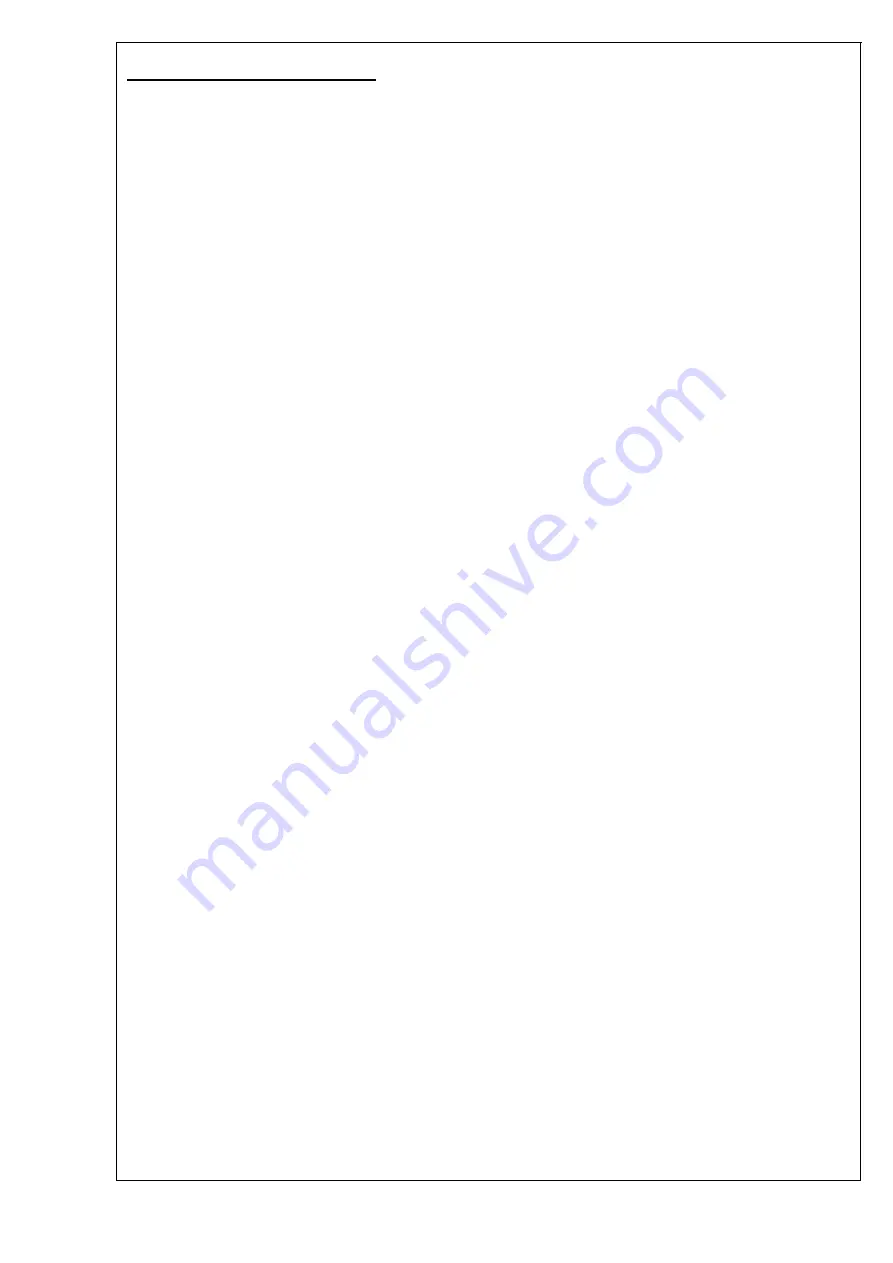
Operation & Maintenance, Page
18
of
23
Section
3
– Revision 2.3
Gearbox Fitting Procedure:
m
Clean the output shaft of the gearbox and the gear coupling.
m
Slide the coupling half onto the output shaft.
m
Fit the end cap onto the output shaft. Threadlock should be applied to the bolts prior to fitting.
m
Lift the gearbox into position, ensuring that the spigot on the gearbox mates with the recess on the gearbox mounting
plate. Fit the studs/bolts connecting the gearbox to the gearbox mounting plate, and torque to the amount specified
in MMD procedure T056.
m
Align the teeth on the coupling half, with the teeth on the coupling sleeve, and slide the coupling sleeve into position.
m
Ensure ‘O’ rings are correctly seated on the coupling sleeve, and fit the two split clamping rings around the coupling.
Tighten bolts in accordance with MMD procedure T056.
m
Fill the gearbox with the correct lubricant to the designated level. (See Maintenance Schedule for Specification).
m
Fill the gear coupling with grease. (See Maintenance Schedule for Specification).