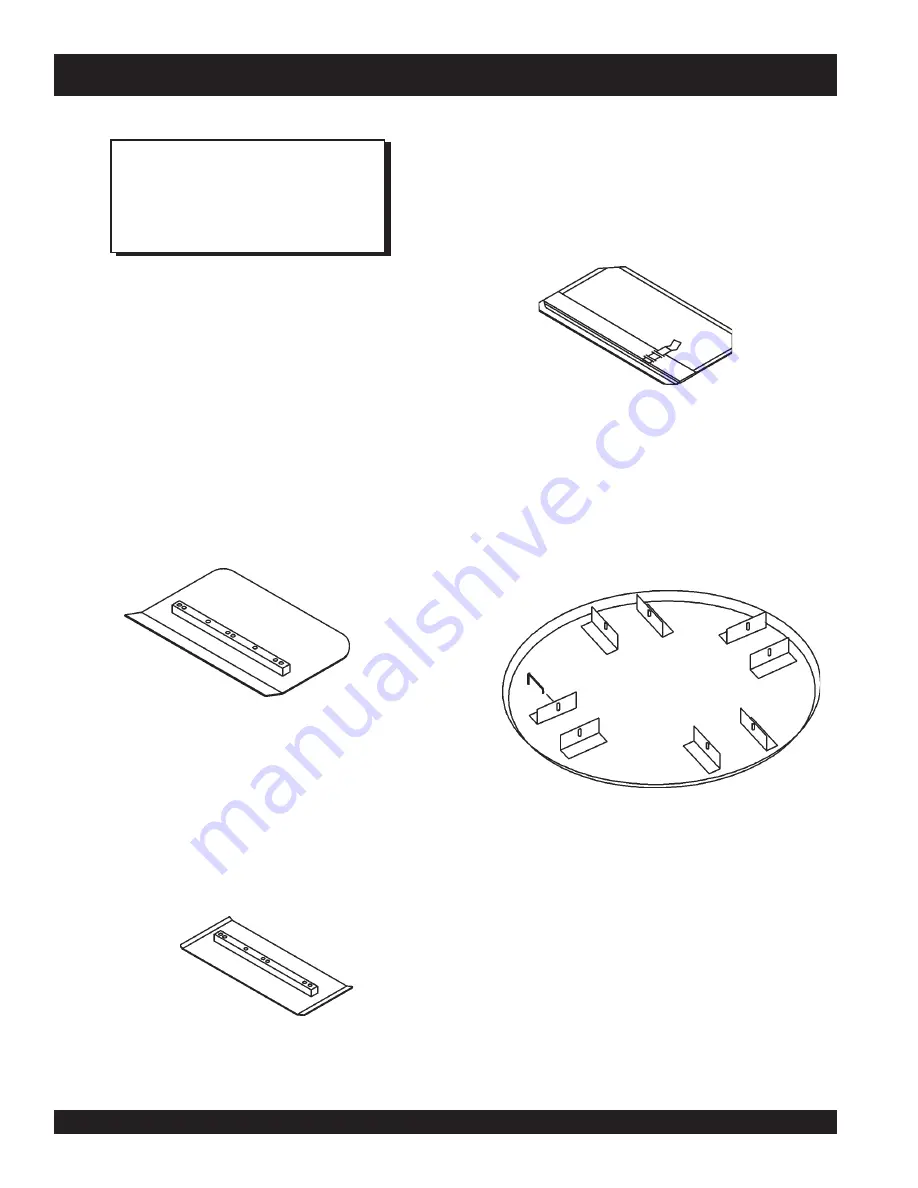
PAGE 28 — BA-SERIES WALK-BEHIND TROWEL— PARTS & OPERATION MANUAL — REV. #3 (11/30/04)
Blades
Blades are a vital part of finishing concrete. This trowel, or
finisher
, has been designed to finish concrete and the blades are
built to stringent quality standards out of the finest trowel steel. If
you need replacement blades, consult your parts list in this
manual for part numbers and order them from your Multiquip parts
dealer or importer.
Combo Blades
This trowel was equipped with combination
float/finish
(Figure
32) blades as original equipment. These blades have been
designed for optimum performance in both the floating and
finishing operations. These blades are versatile and should take
care of most troweling needs.
NOTE
Specification and part number
are subject to change without
notice.
Blades should be changed when they fail to
finish concrete in a satisfactory manner.
BA-SERIES TROWEL — OPTIONS
Float Discs (Optional)
These round discs (Figure 35) attach to the spiders and allow the
machine to “float” on “wet” concrete. The disc design allows early
floating and easy movement from wet to dry areas. They are also
very effective in embedding large aggregates and surface
hardeners.
Clip-On Float Blades (Optional)
These blades will clip (Figure 34) on to an existing installed blade,
allowing your finisher to float on “wet” concrete so that the
troweling operation can begin as early as possible. They are
easily removable, so that after the floating operation, when the
concrete is sufficiently cured, they can be removed to expose the
finish blades for continued troweling.
Figure 33. Finish Blade
Figure 34. Clip-On Float Blade
Figure 35. Float Disk
Finish Blades (Optional)
These blades (Figure 33) have been specifically designed for
finish operations with this trowel. They will provide a premium
surface finishing capability from your trowel. They should only be
used after the concrete has set to the point where the trowel does
not sink into the concrete when placed on it.
Figure 32. Combination Blade
Summary of Contents for BA-SERIES
Page 2: ......