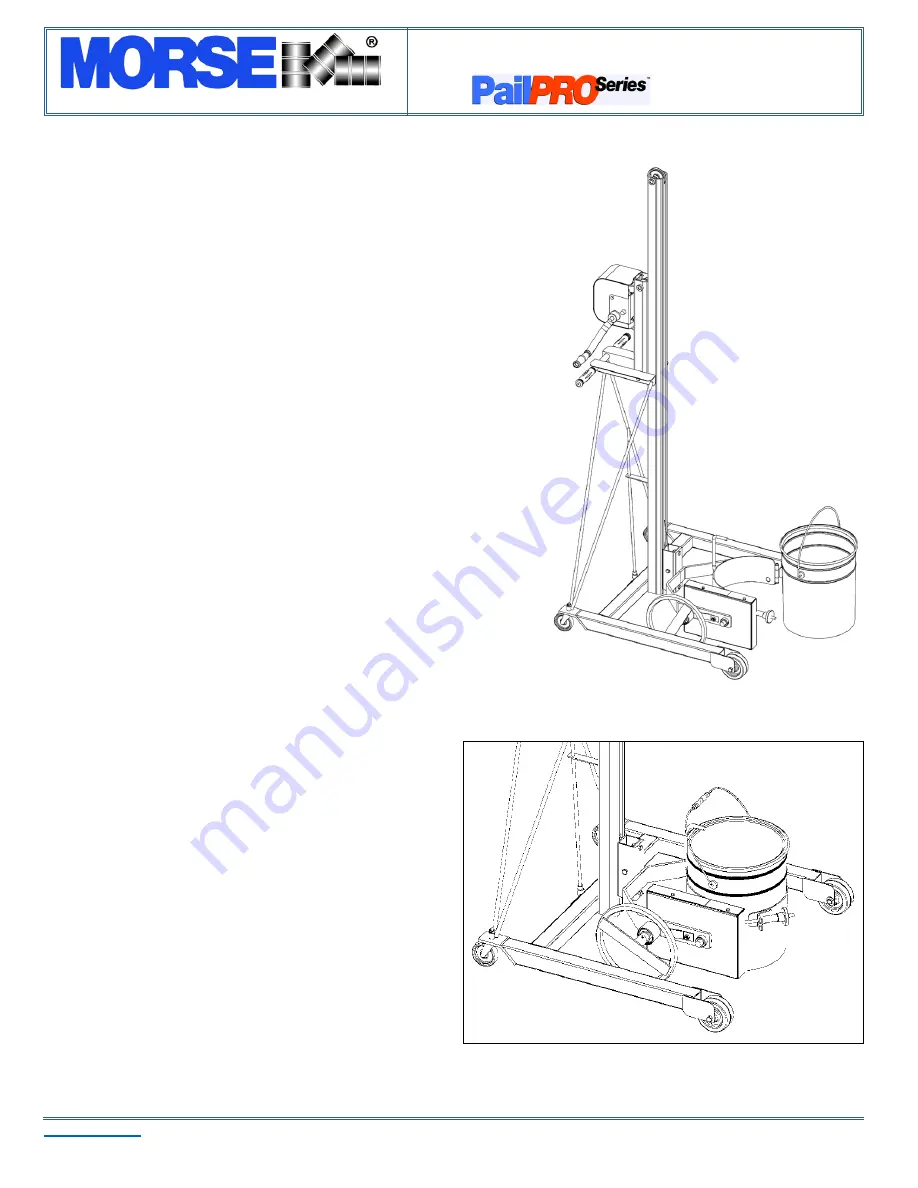
The Specialist In Drum Handling Equipment
Model 83
Pail Handler
operator’s Manual for Morse Model 83
serial number 0819 to ____ (MMYY)
morsedrum.com
Copyright 2020 - Morse Mfg. Co., Inc.
Form PL83 (0819-____)
(Updated 3 Jun, 2020)
6
operating Instructions
1. Push the Pail Handler to the pail.
2. Using the cable winch, crank the handle to position the pail holder assembly
with the back band at the middle of the pail. (see Figure 1). If the pail has a
pivoting wire handle, swing it to lay on the front side to clear the back band.
With the front band hinge plate and clamp screw knob swung open, push
the unit forward until the back band rests firmly against the pail. Engage the
screw down floor lock.
3.
Attaching the pail:
First, swing pivoting wire handle to lay on the back band
side of the saddle. Next, close the front band hinge plate tightly against the
pail (see Figure 2). Swing the clamp screw knob and engage the threaded
rod into the slot on the front band hinge plate as shown in Figure 2. Tighten
the clamp screw knob to secure the pail into the saddle.
4. Crank the cable winch to lift pail clear of floor. Disengage floor lock. Roll to
dispensing location.
5. Crank cable winch to raise pail to desired pouring height. Engage the screw-
down floor lock. Tilt the pail forward until desired pouring angle. The pail will
remain in this position.
6. When dispensing is complete, tilt pail back to upright position. Disengage the
floor lock and lower the pail to transporting height; about 6” off the floor.
7. Push the unit to the pail storage area and lower to the floor. Engage the floor
lock. Loosen the clamp screw knob until it can be released from the slot in the
front band hinge plate. Roll Pail Handler away from pail.
Maintenance
Periodic inspection for the general condition of structural and
mechanical components is imperative for safe and efficient
operation.
Periodically inspect all moving parts, framework, and contact areas
for signs of wear, fatigue, or loosening. Tighten, adjust, or replace
parts as necessary to prevent failure and maintain proper function.
Periodically lubricate vertical track rollers, casters, wheels, saddle
shafts, and cable pulleys and/or shafts.
Figure 1
Figure 2