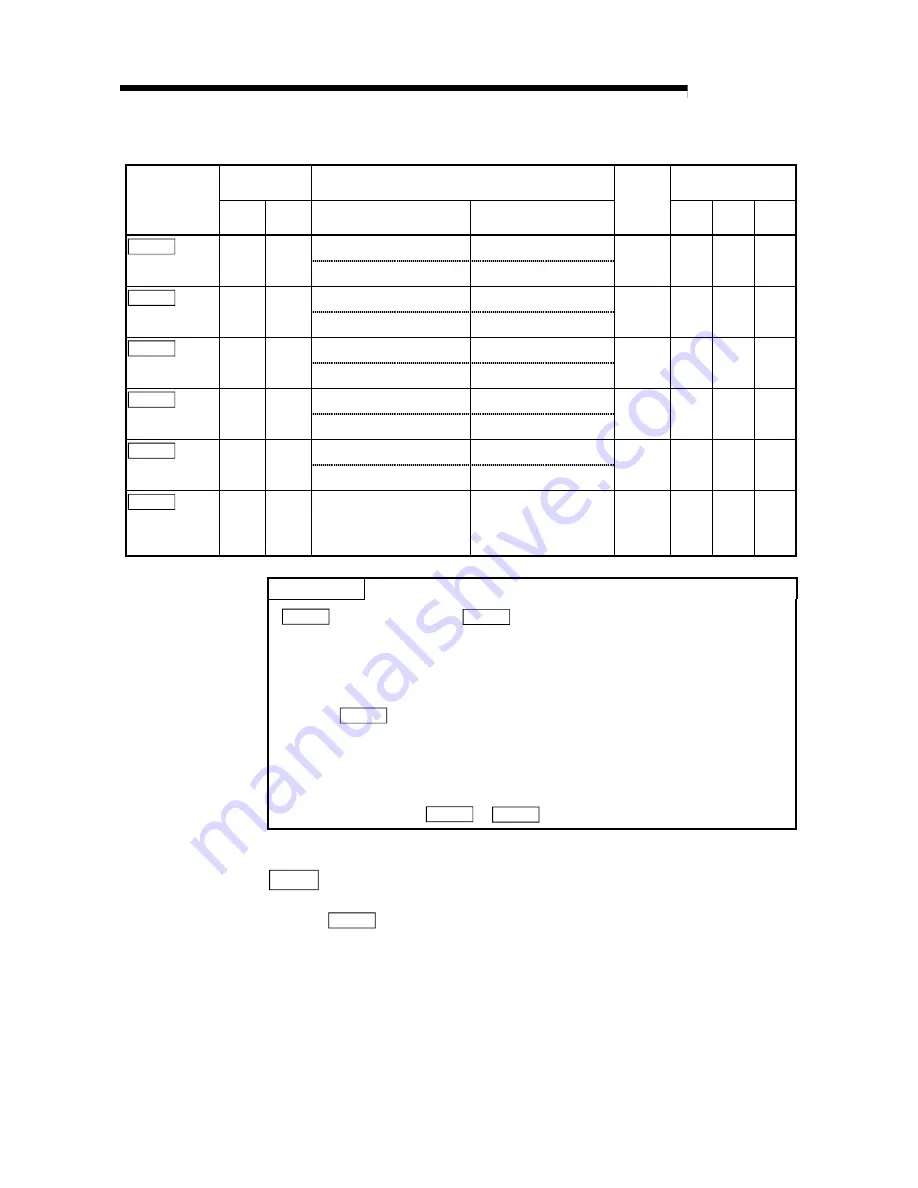
5 - 92
MELSEC-A
5 DATA USED FOR POSITIONING CONTROL
(2) Servo adjustment parameters
Servo amplifier
side parameter
Setting value, setting range
Setting value buffer
memory address
Item
No.
Abbre-
viation
Value set with peripheral
device
Value set with sequence
program
Default
value
Axis 1 Axis 2 Axis 3
0.0 to 100.0 (%)
0 to 1000 (0.1%)
Pr.112
Load inertia
ratio
No.12 GD2
–
1001 to 3000 (0.1%)
30 112 262 412
4 to 1000 (rad/s)
4 to 1000 (rad/s)
Pr.113
Position loop
gain 1
No.13 PG1
–
1001 to 2000 (rad/s)
70 113 263 413
20 to 5000 (rad/s)
20 to 5000 (rad/s)
Pr.114
Speed loop
gain 1
No.14 VG1
–
5001 to 8000 (rad/s)
1200 114 264 414
1 to 500 (rad/s)
1 to 500 (rad/s)
Pr.115
Position loop
gain 2
No.15 PG2
–
501 to 1000 (rad/s)
25 115 265 415
20 to 8000 (rad/s)
20 to 8000 (rad/s)
Pr.116
Speed loop
gain 2
No.16 VG2
–
8001 to 20000 (rad/s)
600 116 266 416
Pr.117
Speed
integral
compensation
No.17
VIC
1 to 1000 (ms)
1 to 1000 (ms)
20
117
267
417
POINT
"
Pr.112
Load inertia ratio" to "
Pr.117
Speed integral compensation" are
transferred to the servo amplifier when the PLC CPU is powered ON or reset or the
PLC READY signal [Y1D] turns ON. When auto tuning is executed and operation is
performed, however, they are changed to the optimum values in the servo amplifier.
At this time, the auto tuning results are not reflected on the AD75.
Hence, if "
Pr.108
Auto tuning" is changed to "2: Manual mode 2" and the PLC
CPU is powered ON or reset or the PLC READY signal [Y1D] is turned ON, the
settings return to the status before auto tuning, and the motor may vibrate.
When it is desired to save the optimum values obtained by auto tuning, set the data
read from the buffer memory addresses 858 to 863 (Axis 1), 958 to 963 (Axis 2),
1058 to 1063 (Axis 3) to
Pr.112
to
Pr.117
, and perform write to flash ROM.
Pr.112
Load inertia ratio (Ratio of load inertia to servomotor inertia)
Set the ratio of load inertia to servomotor inertia.
When "
Pr.108
Auto tuning" is set to "0: Interpolation mode" or "1: Auto tuning
mode 1", this parameter is automatically changed to the auto tuning result in the
servo amplifier.
On the peripheral device, any value in the range 0.0 to 100.0% can be set since
the setting is made as the MR-J2-B.
When setting any of 100.1 to 300.0%, set this parameter in the sequence program.
Summary of Contents for A1SD75M1
Page 2: ......
Page 20: ...A 18 MEMO...
Page 22: ...MEMO...
Page 27: ...1 5 MELSEC A 1 PRODUCT OUTLINE MEMO...
Page 42: ...1 20 MELSEC A 1 PRODUCT OUTLINE MEMO...
Page 52: ...2 10 MELSEC A 2 SYSTEM CONFIGURATION MEMO...
Page 111: ...5 21 MELSEC A 5 DATA USED FOR POSITIONING CONTROL MEMO...
Page 115: ...5 25 MELSEC A 5 DATA USED FOR POSITIONING CONTROL MEMO...
Page 123: ...5 33 MELSEC A 5 DATA USED FOR POSITIONING CONTROL MEMO...
Page 127: ...5 37 MELSEC A 5 DATA USED FOR POSITIONING CONTROL MEMO...
Page 167: ...5 77 MELSEC A 5 DATA USED FOR POSITIONING CONTROL MEMO...
Page 193: ...5 103 MELSEC A 5 DATA USED FOR POSITIONING CONTROL MEMO...
Page 276: ...5 186 MELSEC A 5 DATA USED FOR POSITIONING CONTROL MEMO...
Page 332: ...7 18 MELSEC A 7 MEMORY CONFIGURATION AND DATA PROCESS MEMO...
Page 334: ...MEMO...
Page 422: ...9 64 MELSEC A 9 MAIN POSITIONING CONTROL MEMO...
Page 446: ...10 24 MELSEC A 10 ADVANCED POSITIONING CONTROL MEMO...
Page 472: ...11 26 MELSEC A 11 MANUAL CONTROL MEMO...
Page 576: ...12 104 MELSEC A 12 CONTROL AUXILIARY FUNCTIONS MEMO...
Page 745: ......