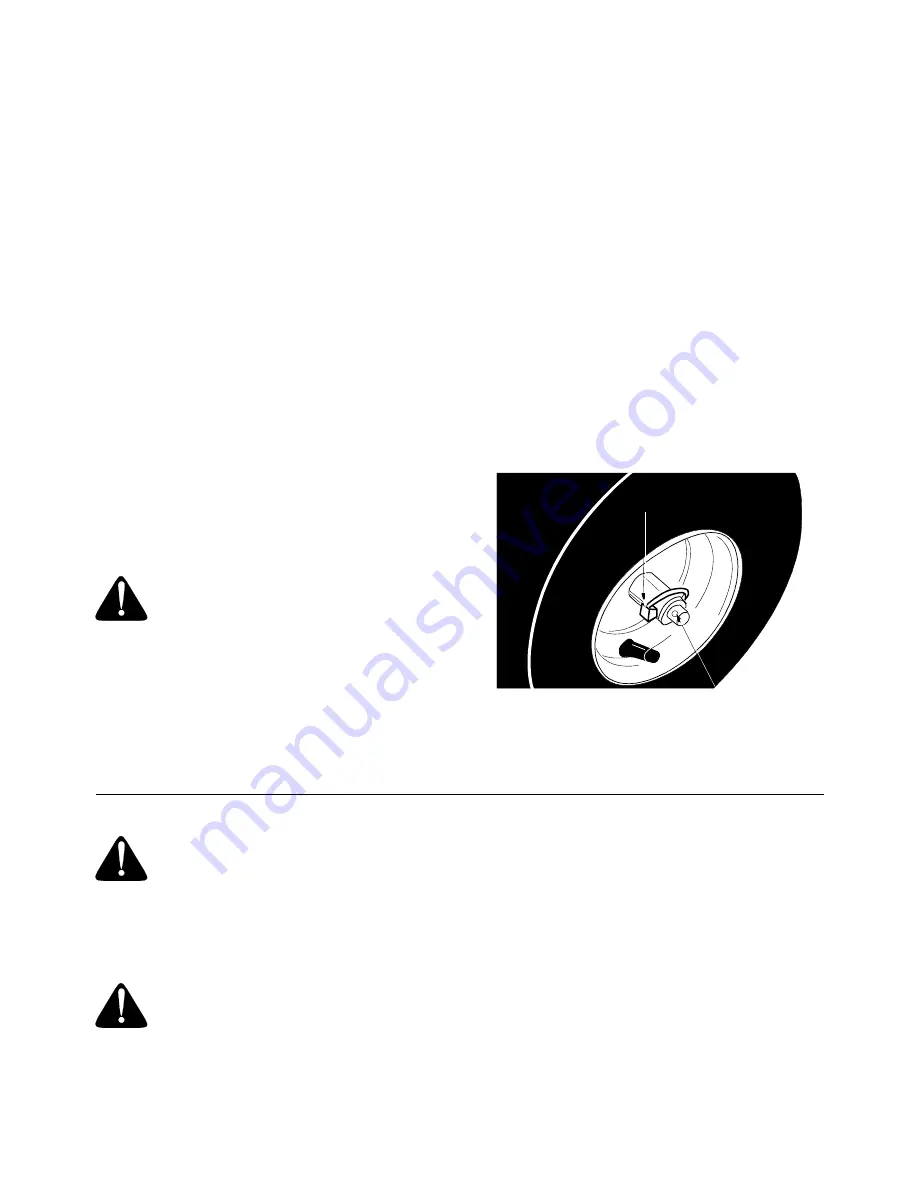
15
ADJUSTING SHIFT ROD
1.
Remove the hairpin clip and flat washer from the
ferrule and remove the ferrule from the shift
lever. Place the shift lever in the fastest forward
speed position.
Models 602, 642, 662:
2.
Push up on the shift arm assembly as far as it
will go. Thread the ferrule up or down the shift
rod and align with the lower hole on the wider
side of the shift lever assembly behind the
handle panel. Secure the ferrule to the shift arm
assembly again with the hardware earlier
removed.
Models 614, 644, 664, and 6A4:
3.
Push down on the shift arm assembly as far as it
will go. Thread the ferrule up or down the shift
rod and align it with the hole closest to the shift
knob on the narrow side of the shift lever
assembly behind the handle panel.
NOTE:
Make certain to check for correct
adjustment of the shift rod as instructed in the Final
Adjustments section before operating the snow
thrower.
CARBURETOR ADJUSTMENT
WARNING:
If any adjustments are
made to the engine while the engine is
running (e.g. carburetor), keep clear of
all moving parts. Be careful of heated
surfaces and muffler.
Minor carburetor adjustment may be required to
compensate for differences in fuel, temperature,
altitude and load.
Refer to the separate engine manual packed with
your unit for carburetor adjustment information.
DRIVE WHEELS
The wheels may be adjusted for two different
methods of operation. The adjustment is made by
placing the klick pins in one of two different holes on
the right side of the unit. See Figure 26.
1.
One Wheel Driving—Place klick pin in the
outside axle hole on the right side. This position
gives power drive to the left wheel only, making
the unit easier to maneuver.
2.
Both Wheels Driving—Place klick pin in the
hole in the hub next to the rim on the right side.
This position is good for heavy snow as there is
power drive in both wheels.
Figure 26
SECTION 9: LUBRICATION
WARNING:
Disconnect the spark plug
wire and ground against the engine
before performing any lubrication or
maintenance.
ENGINE
Refer to engine manual for all engine lubrication
instructions.
WARNING:
When following instruct-
ions in separate engine manual for
draining oil, be sure to protect frame to
avoid oil dripping onto transmission
parts.
CHUTE DIRECTIONAL CONTROL
The gear on the end of the chute directional control
should be greased with multi-purpose automotive
grease once a season.
AUGER SHAFT
At least once a season, remove shear bolts on auger
shaft. Oil or spray lubricant inside shaft. See Figure
27. Also lubricate the auger bearings at least once a
season.
Klick Pin in Hole
in Hub Next to Rim
Outside Hole
in Axle