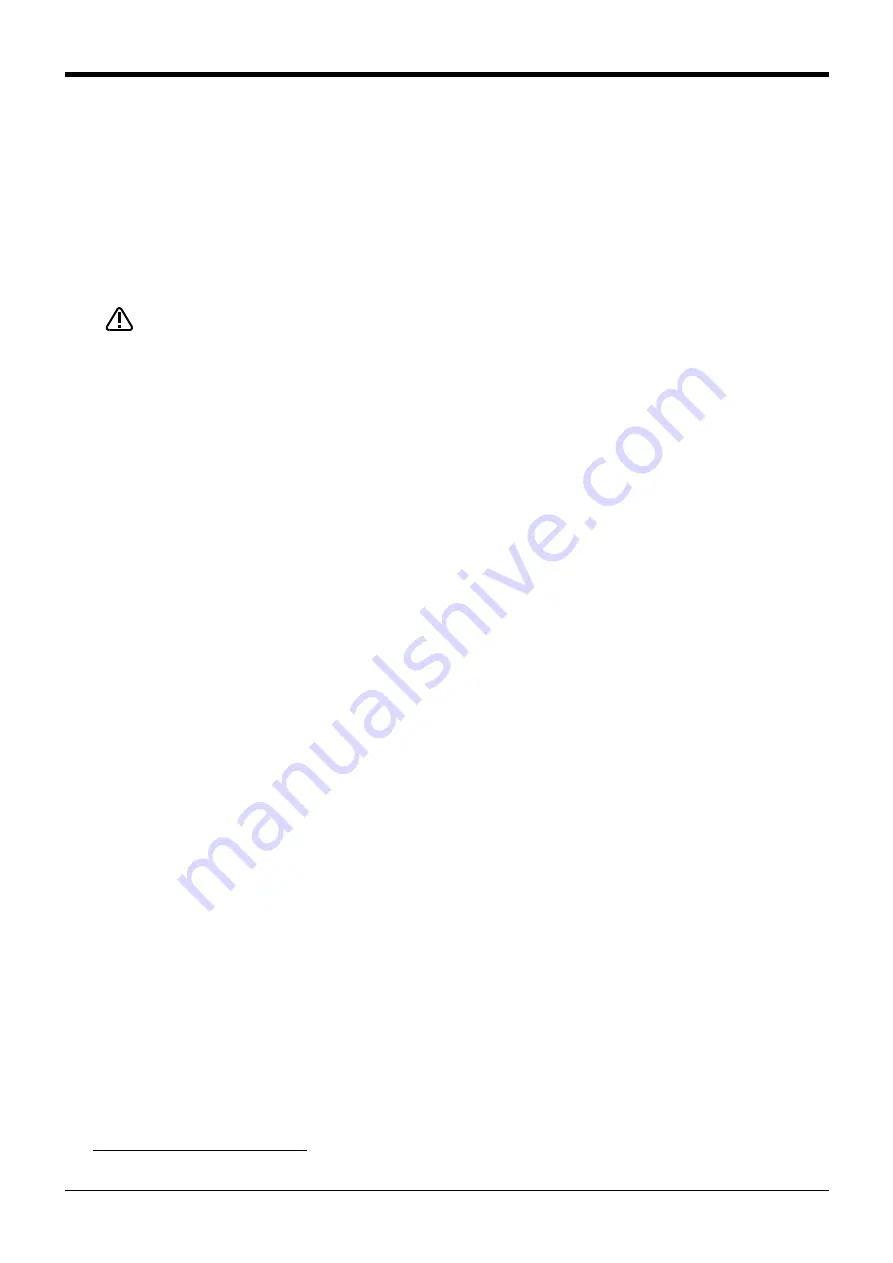
6Safety
Working environment
6-110
6.2 Working environment
Avoid installation in the following places as the equipment's life and operation will be affected by the ambient
environment conditions. When using in the following conditions, the customer must pay special attention to the
preventive measures.
(1) Power supply
・ Where the voltage fluctuation will exceed the input voltage range.
・ Where a momentary power failure exceeding 20ms may occur.
・ Where the power capacity cannot be sufficiently secured.
Please use the controller with an input power supply voltage fluctuation rate of 10% or
less. In the case of 200 VAC input, for example, if the controller is used with 180 VAC
during the day and 220 VAC during the night, turn the servo off once and then on again.
If this is not performed, an excessive regeneration error may occur.
(2) Noise
・ Where a surge voltage exceeding 1000V, 1μs may be applied on the primary voltage. Near large inverters, high
output frequency oscillator, large contactors and welding machines. Static noise may enter the lines when this
product is used near radios or televisions. Keep the robot away from these items.
(3) Temperature and humidity
・ Where the atmospheric temperature exceeds 40 degree , lower than 0 degree.
・ Where the relative humidity exceeds 85%, lower than 45%, and where dew may condense.
・ Where the robot will be subject to direct sunlight or near heat generating sources such as heaters.
(4) Vibration
・ Where excessive vibration or impact may be applied. (Use in an environment of 34m/s
2
or less during transpor
-
tation and 5m/s
2
or less during operation.)
(5) Installation environment
・ Where strong electric fields or magnetic fields are generated.
・ Where the installation surface is rough. (Avoid installing the robot on a bumpy or inclined floor.)
・ Where there is heavy powder dust and oil mist present.
6.3 Precautions for handling
(1) RV-2SD has brakes of J2, J3 and J5 axes. RV-2SDB has brakes of all axes. The precision of the robot may
drop, looseness may occur and the reduction gears may be damaged if the robot is moved with force with the
brakes applied. Moreover, when the axis without the brake is servo-off, take care to falling by the self-weight.
(2) Avoid moving the robot arm by hand. When unavoidable, gradually move the arm. If moved suddenly, the accu
-
racy may drop due to an excessive backlash, or the backed up data may be destroyed.
(3) Note that depending on the posture, even when within the movement range, the section could interfere with
the base section. Take care to prevent interference during jog.
*1)
(4) The robot arm is configured of precision parts such as bearings. Grease is used for lubricating these parts.
When cold starting at low temperatures or starting operation after long-term stoppage, the position accuracy
may drop or servo alarms may occur. If these problems occur, perform a 5 to 10 minute running-in operation at
a low speed (about a half of normal operating speed).
(5) The robot arm and controller must be grounded with Class D grounding to secure the noise resistance and to
prevent electric shocks.
(6) The items described in these specifications are conditions for carrying out the periodic maintenance and
inspections described in the instruction manual.
(7) When using the robot arm on a mobile axis or elevating table, the machine cables enclosed as standard config
-
uration may break due to the fixed installation specifications. In this case, use the machine cable extension (for
flexed)" factory shipment special specifications or options.
(8) If this robot interferes with the workpiece or peripheral devices during operation, the position may deviate, etc.
Take care to prevent interference with the workpiece or peripheral devices during operation.
*1) Jog operation refers to operating the robot manually using the teaching pendant.
CAUTION
Summary of Contents for MELFA RV-2SD Series
Page 2: ......
Page 122: ......
Page 123: ......
Page 124: ......
Page 125: ......
Page 126: ......
Page 127: ......
Page 128: ......
Page 129: ......
Page 130: ......
Page 131: ......
Page 132: ......
Page 133: ......
Page 134: ......
Page 135: ......
Page 136: ......
Page 137: ......
Page 138: ......
Page 139: ......
Page 140: ......
Page 141: ......
Page 142: ......
Page 143: ......
Page 144: ......
Page 145: ......
Page 146: ......
Page 147: ......
Page 148: ......
Page 149: ......