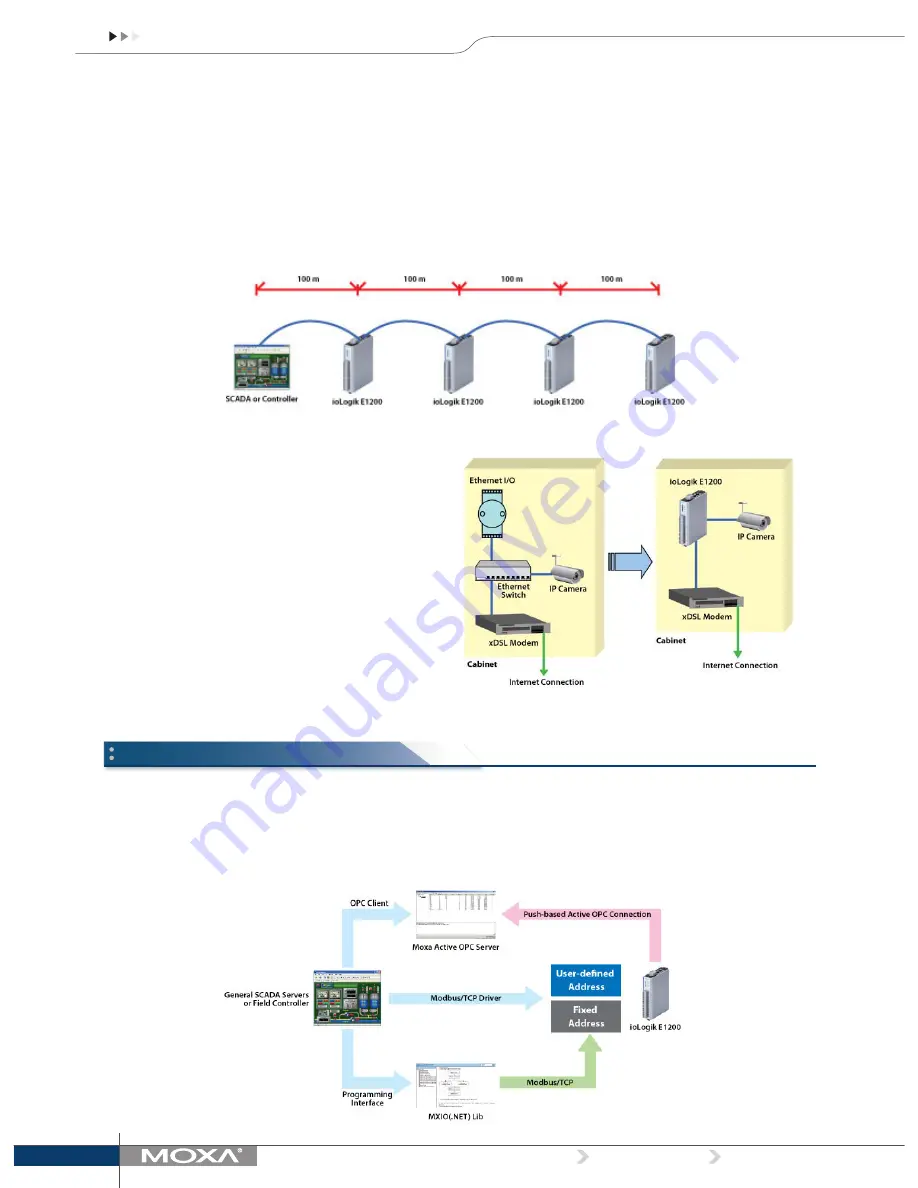
2
w w w. m o x a . c o m
i n f o @ m o x a . c o m
Industrial I/O
Efficient Ethernet Device Connectivity
The ioLogik E1200’s built-in Ethernet switch ports can be cascaded
to other Ethernet devices at the same location. A typical situation is a
remote site that has a few sensors, devices, and Internet connectivity.
Take a roadside cabinet as an example. The IP camera monitors
activity on the street and an Ethernet I/O device handles environmental
monitoring, intrusion, and alarms, and triggers the camera to take
snapshots when needed.
The traditional approach for this kind of remote monitoring application
requires an additional switch or hub for connecting the Ethernet I/O
device to the IP camera. A better approach is to connect another
Ethernet device such as a PLC controller or an IPC in the same cabinet
and use the industrial switch embedded in the ioLogik E1200. Not only
does this solution reduce the number of failure points associated with
an additional switch or hub, but it also reduces the amount of wiring
needed for power, signals, and the network. Space inside the cabinet
can also be saved.
Daisy-chained Ethernet I/O Connection
A new daisy-chained Ethernet I/O concept is now available. The ioLogik
E1200 industrial remote Ethernet I/O has two embedded Ethernet
switch ports that allow information to flow to another local Ethernet
device or connect to the next ioLogik in the daisy-chain. Applications
such as factory automation, security and surveillance systems, and
tunnel monitoring, can make use of daisy-chained Ethernet for building
multi-drop I/O networks over standard Ethernet cables. Many industrial
automation users are familiar with the multi-drop configuration
typically used in fieldbus applications. The daisy-chain function on the
remote Ethernet I/O ioLogik E1200 not only increases the connection
between machines and panels, but also lowers the cost of buying
separate Ethernet switches, and at the same time reduces labor fees
and cabling by a large percentage. For example, if a production facility
contains 700 stations (20 points per station), the wiring cost reduction
can reach 15% of the total implementation cost.
Several approaches are available for controlling the ioLogik E1200
over an Ethernet network. As a traditional I/O solution, the ioLogik
E1200 allows a central SCADA system or field controller to poll the I/O
channel status via the standard, open Modbus/TCP protocol. Except
for the default fixed Modbus/TCP address, the ioLogik E1200 provides
the capability of letting users define the address by themselves. In
Smart I/O Connectivity
addition, the MXIO(.NET) library makes it easy for programmers to
integrate their own software to the ioLogik in the field. Moreover, the
ioLogik E1200 can leverage the benefits of the active technology of
the ioLogik E2000 series with the free Active OPC Server package to
seamlessly connect to any Windows-based SCADA system.