
All set to OFF for shipment
All set to OFF for shipment
SWITCHES FOR ON-SITE SETTING
SW3
Cooling during a test run
Heating during a test run
Normal or After the test operation
●
If an error code other than those listed above is indicated, refer to the wiring diagram of the outdoor unit and the indoor unit.
Error indicated on the
remote control unit
Action
Failure event
Open phase
63H1 actuation or operation with operation valves shut
(occurs mainly during a heating operation)
Low pressure error or operation with operation valves shut
(occurs mainly during a cooling operation)
1. Check whether the operation valves are open.
2. If an error has been canceled when 3 minutes have elapsed
since a compressor stop, you can restart the unit by
effecting Check Reset from the remote control unit.
Airtighteness test completed
Fill refrigerant
Vacuum gauge check
Vacuuming completed
Vacuuming begins
Run the vacuum pump for at least one hour after the vacuum gauge shows
-101kPa or lower. (-755mmHg or lower)
Confirm that the vacuum gauge indicator does not rise even if the system is
left for one hour or more.
When the system has remaining moisture
inside or a leaky point, the vacuum
gauge indicator will rise.
Check the system for a leaky point and
then draw air to create a vacuum again.
NOTE
●
Before conduct a test run, do not fail to make sure that the operation valves are closed.
●
Turn on power 6 hours prior to a test run to energize the crank case heater.
●
In case of the first operation after turning on power, even if the unit does not move for 30 minutes, it is not a breakdown.
●
Always give a 3-minute or longer interval before you start the unit again whenever it is stopped.
●
Removing the service panel will expose high-voltage live parts and high-temperature parts, which are quite dangerous.
Take utmost care not to incur an electric shock or burns. Do not leave the unit with the service panel open.
●
When you operate switches (SW3, SW5) for on-site setting, be careful not to touch a live part.
●
You cannot check discharge pressure from the liquid operation valve charge port.
●
The 4-way valve (20S) is energized during a heating operation.
●
When power supply is cut off to reset the unit, give 3 or more minutes before you turn on power again after power is cut
off. If this procedure is not observed in turning on power again, “Communication error between outdoor and indoor unit”
may occur.
Check item
Check
Check
Item
Turn
The contents of operation
Electric
wiring
Refrigerant
plumbing
Indoor unit
WARNING
WARNING
CAUTION
CAUTION
1) Test run method
(1) A test run can be initiated from an outdoor unit by using SW3-3 and SW3-4 for on-site
setting.
(2) Switching SW3-3 to ON will start the compressor.
(3) The unit will start a cooling operation, when SW3-4 is OFF, or a heating operation, when SW3-4 is ON.
(4)
Do not fail to switch SW3-3 to OFF when a test run is completed.
●
A standard refrigerant charge volume means a refrigerant charge volume for an installation with 0m long refrigerant piping.
●
This unit contains factory charged refrigerant covering 30m of refrigerant piping and additional refrigerant charge on the installation site is not required for an installation with up to 30m refrigerant piping.
When refrigerant piping exceeds 30m, additionally charge an amount calculated from the pipe length and the above table for the portion in excess of 30m.
●
When refrigerant piping is shorter than 3m, reduce refrigerant by 1kg from the factory charged volume and adjust to 2.8kg.
●
If an existing pipe system is used, a required refrigerant charge volume will vary depending on the liquid pipe size. For further information, see “6. UTILIZATION OF EXISTING PIPING.”
*When an additional charge volume calculation result is negative,
it is not necessary to charge refrigerant additionally.
Pipe length for
standard refrigerant
charge volume (m)
0.06
0
Put down the refrigerant volume calculated from the pipe length onto the caution label attached on the back side of the service panel.
3. DRAIN PIPING WORK
○
There are 3 drain holes provided on the bottom plate of an outdoor unit to discharge
condensed water.
○
When condensed water needs to be led to a drain, etc., install the unit on a flat base
(supplied separately as an optional part) or concrete blocks.
○
Connect a drain elbow as shown in the illustration and close the other two drain holes
with grommets.
Drain elbow ( 1 pe.)
Drain grommet
( 2 pes.)
Hard vinyl chloride pipe for general purpose (VP-16)
●
Execute drain piping by using a drain elbow and drain grommets supplied separately as
optional parts, where water drained from the outdoor unit is a problem.
●
Do not turn on the power until the electrical work is completeted .
●
Do not use a condensive capacitor for power factor improvement under any circumstances. (It dose not improve power factor,
while it can cause an abnormal overheat accident)
●
For power supply cables, use conduits.
●
Do not lay electronic control cables (remote control and signaling wires) and other cables together outside the unit. Laying them
together can result in the malfunctioning or a failure of the unit due to electric noises.
●
Fasten cables so that may not touch the piping, etc.
●
When cables are connected, make sure that all electrical components within the electrical component box are free of loose
connector coupling or terminal connection and then attach the cover securely. (Improper cover attachment can result in
malfunctioning or a failure of the unit, if water penetrates into the box.)
●
Always use a three-core cable for an indoor-outdoor connecting cable. Never use a shield cable.
●
Connect a pair bearing a common terminal number with an indoor-outdoor connecting wire.
●
In cabling, fasten cables securely with cable clamps so that no external force may work on terminal connections.
●
Grounding terminals are provided in the control box.
●
Always perform grounding system installation work
with the power cord unplugged.
ON
1 2
3 4
ON
1 2
3 4
SW-3-3
ON
OFF
Cooling
operation
Heating
operation
Discharge pressure
(High pressure)
Suction pressure
(Low pressure)
Suction pressure
(Low pressure)
Discharge pressure
(High pressure)
SW-3-4
OFF
ON
----
Printed circuit board LED(The cycles of 5 seconds)
Red LED
Blinking once
Blinking once
Blinking once
4) Failure diagnosis in a test run
Power cable, indoor-outdoor connecting wires
Check power cables for loose contact or disconnection
E34
E40
E49
Charge port of the
gas operation valve
Check joint of the pipe
Model
100V
〜
140V
M4 Screw
○
Do not connect to the grounding wire from another
unit, but install a dedicated wire up to the grounding
wire from the distribution board.
○
Fasten cables and protect the terminal connection
from external force.
○
It is attached on the back side of the service panel.
○
As like the refrigerant pipe, it can be let out in any of
the following directions: side right, front, rear and
downward.
Power source, signal line and ground terminal block
Grounding terminal
Wiring clamp
Wiring diagram
Outgoing cable direction
Always use an earth leakage circuit
breaker designed for inverter circuits
to prevent a faulty operation.
L1
Outdoor unit
Switchgear or Circuit breaker
N
1 2/N 3
1 2/N 3
Indoor unit
X
Y
X
Y
Remote control
Model 100VN ~ 140VN
100VNX ~ 140VNX
Model 100VS ~ 140VS
100VSX ~ 140VSX
Earth leakage breaker
(Harmonic resistant type)
Electrical installation work must be performed by an electrical installation service provider qualified by a power provider of the country.
Electrical installation work must be executed according to the technical standards and other regulations applicable to electrical
installations in the country.
●
Do not use any supply cord lighter than one specified in parentheses for each type below.
- braided cord (code designation 60245 IEC 51),
- ordinary tough rubber sheathed cord (code designation 60245 IEC 53)
- flat twin tinsel cord (code designation 60227 IEC 41);
Do not use anything lighter than polychloroprene sheathed flexible cord (code designation 60245 IEC57) for supply cords of parts
of appliances for outdoor use.
●
Ground the unit. Do not connect the grounding wire to a gas pipe, water pipe, lightning rod or telephone grounding wire.
If impropery grounded, an electric shock or malfunction may result.
●
A grounding wire must be connected before connecting the power cable. Provide a grounding wire longer than the power cable.
●
The installation of an impulse withstanding type earth leakage breaker is necessary. A failure to install an earth leakage breaker
can result in an acccident such as an electric shock or a fire.
L1 L2 L3
Outdoor unit
Switchgear or Circuit breaker
N
1 2/N 3
1 2/N 3
Indoor unit
X
Y
X
Y
Remote control
Earth leakage breaker
(Harmonic resistant type)
●
When you leave the outdoor unit with power supplied to it,
be sure to close the panel.
●
Always carry out a test run and check the following in order as listed.
If brazed, was it brazed under a nitrogen gas flow?
Were air-tightness test and vacuum extraction surely performed?
Are heat insulation materials installed on both liquid and gas pipes?
Are operation valves surely opened for both liquid and gas systems?
Have you recorded the additional refrigerant charge volume and refrigerant pipe length on the panel’s label?
Is the unit free of cabling errors such as uncompleted connection, an absent or reversed phase?
Are properly rated electrical equipments used for circuit breakers and cables?
Doesn’t cabling cross-connect between units, where more than one unit are installed?
Aren’t indoor-outdoor signal wires connected to remote control wires?
Do indoor-outdoor connecting cables connect between the same terminal numbers?
Are either VCT cabtyre cables or WF flat cables used for indoor-outdoor connecting cables?
Does grounding satisfy the D type grounding (type III grounding) requirements?
Is the unit grounded with a dedicated grounding wire not connected to another unit’s grounding wire?
Are cables free of loose screws at their connection points?
Are cables held down with cable clamps so that no external force works onto terminal connections?
Is indoor unit installation work completed?
Where a face cover should be attached onto an indoor unit, is the face cover attached to the indoor unit?
Open the gas side operation valve fully.
Open the liquid side operation valve fully.
Close the panel.
Where a remote control unit is used for unit setup on the installation site, follow instructions for unit setup on the installation site with a remote control unit.
SW3-3 ON / SW3-4 OFF: the unit will start a cooling operation.
SW3-3 ON / SW3-4 ON: the unit will start a heating operation.
When the unit starts operation, press the wind direction button provided on the remote control unit to check its operation.
Place your hand before the indoor unit’s diffuser to check whether cold (warm) winds come out in a cooling (heating) operation.
Make sure that a red LED is not blinking.
When you complete the test run, do not forget to turn SW3-3 to the OFF position.
Where options are used, check their operation according to the respective instruction manuals.
①
②
③
④
⑤
⑥
⑦
⑧
⑨
⑩
2
4
ー
Test run procedure
Green LED
Blinking continuously
Blinking continuously
Blinking continuously
○
×
VCT cabtyre cable
VVF flat cable
4-core cable
Shield cable
A failure to observe these instructions can result in a compressor breakdown.
Item No.used in the
installation manual
Pipe size
Items to checkbefore a test run
Item
Capacity
Standard refrigerant
charge volume (kg)
Additional charge volume (kg)
per meter of refrigerant piping
(liquid pipe)
Refrigerant volume
charged for shipment
at the factory (kg)
Installation’s pipe length (m)
covered without additional
refrigerant charge
100VN
~
140VN
100VS
~
140VS
100VNX
~
140VNX
100VSX
~
140VSX
2.0
2.7
3.8
4.5
30
0.06
0
100VN
~
140VN
100VS
~
140VS
100VNX
~
140VNX
100VSX
~
140VSX
2.0
2.7
3.8
4.5
30
Pipe length for
standard refrigerant
charge volume (m)
Item
Capacity
Standard refrigerant
charge volume (kg)
Additional charge volume (kg)
per meter of refrigerant piping
(liquid pipe)
Refrigerant volume
charged for shipment
at the factory (kg)
Installation’s pipe length (m)
covered without additional
refrigerant charge
Main pipe
Branch pipe
<Table of pipe size restrictions>
<Pipe system after the branching pipe>
<Where the existing unit can be run for a cooling operation.>
<The model types of existing units of which branching pipes are reusable.>
Formula to calculate additional charge volume
Liquid pipe
φ
9.52
φ
9.52
φ
12.7
φ
12.7
Gas pipe
φ
15.88
φ
19.05
φ
15.88
φ
19.05
Usability
◎
○※1
△
△※1
Maximum one-way pipe length
50
50
25
25
Length covered without additional charge
30
30
15
15
Usability
◎
○※1
△
△※1
Maximum one-way pipe length
50
50
25
25
Length covered without additional charge
30
30
15
15
Usability
◎
○※1
△
△※1
Maximum one-way pipe length
50
50
25
25
Length covered without additional charge
30
30
15
15
100VN
100VS
125VN
125VS
0.06kg/m
0.08kg/m
140VN
140VS
NO
Are the existing units our products?
Check whether an existing pipe system is reusable or not by using the following flow chart.
NO
NO
NO
Is the existing pipe system to reuse free of corrosion, flaws or dents?
Repair the damaged parts.
Remove those branches.
Repair the damaged parts.
Check the pipe system for air tightness on the site.
Repair the damaged parts.
NO
NO
NO
NO
No loose pipe supports
NO
YES
START
The existing pipe system is reusable.
The existing pipe system is not reusable.
Install a new pipe system.
YES
YES
YES
YES
YES
Are an outdoor unit and an indoor unit connected to the
existing pipe system to reuse?
Is the unit to install in the existing pipe system a
twin-triple-double-twin model?
Is the existing pipe system to reuse free of gas leaks?
(Check whether refrigerant charge was required frequently for
the system before)
Are heat insulation materials of the existing pipe system to
reuse free of peel-offs or deterioration?
(Heat insulation is necessary for both gas and liquid pipes)
Are there any branch pipes with no indoor unit connected?
Change the branching pipe to a specified type.
Aren’t there any loose pipe supports?
Does the existing pipe system to reuse satisfy all of the following?
(1) The pipe length is 50m or less.
(2) The pipe size conforms to the table of pipe size restrictions.
(3) The elevation difference between the indoor and outdoor units
conforms to the following restrictions.
Where the outdoor unit is above: 30m or less
Where the outdoor unit is below: 15m or less
Which of the following refrigeration oils
does the existing unit use?
Suniso, MS, Barrel Freeze, HAB, Freol,
ether oil, ester oil
Make an inquiry
for reusability.
※
Check with the flow chart developed for a case where
an existing pipe system is reused for a
twin-triple-double-twin model published as a
technical data sheet.
The branching pipes used with models other than those listed above are not reusable because of their insufficient
pressure resistance. Please use our genuine branching pipes for R410A.
●
* * *
are numbers representing horsepower.
□ □ □
is an alphanumeric letter.
Change
Change is impossible.
Can Use
Can‘t
Use
Repair is impossible.
Air tightness is
impossible.
Remove is
impossible
Repair is impossible.
Repair
Repair
Repair
Some loose pipe supports
Air tightness is OK
Remove
◎:
Standard pipe size
○:
Usable
△:
Restricted to shorter pipe length limits
×:
Not usable
Carry out the following steps with the excising unit
(in the order of (1), (2), (3) and (4))
(1) Run the unit for 30 minutes for a cooling operation.
(2) Stop the indoor fan and run the unit for 3 minutes for a cooling operation (returning liquid)
(3) Close the liquid side operation valve of the outdoor unit and pump down (refrigerant recovery)
(4) Blow with nitrogen gas.
※
If discolored refrigeration oil or any foreign matters is discharged by the blow,
wash the pipe system or install a new pipe system.
●
For the flare nut, do not use the old one, but use the one supplied with the outdoor unit.
Process a flare to the dimensions specified for R410A.
●
Turn on-site setting switch SW5-1
to the ON position. (Where the gas pipe size is
φ
19.05)
<Where the existing unit cannot be run for a cooling operation.>
Wash the pipe system or install a new pipe system.
●
If you choose to wash the pipe system, contact our distributor in the area.
Models later than Type 8.
●
F D C
* * *
8
□ □ □
●
F D C P
* * *
8
□ □ □
Additional charge volume (kg) = {Main pipe length (m) – Length covered without additional charge shown in the table (m)}
×
Additional charge volume per meter of pipe shown in the table (kg/m)
+
Total length of branch pipes (m)
×
Additional charge volume per meter of pipe shown in the table (kg/m)
※
If you obtain a negative figure as a result of calculation, no additional refrigerant needs to be charged.
Example)
When an 140V (single installation) is installed in a 20m long existing pipe system (liquid
φ
12.7, gas
φ
19.05),
the quantity of refrigerant to charge additionally should be (20m-15m) x 0.08kg/m = 0.4 kg.
Model
Power source
Power cable thickness(mm
2
)
MAX. over current (A) Cable length (m) Grounding wire thickness
100VN
~
140VN
100VNX
125VNX,140VNX
100VS
~
140VS
100VSX
~
140VSX
5.5
φ
1.6mm
24
25
26
23
3.5
15
27
φ
1.6mm x 3
φ
1.6mm x 3
3 phase 4 wire
380V 50Hz
Single phase 3 wire
220-240V 50Hz
220V 60Hz
Indoor-outdoor wire thickness
×
number
Model
Power source
Power cable thickness(mm
2
)
MAX. over current (A) Cable length (m) Grounding wire thickness
100VN,100VNX
125VN
140VN
125VNX
140VNX
100VS,100VSX
125VS,125VSX
140VS,140VSX
5.5
8
φ
1.6mm
25
27
28
29
30
16
18
19
24
22
32
31
30
26
23
21
3.5
3 phase 4 wire
380-415V 50Hz
380V 60Hz
Single phase 3 wire
220-240V 50Hz
220V 60Hz
Indoor-outdoor wire thickness
×
number
●
The specifications shown in the above table are for units without heaters. For units with heaters, refer to the installation instructions or the construction
instructions of the indoor unit.
●
Switchgear or Circuit breaker capacity which is calculated from MAX. over current should be chosen along the regulations in each country.
●
The cable specifications are based on the assumption that a metal or plastic conduit is used with no more than three cables contained in a conduit and a
voltage drop is 2%. For an installation falling outside of these conditions, follow the internal cabling regulations. Adapt it to the regulation in effect in each
country.
※
At the connection with the duct type indoor unit.
●
To charge refrigerant again, recover refrigerant from the system first and then charge the volume calculated from the above table (Standard refrigerant charge branch pipes charge volume)
6)
Heed the following on the first operation after turning on the circuit breaker.
This outdoor unit may start in the standby mode (waiting for a compressor startup), which can continue up to 30 minutes, to prevent the oil
level in the compressor from lowering on the first operation after turning on the circuit breaker. If that is the case, do not suspect a unit failure.
PSB012D955F
Pipe size
Liquid pipe
Gas pipe
After 1st branch
After 2nd branch
Additional charging amount of refrigerant per 1m
Twin
Twin
Twin
Triple A
Triple B
Combination type
0.06kg/m
0.06kg/m
φ
9.52
φ
12.7
φ
15.88
φ
19.05
◎
◎
×
◎
×
○
○
◎
○
◎
×
×
○
×
○
φ
9.52
φ
12.7
φ
15.88
ー
ー
ー
ー
◎
ー
ー
ー
ー
○
ー
ー
ー
ー
×
50+50
60+60
71+71
50+50+50
50+50+50
Combination of capacity
Model
100V
125V
140V
Additional charging amount of refrigerant per 1m
Pipe size
Liquid pipe
Gas pipe
Usability
Maximum one-way pipe length
Length covered without additional charge
Usability
Maximum one-way pipe length
Length covered without additional charge
Usability
Maximum one-way pipe length
Length covered without additional charge
φ
12.7
φ
19.05
△※1
50
15
△※1
50
15
△※1
50
15
φ
12.7
φ
15.88
△
50
15
△
50
15
△
50
15
φ
9.52
φ
19.05
○※1
100
30
○※1
100
30
○※1
100
30
φ
9.52
φ
15.88
◎
100
30
◎
100
30
◎
100
30
φ
6.35
φ
15.88
△
20
10
△
20
10
△
20
10
100VNX
100VSX
125VNX
125VSX
0.06kg/m
0.02kg/m
0.08kg/m
140VNX
140VSX
Additional charging amount of refrigerant per 1m
※
1 Because of its insufficient pressure resistance,
turn the dip switch SW5-1
provided on the outdoor unit board to the ON position for
φ
19.05
×
t1.0.
(In the case of a twin-triple-double-twin model, this also applies to the case where
φ
19.05
×
t1.0 is used in a pipe system after the first branching point.)
However, you need not turn the dip switch SW5-1 to the ON position, if 1/2H pipes or pipes having 1.2 or thicker walls are used.
※
2 When the main pipe length exceeds 40m, a significant capacity drop may be experienced due to pressure loss in the liquid pipe system. Use
φ
12.7 for
the liquid main.
※
3 Keep the total pipe length, not one-way pipe length, below the specified maximum pipe length.
※
4 Piping size after branch should be equal or smaller than main pipe size.
※
5 Piping size from first branch to indoor unit should be
φ
9.52 (Liquid) /
φ
12.7 (Gas).
●
When refrigerant piping is shoter than 3m, reduce refrigerant by 1kg from factory charged volume.
●
Any combinations of pipe sizes not listed in the table or marked with
×
in the table are not usable.
※1
φ
19.05
※1
※
4
※
5
※
5
5) Air tightness test
①
Although outdoor and indoor units themselves have been tested for air tightness at the factory, check the connecting pipes after the installation work for air tightness from the operation valve’s check joint equipped on the
outdoor unit side. While conducting a test, keep the operation valve shut all the time.
a) Raise the pressure to 0.5 MPa, and then stop. Leave it for five minutes to see if the pressure drops.
b) Then raise the pressure to 1.5 MPa, and stop. Leave it for five more minutes to see if the pressure drops.
c) Then raise the pressure to the specified level (4.15 MPa), and record the ambient temperature and the pressure.
d) If no pressure drop is observed with an installation pressurized to the specified level and left for about one day, it is acceptable. When the ambient Temperature fall 1
℃
, the pressure also fall approximately 0.01 MPa. The
pressure, if changed, should be compensated for.
e) If a pressure drop is observed in checking e) and a) – d), a leak exists somewhere. Find a leak by applying bubble test liquid to welded parts and flare joints and repair it. After repair, conduct an air-tightness test again.
②
In conducting an air-tightness test, use nitrogen gas and pressurize the system with nitrogen gas from the gas side. Do not use a medium other than nitrogen gas under any circumstances.
Gas side
operation valve
Check joint
Pressurize
Close
Outdoor unit
Indoor unit
How to remove the service panel
Catch
First remove the five screws ( mark) of the service panel and push it down into the direction of
the arrow mark and then remove it by pulling it toward you.
●
Take care so that installed pipes may not touch components within a unit. If touching with an internal
component, it will generate abnormal sounds and/or vibrations.
●
The pipe can be laid in any of the following directions: side right, front, rear and downward.
●
Remove a knock-out plate provided on the pipe penetration to open a minimum necessary area and attach an edging
material supplied as an accessory by cutting it to an appropriate length before laying a pipe.
●
Carry out the on site piping work with the operation valve fully closed.
●
Give sufficient protection to a pipe end (compressed and blazed, or with an adhesive tape) so that water or foreign matters may
not enter the piping.
●
Bend a pipe to a radius as large as practical.(R100
〜
R150) Do not bend a pipe repeatedly to correct its form.
●
Flare connection is used between the unit and refrigerant pipe. Flare a pipe after engaging a flare nut onto it. Flare
dimensions for R410A are different from those for conventional R407C. Although we recommend the use of flaring tools
designed specifically for R410A, conventional flaring tools can also be used by adjusting the measurement of protrusion B
with a protrusion control gauge.
●
The pipe should be anchored every 1.5m or less to isolate the vibration.
4) On-site piping work
IMPORTANT
A
B
Flared pipe end: A (mm)
φ
6.35
φ
9.52
φ
12.7
φ
15.88
Copper
pipe outer
diameter
0
ー
0
.
4
A
9
.
1
13
.
2
16.6
19.7
Copper pipe protrusion for flaring: B (mm)
φ
6.35
φ
9.52
φ
12.7
φ
15.88
Copper
pipe outer
diameter
In the case of a rigid (clutch) type
With an R410A tool With a conventional tool
0
〜
0.5
0.7
〜
1.3
For downward connection
For side right connection
For front connection
For rear connection
CAUTION
Do not apply force beyond proper fastening torque in tightening
the flare nut.
Fix both liquid and gas service valves at the valve main bodies as illustrated
on the right, and then fasten them, applying appropriate fastening torque.
Tightening angle
(
°
)
Tightening torque
(N-m)
φ
6.35 (1/4")
φ
9.52 (3/8")
φ
12.7 (1/2")
φ
15.88 (5/8")
14
〜
18
34
〜
42
49
〜
61
68
〜
82
45
〜
60
30
〜
45
30
〜
45
15
〜
20
150
200
250
300
●
Tighten a flare joint securely with a double spanner.
Use a torque wrench. If a torque wrench is not available,
fasten the flare nut manually first and then tighten it
further, using the left table as a guide.
Recommended length
of a tool handle (mm)
Operation valve size
(mm)
Do not hold the valve cap area with a spanner.
Catch
Wiring guide
Summary of Contents for V Multi 100VNX
Page 98: ... 97 13 PAC T 197 Models FDT100VF1 125VF 140VF H H H H H C B A F G D G PJF000Z285 A ...
Page 101: ... 100 13 PAC T 197 Models FDEN60VF 71VF1 C2 C1 A B A B D C1 C2 C1 C2 E G F C PFA003Z817 ...
Page 116: ... 115 13 PAC T 197 b Wireless remote control RCN E1R 60 17 150 Unit mm ...
Page 291: ... 290 13 PAC T 197 261 12 PAC T 173 ー K ...
Page 590: ... 589 13 PAC T 197 3 8 SUPER LINK E BOARD SC ADNA E F ...
Page 591: ... 590 13 PAC T 197 ...