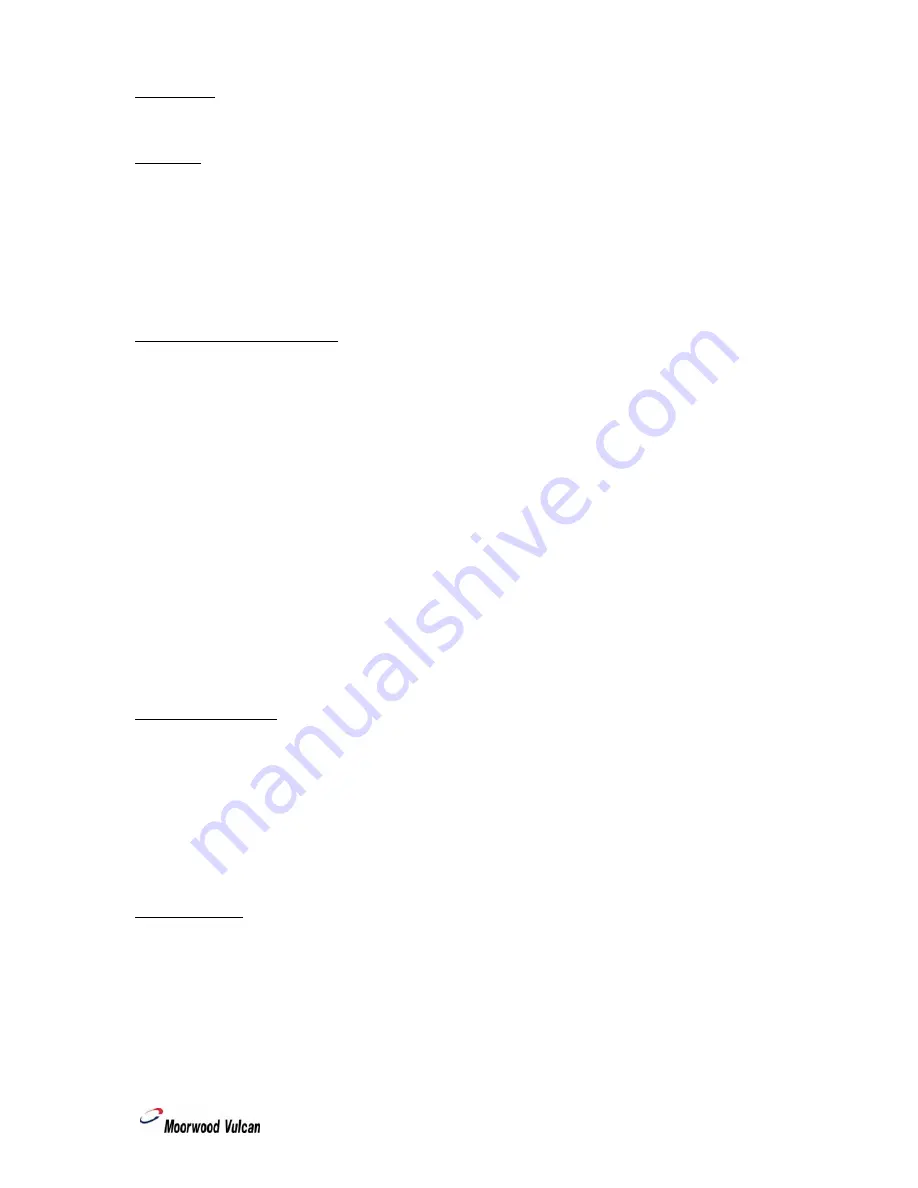
Manual Part No: 931764-01 MV1 Gas Griddle
- 15 –
Manual Rev No: 1
Installation (cont.)
Leak Test
Clean off any protective film from the stainless steel panels.
AT THIS STAGE, LEAK TEST THE WHOLE SYSTEM. THE GAS SAFETY REGULATIONS
require that
ALL
connections in the gas supply line between the Gas Meter and the appliance is tested for gas leaks.
THIS MUST BE DONE BEFORE COMMENCING TO COMMISSION THE APPLIANCE
.
Checking and commissioning
ALTHOUGH EVERY APPLIANCE IS TESTED AND SET BEFORE IT LEAVES THE FACTORY, IT IS
IMPORTANT THAT THE INSTALLER RE-CHECKS CERTAIN FUNCTIONS BEFORE LEAVING THE SITE.
CHECK THE GAS PRESSURE AT THE APPLIANCE THUS
: -
The pressure test point is located on the manifold rail behind the front control panel, which is secured
by two M5 screws.
Connect a manometer (U tube) to the test point. Turn on the gas supply and light all burners. Check
that the pressure reading agrees with that stated on the Data Plate.
SHOULD ADJUSTMENT BE NECESSARY, PROCEED AS FOLLOWS
: -
FOR PROPANE GAS, REFER TO SUPPLIER
.
On the gas governor: -
Remove the cap in order to gain access to the pressure adjusting screw.
Turn the pressure adjusting screw clockwise to increase the pressure or anti-clockwise to decrease it.
When the pressure reading is correct, refit the cap to the governor.
Turn the gas supply to the unit
OFF
at the stopcock and disconnect the manometer (U tube). Ensure that
the pressure test point screw is refitted.
Turn the gas supply to the appliance on at the stopcock and leak test the pressure test point.
Burner Aeration
The aeration of all the burners is fixed and does not need adjusting.
The parts protected by the manufacturer or his agent are not to be adjusted by the installer.
The appliance must be equipotentially earth bonded.