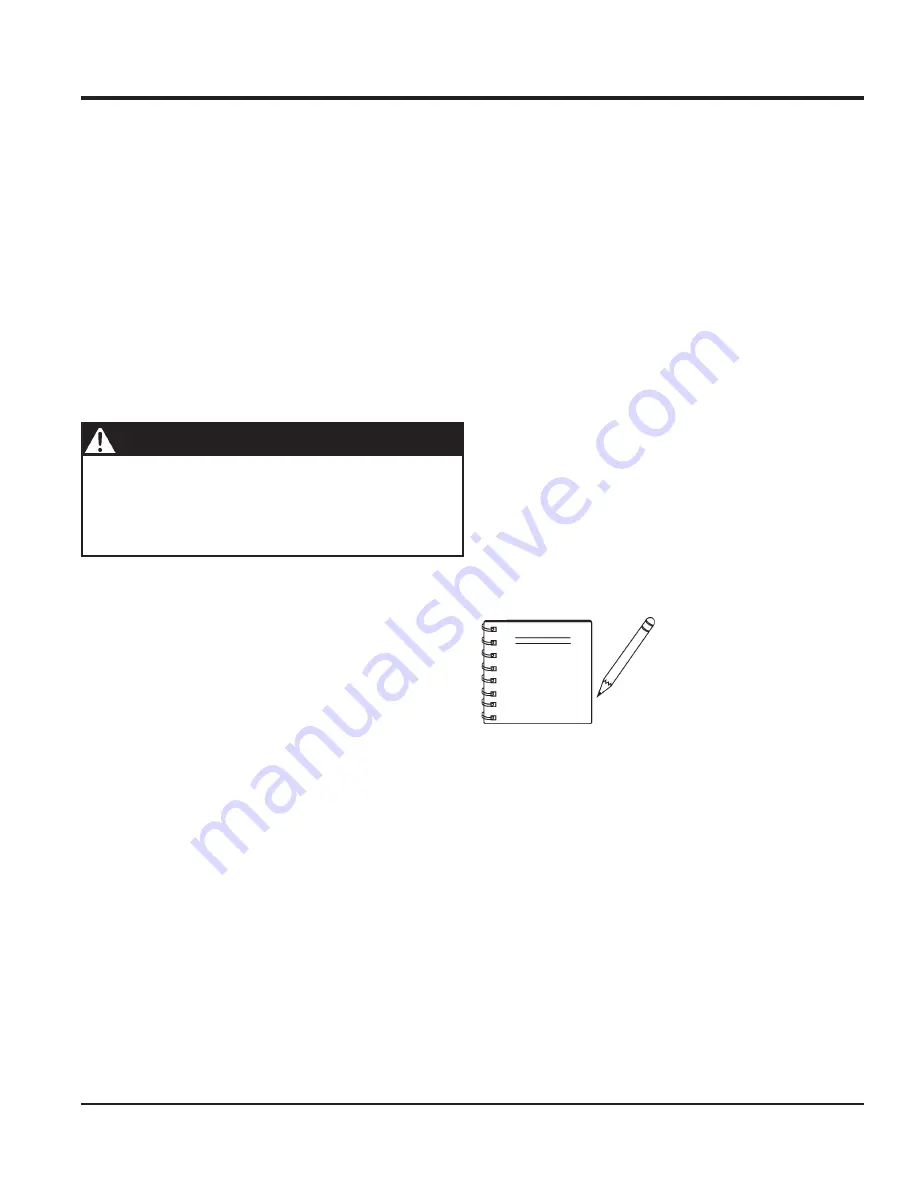
DCA-180SSJU — OPERATION AND PARTS MANUAL — REV. #3 (02/01/10) — PAGE 17
1
Outdoor Installation
Install the generator in a area that is free of debris,
bystanders, and overhead obstructions. Make sure the
generator is on secure level ground so that it cannot slide or
shift around. Also install the generator in a manner so that
the exhaust will not be discharged in the direction of nearby
homes.
The installation site must be relatively free from moisture
and dust. All electrical equipment should be protected from
excessive moisture. Failure to do will result in deterioration
of the insulation and will result in short circuits and grounding.
Foreign materials such as dust, sand, lint and abrasive
materials have a tendency to cause excessive wear to
engine and alternator parts.
Generator Grounding
To guard against electrical shock and possible damage to
the equipment, it is important to provide a good
EARTH
ground.
Article 250 (Grounding) of the National Electrical Code (NEC)
provides guide lines for proper grounding and specifies that
the cable ground shall be connected to the grounding system
of the building as close to the point of cable entry as practical.
NEC articles 250-64(b) and 250-66 set the following
grounding requirements:
1. Use one of the following wire types to connect the
generator to earth ground.
a. Copper - 10 AWG (5.3 mm
2
) or larger.
b. Aluminum - 8 AWG (8.4 mm
2
) or larger.
2. When grounding the generator (Figure 4) connect the
ground cable between the lock washer and the nut on
the generator and tighten the nut fully. Connect the other
end of the ground cable to earth ground.
3. NEC article 250-52(c) specifies that the earth ground
rod should be buried a minimum of 8 ft. into the ground.
When connecting the generator
to any buildings electrical
system
ALWAYS
consult with
a licensed electrician.
INSTALLATION
NOTE
Indoor Installation
Exhaust gases from diesel engines are extremely poisonous.
Whenever an engine is installed indoors the exhaust fumes
must be vented to the outside. The engine should be installed
at least two feet from any outside wall. Using an exhaust
pipe which is too long or too small can cause excessive back
pressure which will cause the engine to heat excessively
and possibly burn the valves.
Mounting
The generator must be mounted on a solid foundation (such
as concrete) and set firmly on the foundation to isolate
vibration of the generator when it is running. The generator
must set at least 6 inches above the floor or grade level (in
accordance to NFPA 110, Chapter 5-4.1).
DO NOT
remove
the metal skids on the bottom of the generator. They are to
resist damage to the bottom of the generator and to maintain
alignment.
Pay close attention to ventilation when operating the
generator inside tunnels and caves. The engine exhaust
contains noxious elements. Engine exhaust must be routed
to a ventilated area.
CAUTION - EXHAUST HAZARD
Summary of Contents for DCA180SSJU WHISPERWATT SERIES
Page 2: ...PAGE 2 DCA 180SSJU OPERATION AND PARTS MANUAL REV 3 02 01 10 PROPOSITION 65 WARNING ...
Page 69: ...DCA 180SSJU OPERATION AND PARTS MANUAL REV 3 02 01 10 PAGE 69 1 NOTES ...
Page 72: ...PAGE 72 DCA 180SSJU OPERATION AND PARTS MANUAL REV 3 02 01 10 GENERATOR ASSY GENERATOR ASSY ...
Page 88: ...PAGE 88 DCA 180SSJU OPERATION AND PARTS MANUAL REV 3 02 01 10 BATTERY ASSY BATTERY ASSY ...
Page 90: ...PAGE 90 DCA 180SSJU OPERATION AND PARTS MANUAL REV 3 02 01 10 MUFFLER ASSY MUFFLER ASSY ...
Page 92: ...PAGE 92 DCA 180SSJU OPERATION AND PARTS MANUAL REV 3 02 01 10 FUEL TANK ASSY FUEL TANK ASSY ...
Page 105: ...DCA 180SSJU OPERATION AND PARTS MANUAL REV 3 02 01 10 PAGE 105 1 NOTES ...