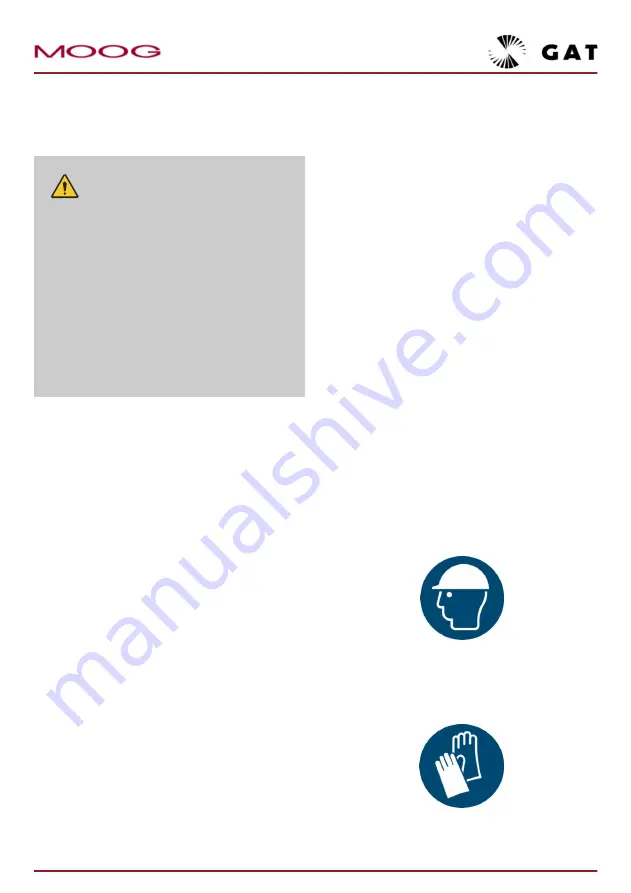
2.4 Staff requirements
2.4.1 Qualifications
WARNING!
Danger due to insufficiently qualified
personnel!
Insufficiently qualified personnel are not
capable of assessing the risks when using
the device and expose themselves and
others to the risk of serious or even fatal
injuries.
– All work must be carried out by appro-
priately qualified personnel only.
– Insufficiently qualified and unauthor-
ised personnel must be kept away from
the danger and working zone.
Only personnel who can be expected to carry out
this work reliably are authorised as staff. Per-
sonnel whose reactions are impaired, e.g. by
drugs, alcohol or medication, are not authorised.
The required qualifications for personnel and the
various tasks are listed in these instructions as fol-
lows:
Electrician
Due to his professional knowledge, training and
experience, as well as his knowledge of the appli-
cable standards and regulations, the electrician is
in a position to perform work on electrical systems
and to detect and avoid possible dangers by him-
self.
The electrician is trained specially for his work
environment and is familiar with the relevant stan-
dards and regulations.
Specialist staff
Specialist staff are capable of carrying out the
assigned work and identifying and preventing pos-
sible hazards independently due to their specialist
qualification, knowledge and experience of han-
dling rotary feedthrough and familiarity with the
valid standards and regulations.
Transport specialist
The transport specialist is trained to perform trans-
port work with a crane or forklift. The transport
specialist is able to choose suitable fastening
equipment according to transport requirements
and handle it professionally. The transport spe-
cialist has been trained for transportation by fork
lift on the machine and is able to operate it.
The transport specialist is trained specially for the
work environment in which they are active and is
familiar with the relevant regulations.
Depending on the area of application, additional
knowledge of working in explosive areas and of
using special tools and aids may be required.
2.5 Personal protective equipment
Personal protective equipment serves to protect
people against hazards to their safety and health
while working.
The personnel must wear the personal protective
equipment while working on and with the device
which is referred specially to in the individual sec-
tions of these instructions.
Description of the personal protective equip-
ment
The personal protective equipment is explained
below:
Industrial helmet
Industrial helmets protect the head against falling
objects, swinging loads and impacts with fixed
objects.
Protective gloves
Rotopack • Operating instructions
9