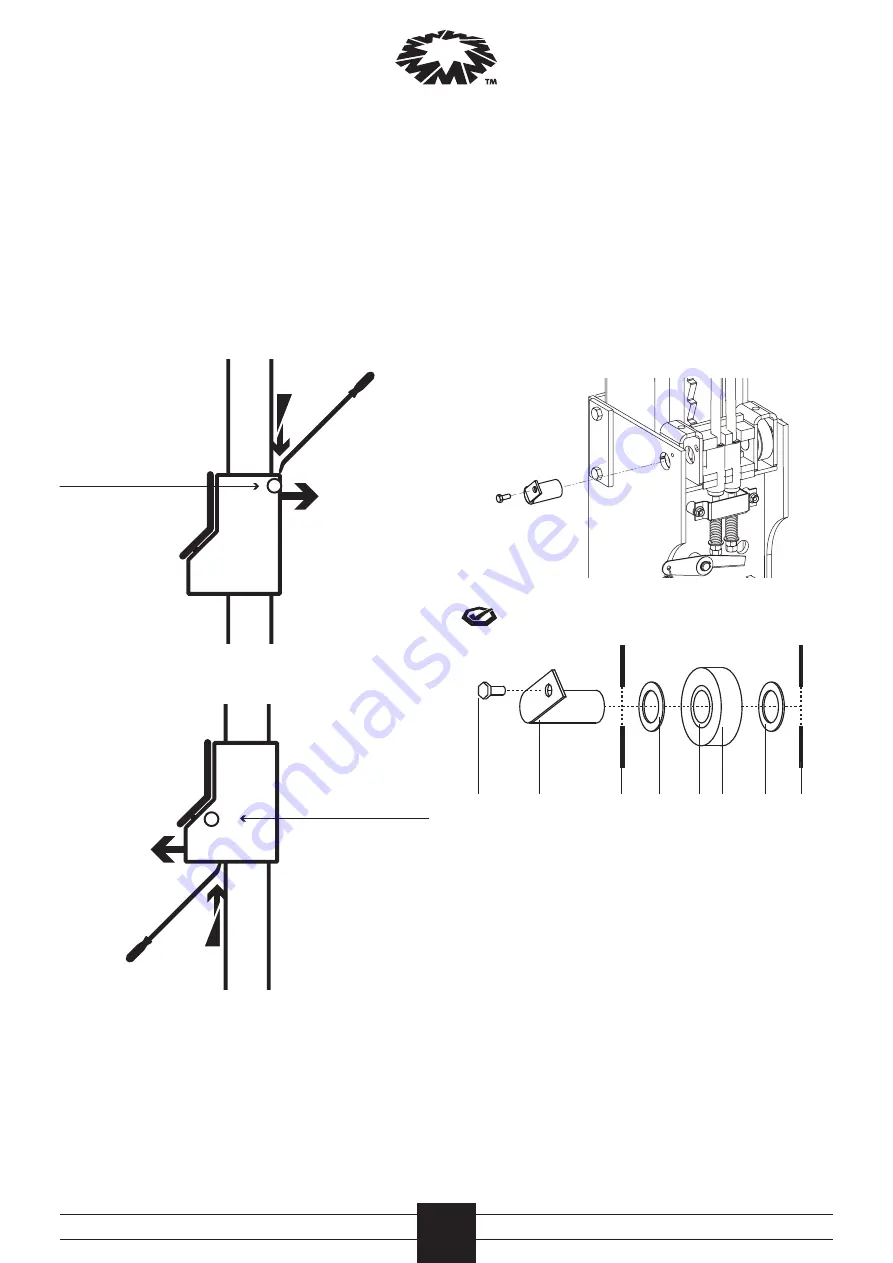
Molnar Hoists
All Rounder
Servicing
7
Check Carriage rollers
Check Carriage Rollers
1
Raise hoist to a comfortable working height.
2
Pry the carriage away from post (to remove the load off
the rollers) and wedge in position.
2
b For the outside rollers wedge from the top of the carriage
(as illustrated above). For the inside rollers, wedge from
beneath the carriage (as illustrated below).
location of outside roller
location of inside roller
3
With the load off the rollers (load is now held by wedge)
check that the rollers rotate freely
4
Remove side bolt and slide out roller pin, roller and
spacers.
Note the orientation of the roller,
as it must be refitted in the same orientation.
5
Remove spacers and clean bush and pin. Inspect bush
and replace if necessary (ensure minimal non-rotational/
sideways movement between pin and bush) .
The roller must be at least 60mm in diameter with no flat
spots on the surface; otherwise replace.
6
Re-lubricate the inside of the bush (with grease). Use
grease to adhere the spacers to the sides of the roller.
Reinsert roller into carriage and insert the pin. Fasten the
side bolt.
7
Use a pry bar to remove wedge.
8
Perform for all load rollers on both carriages.
side bolt
roller pin
carriage
carriage
spacer
spacer
roller
bush
CAD