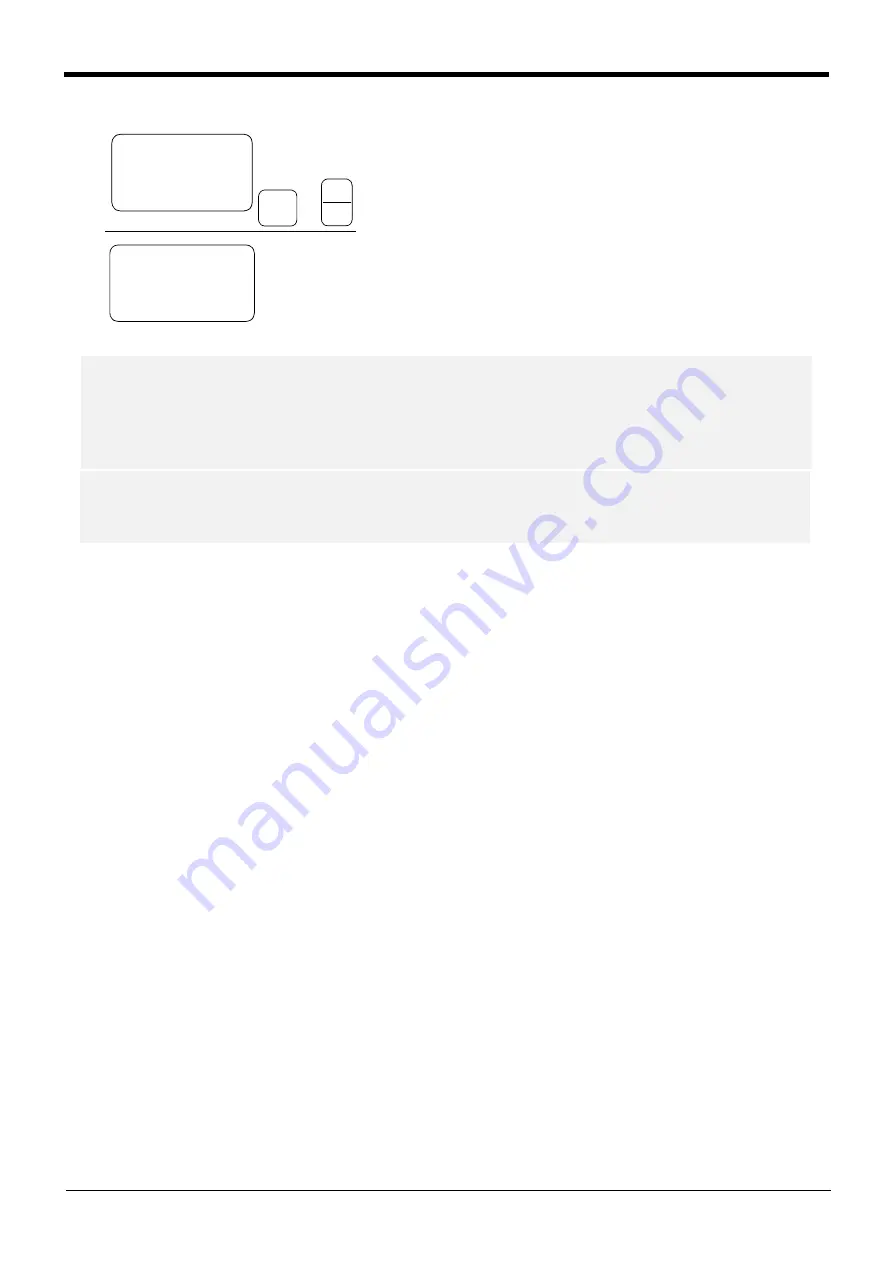
5-76
Resetting the origin
5Maintenance and Inspection
9) Press the [
1
] and [INP] keys.
The origin posture will be set.
1
0) Setting of the origin is completed.
11
) Refer to
"5.5.5Recording the origin data" on
in this manual, and record the origin data
on the origin data seal.
Set the origin
-B
(J5)
1
DEF
<MECHA>
SET ORIGIN
OK?(1)
1:EXECUTE
INP
EXE
→
<MECHA> 12345678
BRAKE (00000100)
SET AXIS(00000100)
ORIGIN:COMPLETED
◇◆◇
Releasing the brakes
◇◆◇
To release the brakes, move the cursor to the "BRAKE" axis No. with the [
←
] or [
→
] key.
The brakes can be released only for the axis for which a "
1
" is displayed on the screen. If the brakes are not to
be released, press the [0] key and display a "0".
If the [+X] key on the teaching pendant or the deadman switch is pressed while the brakes are released, the
brakes will be applied immediately.
◇◆◇
Origin setting axis designation
◇◆◇
Move the cursor to the "SET AXIS" axis No. in the origin setting with the [
←
] or [
→
] key.
The origin is set only for the axis for which a "
1
" is displayed on the screen. If the origin is not to be set, press
the [0] key and display a "0".