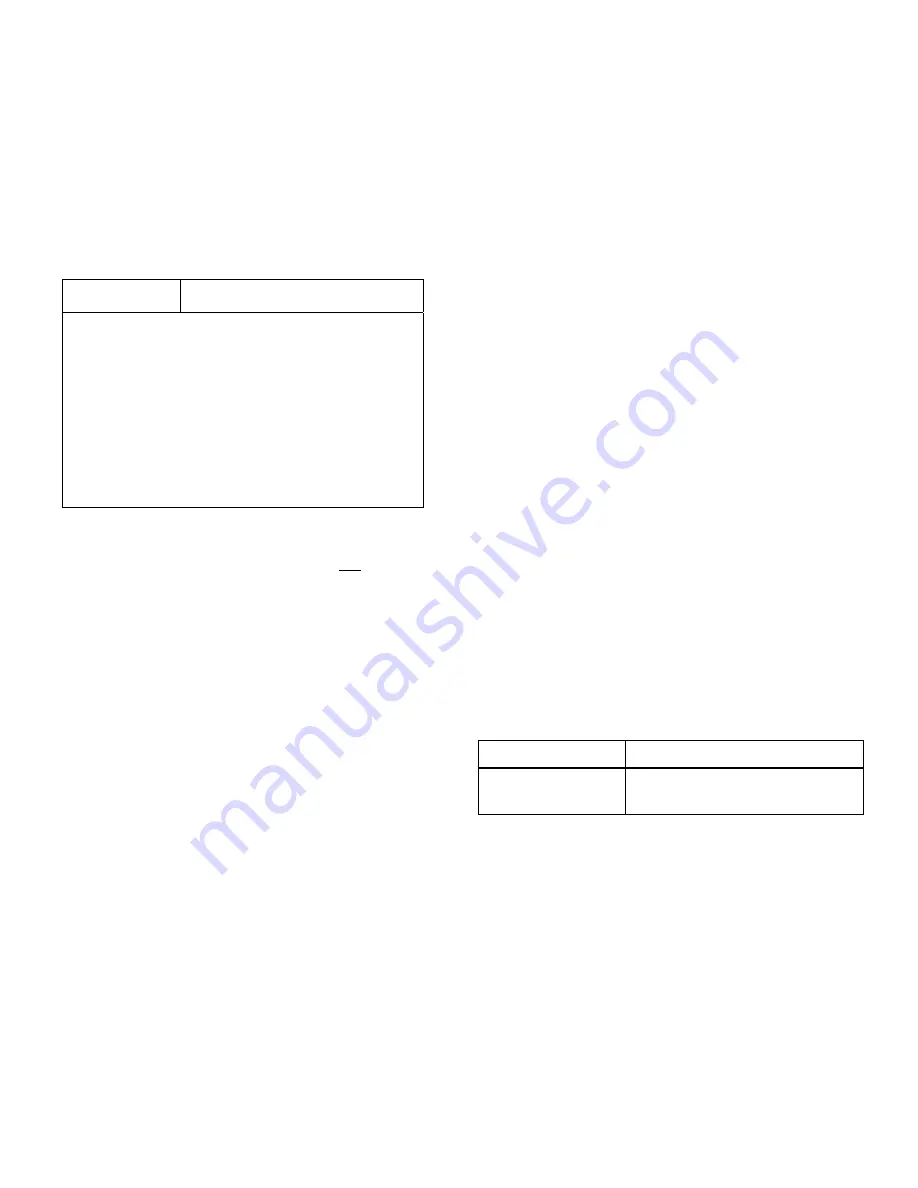
Page 8
4-28. Seals.
It is sound practice to always replace grease
seals (1 and 9, fig. 4-7) whenever drive shaft and tapered
roller bearings are removed.
4-29. Packing.
It is sound practice to always replace pack-
ing whenever the pump bearing housing or G3 bearing re-
tainers are disassembled.
4-30. Rotor.
1. To check for excessive wear of rotor (37, fig. 4-7),
measure the rotor crest-to-crest diameter (see fig. 4-4) and
compare with the following chart:
Rotor
Capacity
Standard
*Crest to Crest Dia. (inches)
008
2.772 + .000/—.004
012
2.676 + .000/—.004
022
3.425 + .000/—.004
036
4.015 + .000/—.004
050
4.015 + .000/—.004
065
4.906 + .000/—.004
090
4.906 + .000/—.004
115
5.709 + .000/—.004
175
6.584 + .000/—.004
335
5.800 + .000/—.005
345
7.260 + .000/—.004
620
7.128 + .000/—.005
800
9.068 + .000/—.004
*These dimensions are applicable for AAA trim codes only.
Note: The rotor is designated by the third, fourth and fifth
numbers in the Model Number, La., 2G
065
G2.
2. If the measured crest to crest diameter is within 0.010
inch of the standard value and is free of deep nicks, gouges,
or other surface defects, the rotor is re-usable.
3. Rotors with crest to crest values 0.011 to 0.050 inch
under the standard values should be replaced. These rotors
can be renewed by chrome plating to standard dimensions
provided that:
a. The key slots are not excessively worn.
b. The rotor surface is not cracked, pitted or deeply
grooved (1/32 inch or more).
c. The base surface metal is not pitted or corroded.
4. Rotors may be sent to Moyno or any other competent
plating shop. Rotors should be stripped and replated to
standard dimensions, then buffed.
4-31. Stator.
A worn stator may appear pitted and gouged,
or may appear smooth similar to when new. Performance is
the best measure of rotor to stator fit. If unable to measure
performance adequately, suspected stator wear can be
evaluated by a Moyno sales or factory representative.
4-32. All Other Parts.
Check for cracks, excessive wear,
damage to threaded holes, burrs, etc. Replace as neces-
sary. Replace O-rings and all gaskets at each disassembly
and reassembly.
4-33. ASSEMBLY OF G2 OPEN THROAT PUMP
Note: In the following G2 assembly instructions, the part
reference numbers are from fig. 4-7.
The Moyno 2000 pumps are reassembled in the
reverse order of dismantling. The following suggestions
are offered:
1. While pump is dismantled, check all gaskets, seals,
packing, and O-rings. Replace all worn items. It is rec-
ommended that the gear joint seals (32), gear joint O-rings
(24, 38) and stator O-ring (20) be replaced each time either
of the gear ioints is disassembled.
2. During the assembly process, cleanliness is impor-
tant. To avoid premature failure, bearings and gear joint
components must be handled with care and kept clean.
4-34. Lubrication During Assembly
Note:
The bearings are lubricated at the factory, and will
only need to be re-lubricated when the shaft/bear-
ing assembly is completely removed from pump.
1. Bearings.
Pack bearings after installation on
shaft (Section 4-37). Lubricant should be packed around
all of the rollers and should completely cover the faces
of the races. The void inside the spacer between
the bearings should be filled approximately half
way with lubricant.
2. Gear Joints.
Both gear joints should be packed with
lubricant during assembly (Sections 4-39 and 4-40). DO
NOT use zerk fittings to lubricate gear joints after assembly.
The pipe plugs (C) in the gear joint shells are vent plugs and
MUST BE REMOVED during assembly of the gear joints to
allow excess lubricant to vent from the gear joints.
3. Packing.
Lubricate packing rings during assembly.
Additional grease can be added after assembly through
the zerk fittings installed in the side of the stuffing box.
4. Approved lubricants:
CAUTION: Do not mix different brands of lubricants for
the same application.
Area to Lubricate
Approved Lubricant or Equivalent
Bearings, Gear Joints
& Packing
ACG-2
(Dubois Chemical, Inc.)
4-35. Packing Installation
1. The standard packing set (10) consists of six braided
packing rings and two teflon lantern ring halves (13).
2. Install packing and lantern ring halves into the stuffing
box area of the suction housing (19) in the following se-
quence:
a. Wipe a film of lubricant on each packing ring and
install three rings. Push each ring firmly in place.
Note: Install the packing rings with the splits staggered at 90
degrees to the adjacent ring of packing. On initial as-
sembly, one ring of packing may not fit in stuffing box.
This final ring of packing should be installed after
pump is started and packing is seated.
Summary of Contents for Version 3
Page 1: ......
Page 19: ...Page 16 4 60 PARTS LIST FOR G2 OPEN THROAT Table 4 1 G2 Parts List ...
Page 20: ...Page 17 FOLD OUT FOR EXPLODED VIEW OF PUMP Notes ...
Page 21: ...Page 18 ...
Page 22: ...Page 19 Figure 4 7 G2 open throat pump exploded view ...
Page 26: ...Page 23 Figure 4 10 G3 bridge breaker exploded view ...
Page 28: ...Page 25 ...