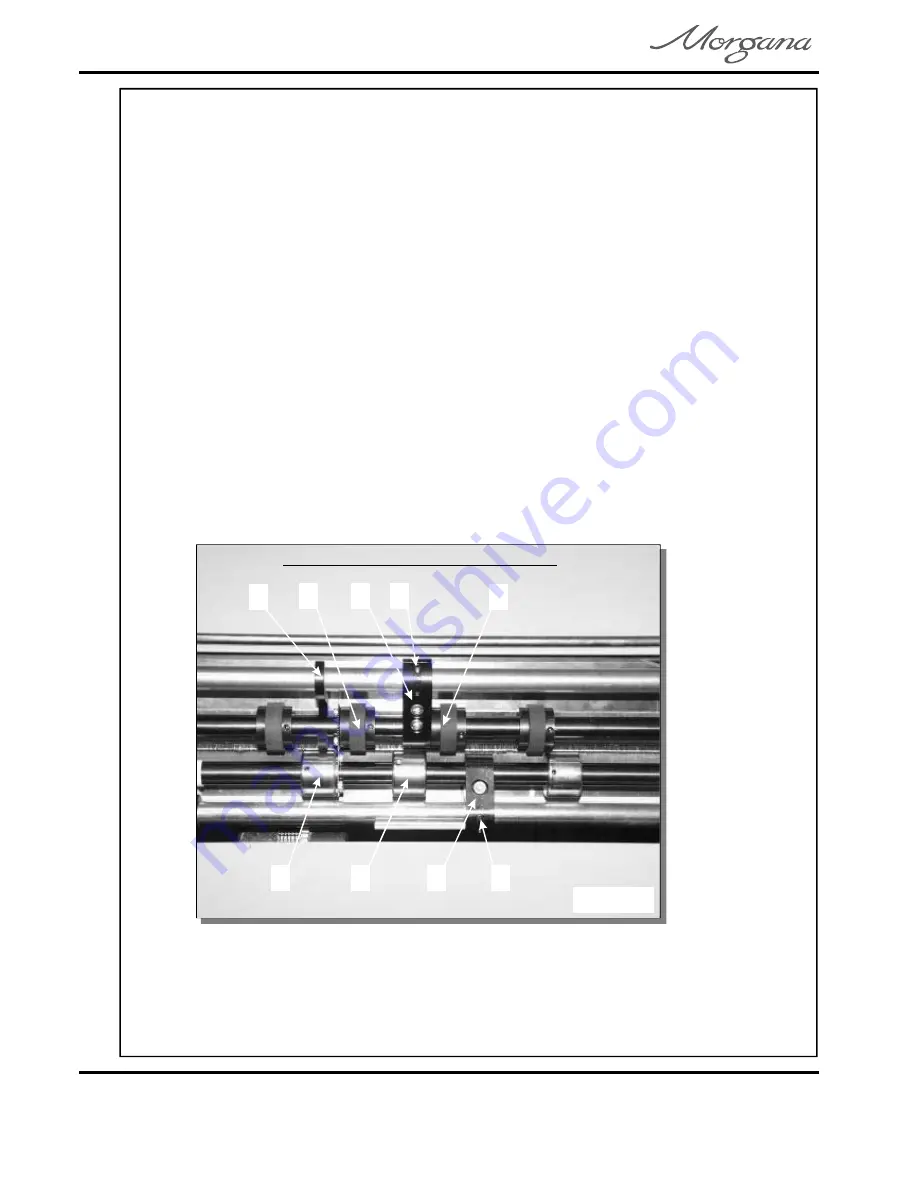
Perforating
11.
Mount the other anvil ensuring that they have matched on the drive hub. Secure the
anvil to the hub ensuring not to over tighten grub screw as shown in fig 16.2.
12.
Slide the drive hub towards the perforating drive wheel until there is a clearance
of 0.5mm.
13.
To prevent damage to the blades or the anvils, do not force the drive wheel against
the hub.
14.
Fix the perforator stripper adjacent to the drive wheel and blade as shown.
15.
Operate the machine and test the perforations for form.
It is important that the drive hubs are arranged evenly across the width of the paper
in order to reduce the risk of jamming.
For multiple perforations repeat the above procedure.
1
– Perforating drive wheel with mounted blades
5
–
2
– Perforator stripper
6
–
Standard drive hub
3
– Standard drive wheel
Always remove blades and anvils once the perforating operation has been
completed to avoid marking on digital or delicate media.
1
4
FIG 17.1
2
3
5
6
7
–
Upper shaft support block
7
Shaft support blocks are mounted on the top and bottom shafts. If they are in a
position that obstructs perforating, they can be slid along just enough to clear the hubs.
They should be mounted as near to the centre of the machine as possible, to
4
– Drive wheel with mounted anvils
Lower shaft support block
Typical set-up for perforating sheets.
8
8
maximise support. The depth of perforation can be adjusted by first loosening the
socket set screws, in the support block, with a 2.5mm allen key. Insert the 2.5mm
allen key into the grub screw, push the allen key up to decrease the perforating depth
or down to increase the depth of perforation. Re-tighten the socket set screws.
(Note. This adjustment can also be carried out on the bottom shaft)
8
– Grub screw
Page 22
CREASING