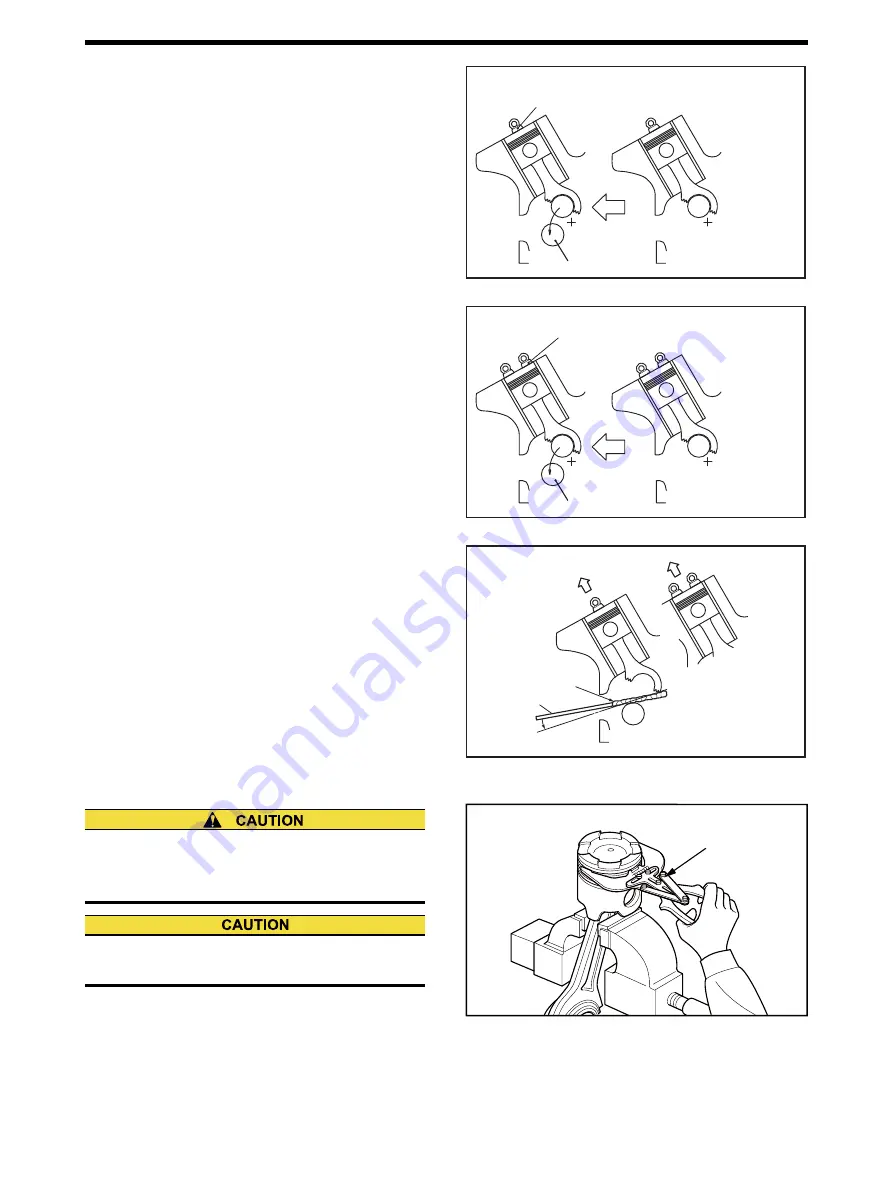
5-20
Chapter 5 DISASSEMBLY OF BASIC ENGINE
4.5.2 Removing the Piston With Pushing-up the Con-
necting Rod Big End
(1)
Remove the connecting rod cap and rotate the crank-
shaft to bring the piston to the top dead center position.
(2)
Install the eye bolt to the threaded hole on the piston
top, and support the piston to prevent it from falling
down.
(3)
Rotate the crankshaft carefully until the crankpin is dis-
placed from the connecting rod and the lower bolt hole
can be seen trough the inspection window.
(4)
Insert a bar wrapped with cloth, and push up the bottom
of connecting rod carefully, with the crankpin as a ful-
crum.
Note: Protect the crankpin and connecting rod big end with
cloth or rubber to prevent them from damage with the
bar.
(5)
Push-up the connecting rod and piston while adjusting
the supporting position.
When the oil ring is slid out of the cylinder liner, care-
fully put the piston on the top face of cylinder liner.
(6)
Lift the piston with eye bolt on the piston top, and pull-
out the piston from cylinder liner.
Crankshaft - Rotate (1)
Crankshaft - Rotate (2)
Connecting Rod Big End - Push-Up
4.6 Piston Ring - Remove
Hold the piston and connecting rod in a vise, and remove
the piston rings with ring expander.
Piston Ring - Remove
Crankpin
Weight of piston and
connecting rod
assembly:
approx 19.8 kg [44 lb]
Eyebolt
P/N:45815-32301
(M10 × 1.5 mm)
Crankpin
Weight of piston and
connecting rod
assembly:
approx 19.8 kg [44 lb]
Eyebolt
P/N:45815-32201
(M8 × 1.25 mm)
Turning bar
Wrap in cloth
When removing the piston ring, be careful not to be
pinched your hand between the piston and connecting
rod by piston swing.
A free swing of piston and its bump to connecting rod
may result in piston damage.
Ring expander
P/N : 37191-03200
Summary of Contents for S12A2
Page 1: ...SERVICE MANUAL September 2010 Pub No 99269 20170 199269 20170 ...
Page 2: ......
Page 16: ......
Page 20: ......
Page 42: ......
Page 44: ......
Page 68: ......
Page 69: ...3 1 Chapter 3 SERVICE TOOLS 1 Special Tools 3 3 ...
Page 70: ......
Page 78: ......
Page 82: ......
Page 136: ......
Page 174: ......
Page 218: ......
Page 220: ......
Page 242: ......
Page 244: ......
Page 294: ......
Page 310: ......
Page 320: ......
Page 322: ......
Page 334: ......
Page 354: ......