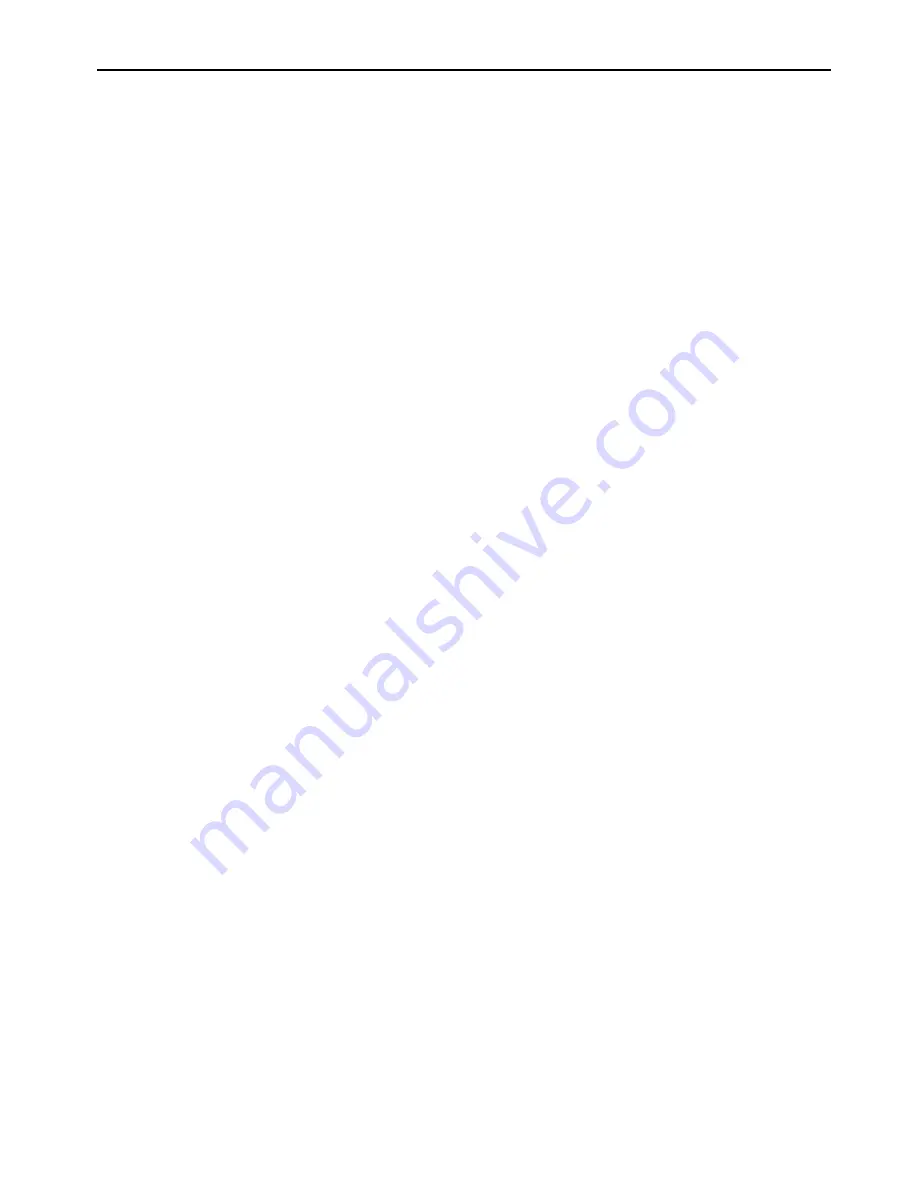
MTZ 1220.1/1220.3 K. Scheduled technical maintenance
K2
Maintenance after running-in (30 service hours)
1. Inspect and wash the tractor.
2. Listen how all components of the trac-
tor operate.
3. Check tightening of the cylinder head
fastening bolts (Operation 35).
4. Check clearance between valves and
rockers (Operation 22).
5. Clean the impellers of the engine
centrifuge of gear box (Operation 13).
Clean the GB strainer (Operation 15).
6. Check the generator belt tension (Op-
eration 8).
7. Discharge sediment from fuel tanks,
coarse and fine filters of the engine
(Operations 7, 18).
8. Check and, if necessary, adjust the
clutch, brake pedal free travel and the
air system (Operations 24, 26).
9. Check condition of the batteries, clean
the terminal connections and vent
holes (Operation 27).
10. Change the oil in:
• diesel engine crankcase (Operation
16),
• power train housings (Operation
41),
• wheel reduction gears and FDA fi-
nal drive (Operation 41).
11. Replace the paper filter elements of
the engine and hydraulic system filters
(Operations 17, 30).
12. Lubricate the clutch release yoke
bearing (Operation 19).
13. Discharge condensate from pneumatic
system receivers (Operation 5).
14. Check and as necessary tighten the
external threaded connections (Opera-
tion 39).
15.
Check operation of the engine,
steering, brakes, controls, illumination and
signaling systems (Operation 6).
16. Lubricate the bearings of swivel pin of
FDA wheel reduction gear (Operation
10).
17. Check toe-in of front wheels (Opera-
tion 33).
18. Lubricate the pivots of the steering cy-
linders (Operation 9).
Summary of Contents for 1220.1
Page 1: ...MTZ 1220 1 1220 3 1220 1 0000010 OM OPERATOR S MANUAL 2010...
Page 161: ...MTZ 1220 1 1220 3 Section I Coupling of implements I15...
Page 232: ......
Page 236: ......
Page 241: ......
Page 243: ......