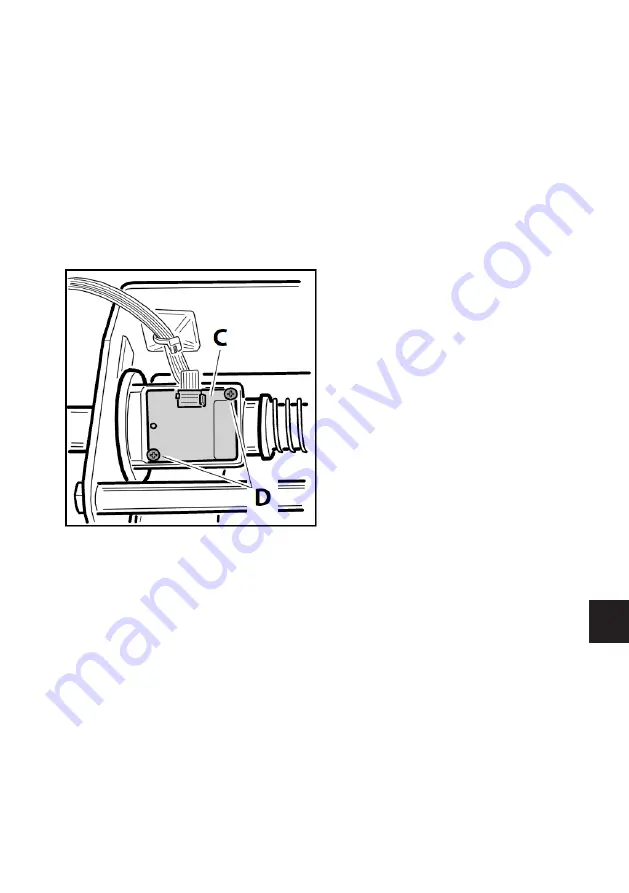
Technical service manual
13
UK
Check the following if the sensor (A, Fig. 2a) does not read:
- the connection flat;
- that the sensor is correctly assembled in its housing.
If these checks do not rectify the problem, replace the sensor (A, fig.2a) as follows:
- remove the weight tray
- remove the sensor lever;
- disconnect the Picoflex from the sensor;
- remove the sensor A, undoing the two fastener screws (B, fig.2a);
- replace the sensor, assembling it by following the disassembly directions in the
reverse order;
- check the sensor reads correctly, as indicated above.
Distance sensor [d]
Fig.2b
Check that the total travel is 750 notches (maximum permissible error +/- 5 notches
along entire travel);
Check the following if the sensor (C, Fig. 2b) does not read:
- the connection flat;
- the correct mounting of the sensor in its housing (Picoflex connector in the direction
of the swinging unit);
If the sensor needs to be replaced:
- remove the weight tray
- Disconnect the Picoflex connector;
- undo the two self-tapping screws (D, fig.2b) then remove the sensor from its mount-
ing;
- mount the new sensor, paying attention to the correct fixing direction of the sensor
itself;
- Check that the sensor is working correctly using programme 98 “Display internal sen-
sor function”.
Summary of Contents for MT 2450
Page 1: ...MT 2450 Code 4 131046_uk 12 2013 Technical service manual...
Page 25: ...Technical service manual 25 UK Note...
Page 27: ...Technical service manual 27 UK...
Page 28: ...28 Technical service manual...
Page 29: ...Technical service manual 29 UK Cod 4 101700...
Page 30: ...30 Technical service manual...
Page 31: ...Technical service manual 31 UK...
Page 32: ...32 Technical service manual...
Page 33: ...Technical service manual 33 UK Cod 457674B...
Page 34: ...34 Technical service manual...