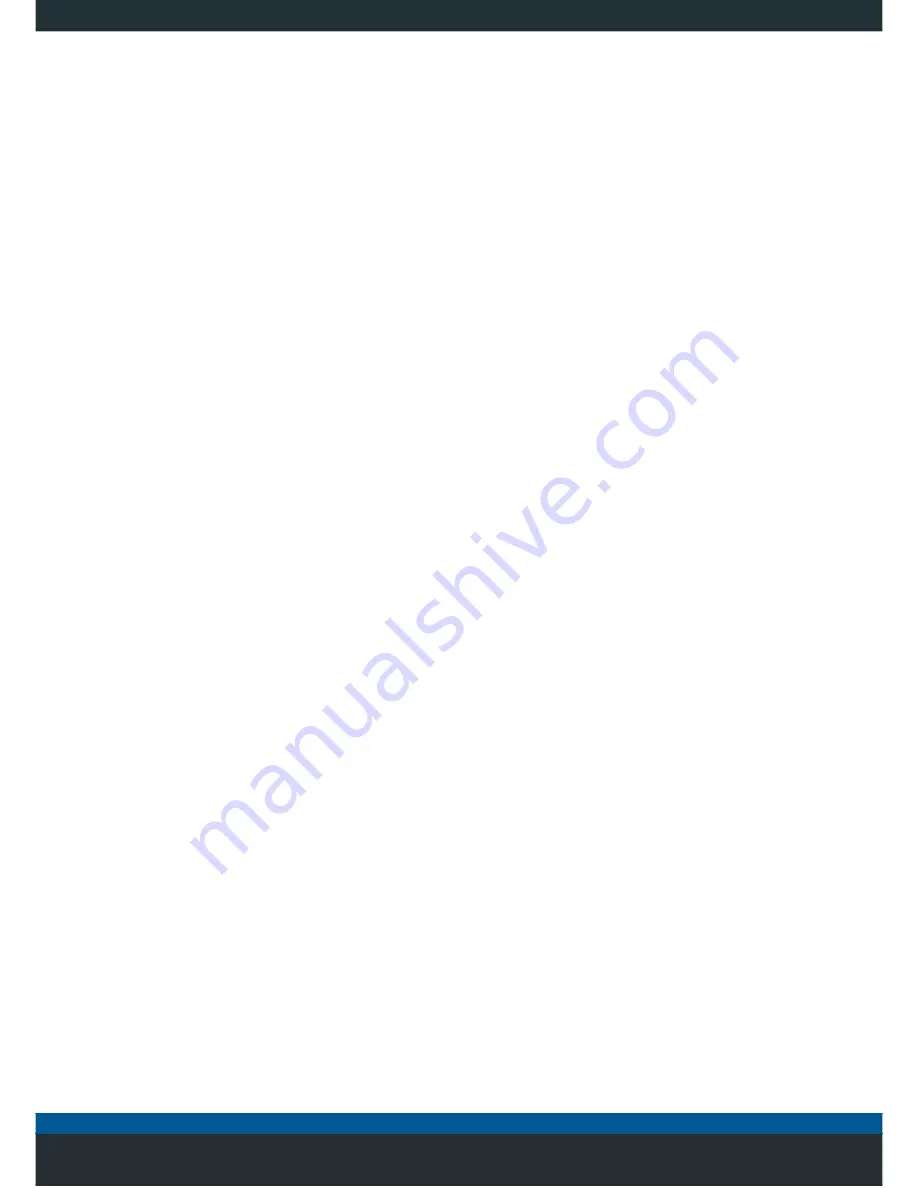
9
2 Safety
2.1 Introduction
This chapter gives an overview of all important safety
aspects to protect personnel, for safe and trouble-free use
of the product from installation through to disposal.
• Failure to comply with the instructions and safety
instructions set out in this manual can lead to
significant risks of personal injury or damage to the
product.
• The product has been designed based on the state-of-
the-art and recognised technical safety guidelines and
standards. The product is safe to use.
2.2 Intended use
• The Motec MVS System is a driver assistance system
can only be operated with a its system limits.
• The device provides the driver with a 270°/360° all-
round view from a bird's-eye perspective. Images
provided by the wide angle cameras that are installed
on both sides, the front and rear of the
vehicle/machinery capture the surroundings.
In order to obtain the desired images, the MVS System
must be installed and operated compliant with these
operating instructions.
The driver/operator shall be responsible for the safe
operation of the vehicle at all times. This obligation
applies in particular if personnel remain in the danger
zone of the vehicle/machinery.
2.3 Non-intended use
Any use of other than that described in the
Chapter"Intended use" on page 9and any use beyond that
shall be deemed non-intended.
• The manufacturer accepts no liability for damage
caused as a result. The risk is borne solely by the
user/operating company.
• It is prohibited to change the system in any shape or
form.
• It is prohibited to operate the system by bypassing the
safety devices.
• It is prohibited to use components which are defect and
therefore jeopardise the safety of the system!
• The Motec MVS is not suitable for the protection of
persons in the sense of the applicable standards and
guidelines for machines and vehicles (Machinery
Directive 2006/42 / EU, DIN EN ISO 13849 and ISO
26262).
2.4 Predictable misuse
The following points describe predictable misuse of the
product:
• Work or operation carried out by unskilled or
insufficiently skilled personnel.
• Improper installation.
• Failure to comply with operational data and
maintenance intervals.
• Operation without or with damaged components, which
are intended for the safety of the persons and the
system.