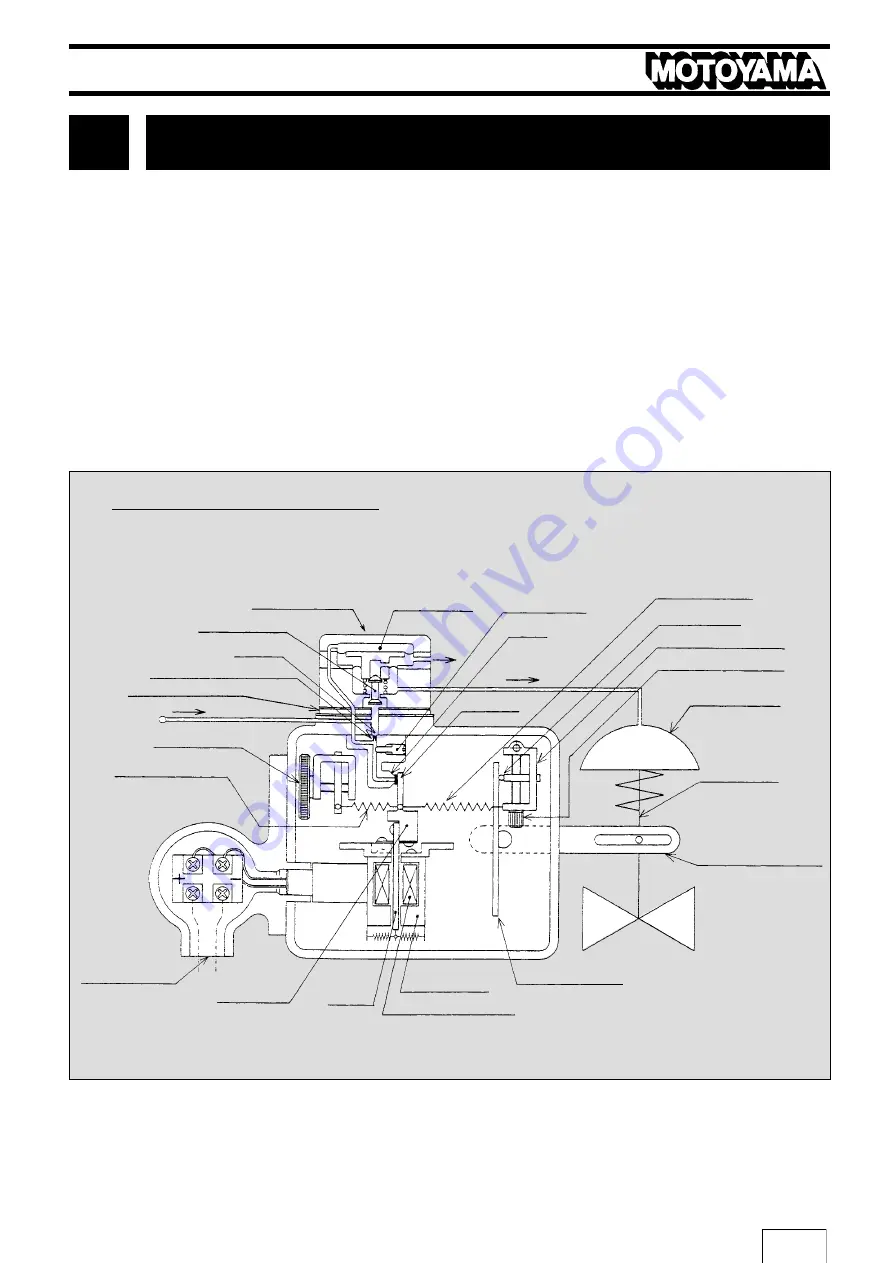
7
Model EA91A&EA90A
PRINCIPLE 0F OPERATION
3
Auto/Manual
Switching Screw
Nozzle
Back Pressure
Pilot Valve
Figure of Principle of Operation
Inner Valve
Filter
Restriction
Orifice Plate
Supply Press.
Zero Adjustment Knob
Zero Adjustment Spring
Conduit Connection
Balancer
Armature
Torque Motor
Transmission Lever
Torque Motor Coil
Nozzle
Output
Exhaust
Flapper
Stroke Adjustment Knob
Actuator
Valve Stem
Stroke Adjustment Lever
Transmission
Feedback Lever
The Model EA91A and EA90A Electro-Pneumatic Positioner is used as accessory measuring instrument to
pneumatic control valves. This converts electric signals from the controller into pneumatic pressure to position
the opening of pneumatic control valve.
As the signal current from the controller or manual operator increases, the torque motor coil generates magnetic
pole on the armature. The armature receives rotary torque in the counter-clockwise direction, and varies the
distance between the nozzle and the flapper. As a result, the nozzle back pressure changes, and the pilot
valve reacts accordingly.
The output air of pilot valve is supplied to the diaphragm motor, and moves the control valve. The valve stem
movement is mechanically transmitted to the feedback spring through feedback lever, transmission lever, and
stroke adjustment lever, and balances the valve movement at a position that is equal to the generated torque due
to the signal current.
Feedback Spring