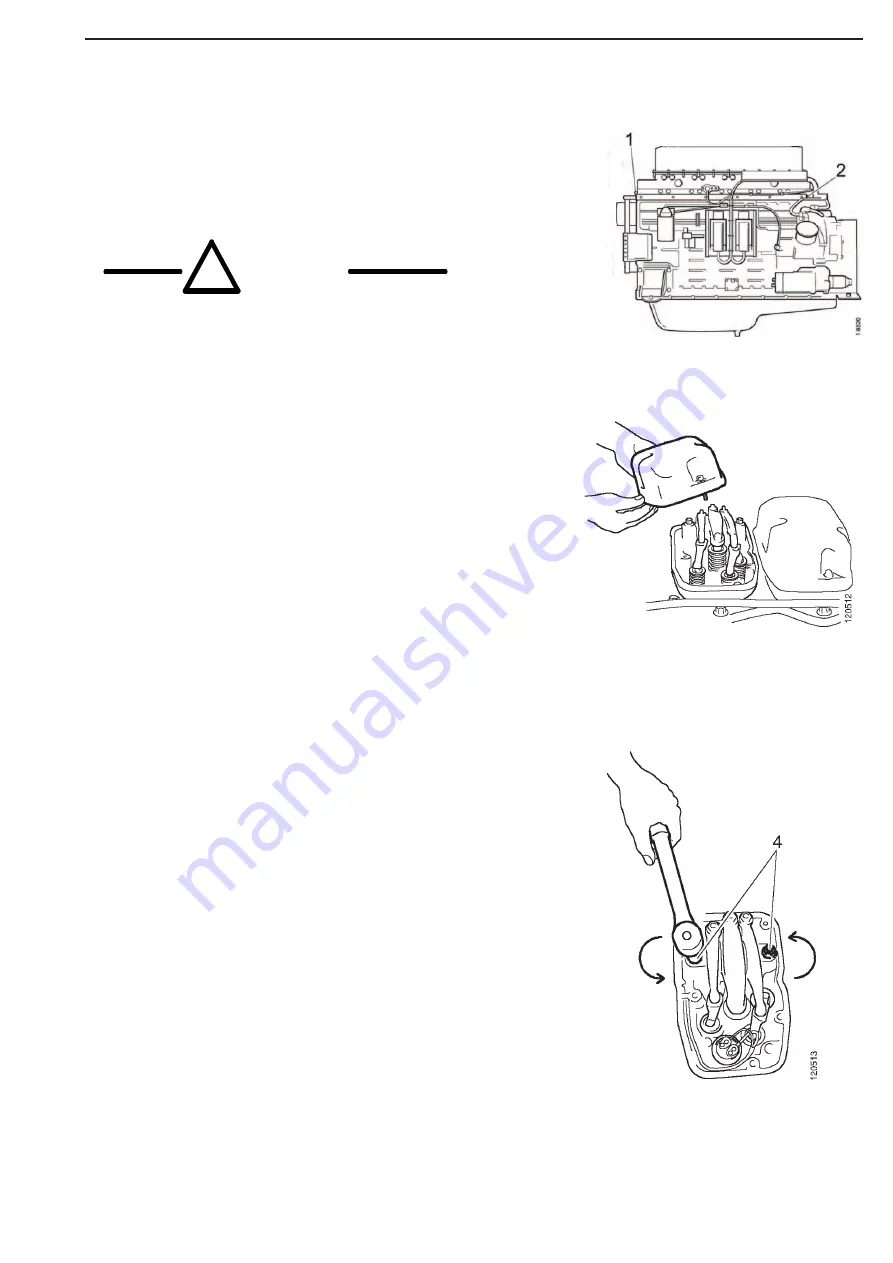
Engine
SHOP MANUAL MT26-31 - 06.2005
Tier-3 710655-
Ch 1
page
47
1.
Open the bleeder nipple and drain the fuel
system by undoing the banjo screw on the
back of the fuel manifold.
The fuel system must be empty or fuel
may run down into the cylinders, which
will result in a great risk of liquid
hammering. If fuel runs into the
combustion chamber, it must be removed
immediately using a pump.
.
Clean the rocker cover and the surrounding
area.
3.
Remove the top part of the rocker cover.
4.
Relieve the pressure on the valves by
undoing the bolts on the rocker arm shaft
alternately.
WARNING!
!
1. Bleeder nipple
. Banjo screw
Summary of Contents for MT 26
Page 1: ...Engine SHOP MANUAL MT26 31 06 2005 Tier 3 710655 Ch 1 page Chapter 1 Engine...
Page 30: ...SHOP MANUAL MT26 31 06 2005 Engine Tier 3 710655 Ch 1 page 30...
Page 95: ...Engine SHOP MANUAL MT26 31 06 2005 Tier 3 710655 Ch 1 page 95...
Page 168: ...SHOP MANUAL MT26 31 06 2005 Engine Tier 3 710655 Ch 1 page 168...
Page 169: ...Engine SHOP MANUAL MT26 31 06 2005 Tier 3 710655 Ch 1 page 169 Note...
Page 170: ...SHOP MANUAL MT26 31 06 2005 Engine Tier 3 710655 Ch 1 page 170 Note...