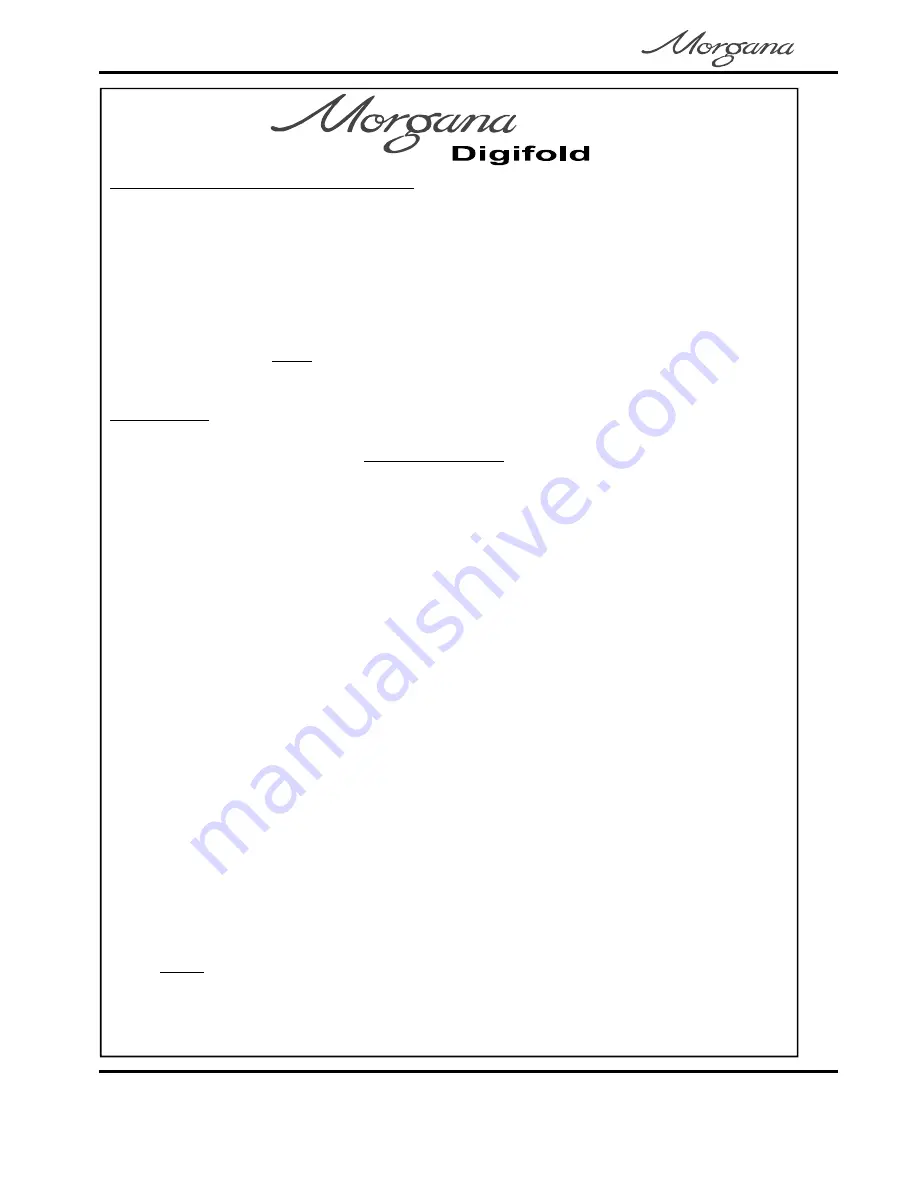
INTRODUCTION
INTRODUCTION AND SPECIFICATION
must
DigiFold
DigiFold
IMPORTANT
is a registered trade mark of Morgana Systems Ltd. The unique patented
creasing and folding system, makes it possible to fold most delicate stocks from 90gsm,
upto and often above 300gsm. The
reduces the possibility of scratching, marking
or cracking appearing on the substrate, as is often associated with conventional folding
machine methods. A maximum paper weight cannot be specified, as this can be governed
by the hardness of the substrate or the type of fold required to be produced.
It is
to note that to prevent cracking, when using dry ink or toner based print
engines, the material
be fully acclimatised for at least 48 hours before putting an
image onto the paper.
Feeding System ................................................ Bottom suction feed
Max. Sheet Size ................................................630mm x 330mm
Min. Sheet Size .................................................140mm x 160mm (dependant on stiffness
of paper and type of fold).
Max. Paper Weight ........................................... 300gsm
(varies according to hardness,
type of fold, and substrate).
Min. Paper Weight ............................................ 120gsm
Max. No. Creases per Sheet ............................ 9
Max. No. Folds per Sheet.................................. 2
Max. No. Stored Programmes ...........................6
Min. Repeat Crease Distance ........................... 4mm (depending on paper weight)
Min. Repeat Fold Distance ................................70
Min. Crease Distance from Leading Edge ........ 25mm
Min. Fold Distance from Leading Edge ............. 70mm (depending on paper weight)
Speed per Hour (A4 Material) One Crease or One Fold..........1800 sheets
Speed per Hour (A4 Material) Two Creases or Two Folds ......1400 sheets
IMPORTANT
Note:
the operating environment should be controlled to a temperature between
16° C and 27° C Maximum.
mm (depending on paper weight)
Min. Crease Distance from Tail Edge ............... 25mm
Min. Fold Distance from Tail Edge .................... 70mm (depending on paper weight)
Max. Fold Length .............................................. 560mm
Min. Fold Length ............................................... 70mm
Speed per Hour (A4 Material) One Crease & One Fold ..........1800 sheets
Speed per Hour (A4 Material) Two Creases & Two Folds .......1400 sheets
Speed per Hour (A3 Material) One Crease or One Fold .........1440 sheets
Speed per Hour (A3 Material) One Crease & One Fold ..........1440 sheets
Speed per Hour (A3 Material) Two Creases or Two Folds ......1200 sheets
Speed per Hour (A3 Material) Two Creases & Two Folds ......1200 sheets
Dimensions ....................................................... L: 1830mm H: 1185mm W: 555mm
Weight ............................................................... 180Kgs (+50Kgs packing)
Power Requirement .......................................... 1 phase 220 / 240v
+
Specification
The production speed varies according to the material size and
the number of creases or folds on the sheet.
Page 4
CREASING / FOLDING