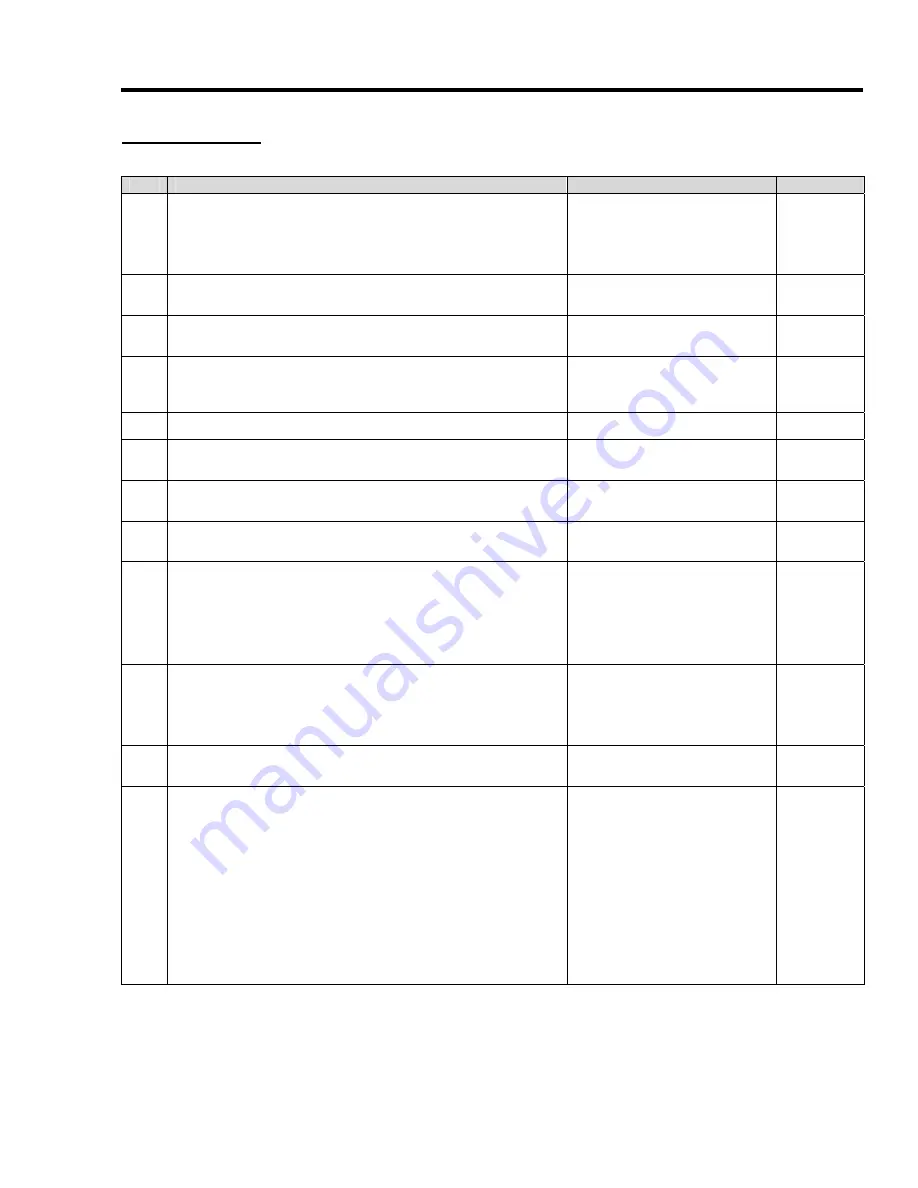
MKS MultiGas High-Speed Gas Sampling Cart
Cart
Daily
Use
STEP
ACTION
NOTES
COMPLETED
1.
The cart requires a 5-hour warm-up time. It is recommended to keep
the system powered-on at all times.
If starting with a cold system, see the “power up” section of this
manual.
2.
Turn off pumps when not in use.
The pumps may be turned off when
not sampling.
3.
Periodically drain water condensation from the Backpressure
reservoir. Drain valve found at the bottom of the reservoir.
4.
Verify temperature readings are stable:
HTD LINE 2: 191°C
HTD BOX: 191°C
5.
Verify that FM1 valve is in the full open position.
6.
Verify that the back pressure regulator is fully-clockwise to decrease
the backpressure through the system.
7.
Verify that the sample line is connected. Make sure the Swagelok
quick connect is properly seated.
8.
Turn the MV1 valve in the Span / N
2
position.
The valve handle moves left to
right in a lower arc.
9.
Turn MV2 to the N
2
position.
This is done to purge the MultiGas
gas cell with Nitrogen gas so the
daily checks can be performed and
a new background reading can be
taken. See MultiGas SOP for daily
checks.
10.
When Daily checks are completed and a new background has been
taken, turn the MV1 valve in the Sample position
When the MV1 valve is moved
from N
2
/Span to Sample all flow
through the MV2 is stopped.
11.
Verify that the HTD LINE 2 and HTD BOX temperatures are 191°C
then turn ON the Pump.
12.
Use the back pressure regulator to achieve the desired flow rate and
gas cell pressure. The pressure measured in the MG2000 should be at
1.0 atm ± 0.05atm.
If the pressure drops during the
sampling:
- The filter may be coated with
particulate
- Issue with the pumps, check to
see if both pumps
are running. Check front and
rear cowling to see
if the fan is spinning.
- Restriction in the sample line
Installation and Use Manual 2011 APRIL 2 Rev. 1.5
32