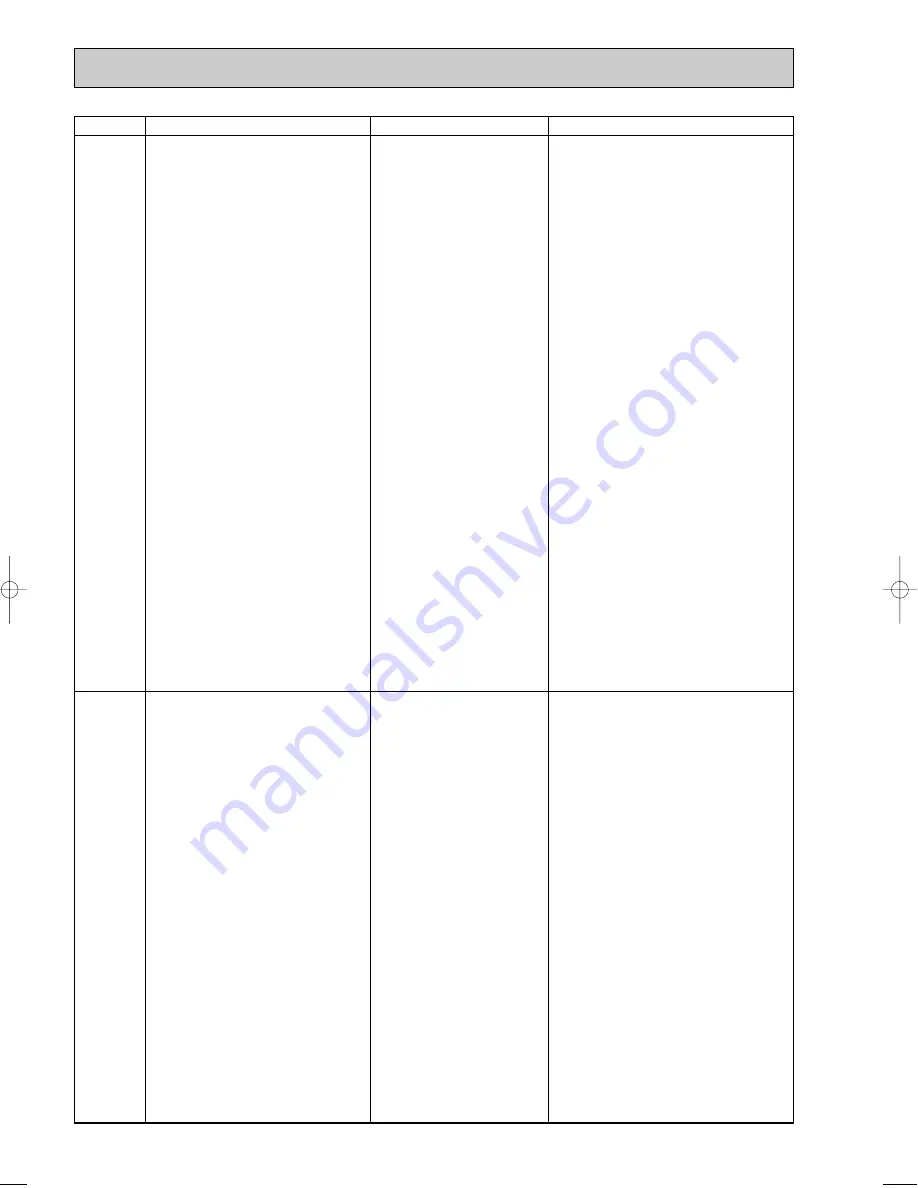
20
Error Code Meaning of error code and detection method
Cause
Countermeasure
P6
Freezing/overheating protection is
working
1
Freezing protection (Cooling mode)
The unit is in six-minute resume prevention
mode if pipe <liquid or condenser/evap-
orator> temperature stays under
-15
:
for three minutes, three minutes
after the compressor started. Abnormal
if it stays under -15
:
for three minutes
again within 16 minutes after six-minute
resume prevention mode.
<Frost prevention mode>
If pipe <liquid or condenser-evaporator>
temperature is 2
:
or below when 16
minutes has passed after compressor
starts operating, unit will start operating
in frost prevention mode which stops
compressor operation. After that, when
pipe <liquid or condenser/evaporator>
temperature stays 10
:
or more for 3
minutes, frost prevention mode will be
released and compressor will restart its
operation.
2
Overheating protection (Heating mode)
The units is in six-minute resume
prevention mode if pipe <condenser /
evaporator> temperature is detected as
over 70
:
after the compressor started.
Abnormal if the temperature of over
70
:
is detected again within 10 minutes
after six-minute resume prevention
mode.
P8
1
Slight temperature difference
between indoor room
temperature and pipe <liquid
or condenser / evaporator>
temperature thermistor
• Shortage of refrigerant
• Disconnected holder of pipe
<liquid or condenser /
evaporator> thermistor
• Defective refrigerant circuit
2
Converse connection of
extension pipe (on plural units
connection)
3
Converse wiring of indoor/
outdoor unit connecting wire
(on plural units connection)
4
Defective detection of indoor
room temperature and pipe
<condenser / evaporator>
temperature thermistor
5
Stop valve is not opened
completely.
(Cooling or drying mode)
1
Clogged filter (reduced airflow)
2
Short cycle of air path
3
Low-load (low temperature)
operation beyond the tolerance
range
4
Defective indoor fan motor
• Fan motor is defective.
• Indoor controller board is
defective.
5
Defective outdoor fan control
6
Overcharge of refrigerant
7
Defective refrigerant circuit
(clogs)
(Heating mode)
1
Clogged filter (reduced airflow)
2
Short cycle of air path
3
Over-load (high temperature)
operation beyond the tolerance
range
4
Defective indoor fan motor
• Fan motor is defective.
• Indoor controller board is
defective.
5
Defective outdoor fan control
6
Overcharge of refrigerant
7
Defective refrigerant circuit
(clogs)
8
Bypass circuit of outdoor unit
is defective.
(Cooling or drying mode)
1
Check clogs of the filter.
2
Remove shields.
4
Measure the resistance of fan motor's winding.
Measure the output voltage of fan's connector
(FAN) on the indoor controller board.
W
The indoor controller board should be
normal when voltage of AC 220~240V is
detected while fan motor is connected.
Refer to 9-7.
5
Check outdoor fan motor.
67
Check operating condition of refrigerant
circuit.
(Heating mode)
1
Check clogs of the filter.
2
Remove shields.
4
Measure the resistance of fan motor's
winding.
Measure the output voltage of fan's connector
(FAN) on the indoor controller board.
W
The indoor controller board should be
normal when voltage of AC 220~240V is
detected while fan motor is connected.
Refer to 9-7.
5
Check outdoor fan motor.
6
~
8
Check operating condition of refrigerant
circuit.
Abnormality of pipe temperature
<Cooling mode>
Detected as abnormal when the pipe tem-
perature is not in the cooling range 3 min-
utes later of compressor start and 6 min-
utes later of the liquid or condenser/evapo-
rator pipe is out of cooling range.
Note 1) It takes at least 9 min. to detect.
Note 2) Abnormality P8 is not detected in
drying mode.
Cooling range : -3 deg
]
(TH-TH1)
TH: Lower temperature between: liquid
pipe temperature (TH2) and con-
denser/evaporator temperature (TH5)
TH1: Intake temperature
<Heating mode>
When 10 seconds have passed after the
compressor starts operation and the hot
adjustment mode has finished, the unit is
detected as abnormal when
condenser/evaporator pipe temperature is
not in heating range within 20 minutes.
Note 3) It takes at least 27 minutes to
detect abnormality.
Note 4) It excludes the period of defrosting
(Detection restarts when defrosting
mode is over)
Heating range : 3 deg
[
(TH5-TH1)
1
~
4
Check pipe <liquid or condenser /
evaporator> temperature with room
temperature display on remote
controller and outdoor controller circuit
board.
Pipe <liquid or condenser / evaporator>
temperature display is indicated by
setting SW2 of outdoor controller circuit
board as follows.
23
Check converse connection of extension
pipe or converse wiring of indoor/outdoor
unit connecting wire.
Conduct temperature check with outdoor
controller circuit board after connecting
‘A-Control Service Tool(PAC-SK52ST)’.
(
)
OC330--1.qxp 05.5.9 1:30 PM Page 20