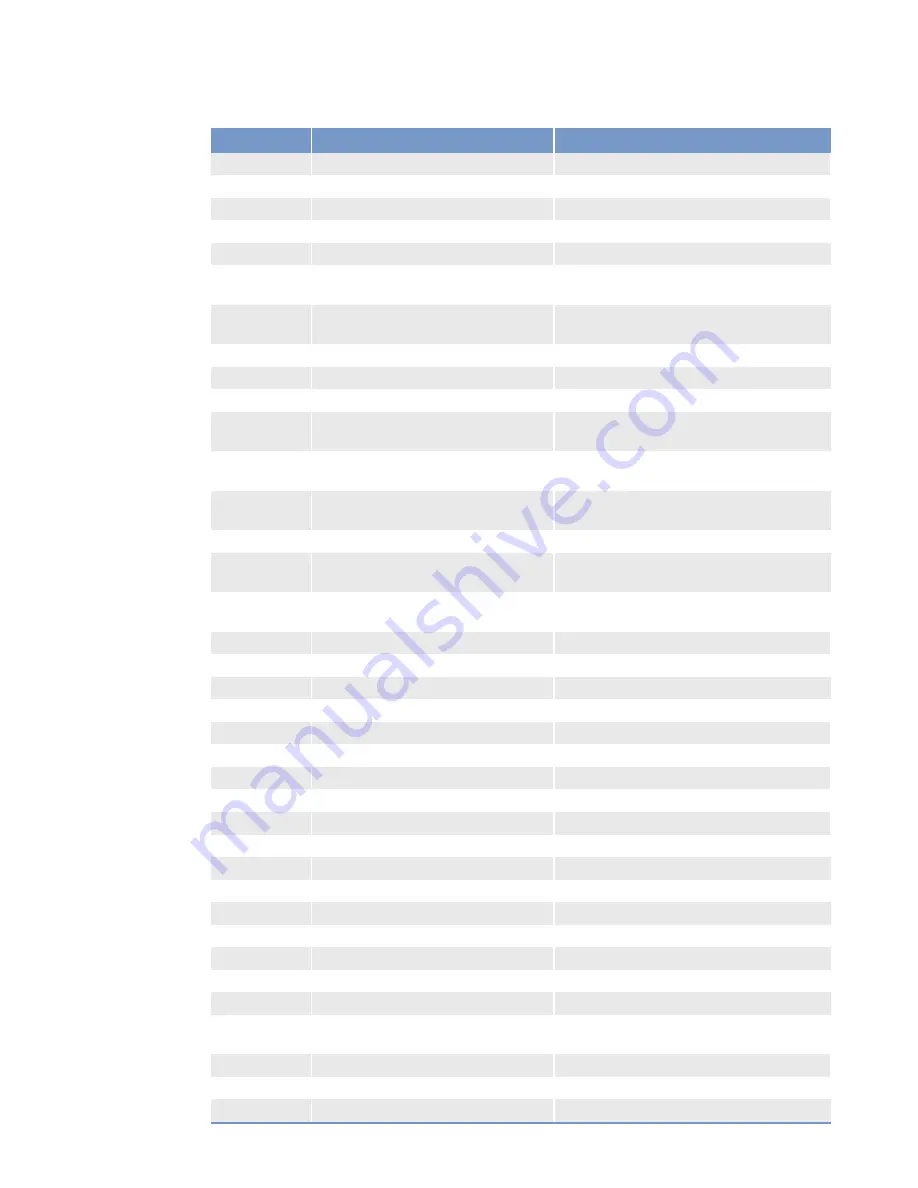
Abbreviation
Meaning
Explanation
FRS
Fuel Restriction Sensor
Fuel differential pressure sensor
FTS
Fuel Temperature Sensor
FWCP
Fire Water Control Panel
Control cabinet for fire extinguishing water
GND
Ground
HD
Hochdruck
High pressure
HI
High
Alarm: Measured value exceeds 1st maximum
limit
HIHI
High High
Alarm: Measured value exceeds 2nd maximum
limit value
HT
Hochtemperatur
High temperature
IDM
Interface Data Module
Memory module for interface data
INJ
Injector
ISO
International Organization for Standardi-
zation
International umbrella organization for all na-
tional standardization institutes
KGS
Kupplungsgegenseite
Engine free end in accordance with DIN ISO
1204
KS
Kupplungsseite
Engine driving end in accordance with DIN ISO
1204
LED
Light Emitting Diode
LO
Low
Alarm: Measured value lower than 1st mini-
mum limit value
LOLO
Low Low
Alarm: Measured value lower than 2nd mini-
mum limit value
LSG
Limiting Speed Governor
Maximum-speed governor
N/A
Not applicable, not available
ND
Niederdruck
Low pressure
NT
Niedertemperatur
Low temperature
OEM
Original Equipment Manufacturer
OI
Optimized Idle
OLS
Oil Level Sensor
OPS
Oil Pressure Sensor
OTS
Oil Temperature Sensor
OT
Oberer Totpunkt
Top Dead Center (TDC)
PAN
Panel
Control panel
PIM
Peripheral Interface Module
PWM
Pulsweitenmodulation
Pulse Width Modulation
P-xyz
Pressure-xyz
Pressure measuring point xyz
RL
Redundancy Lost
Alarm: Redundant CAN bus failure
SAE
Society of Automotive Engineers
U.S. standardization organization
SD
Sensor Defect
Alarm: Sensor failure
SEL
Stop Engine Light
Signal lamp requesting engine stop and elimi-
nation of fault as soon as possible.
SID
System Identifier
SRS
Synchronous Reference Sensor
SS
Safety System
Safety system alarm
MS150100/04E 2015-09
| Appendix A | 143
TIM-ID: 0000035533 - 006