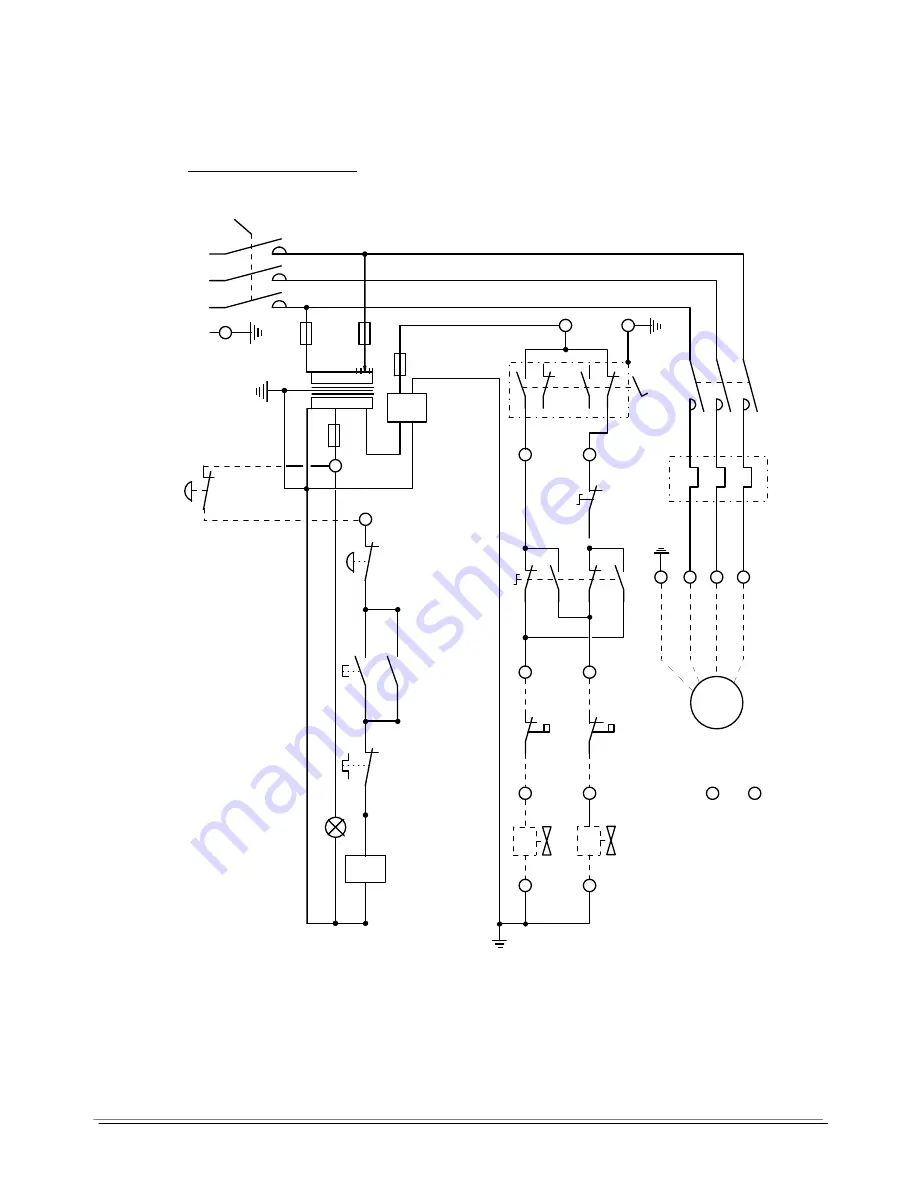
BULLDOG 65 Hydraulic Steelworker
38
10.2
10.2
10.2
10.2
E
E
E
E
LECT
LECT
LECT
LECTRICAL
RICAL
RICAL
RICAL
C
C
C
C
IRCUIT
IRCUIT
IRCUIT
IRCUIT
5
3
6
4
1
2
KM1
E
#1
#2
1
F4
V
W
U
4
E
3
1
3
2
2
2
4
5
2
4
1
3
1
#3
F3
2A
24v
DC
+ -
20V
F3
2A
24V
F1
5A
F2
5A
1
9
10
2
KM1
13
3
2
1
12
11
7
6
B
8
A
8
14
96
95
F4
4
KM1
STOP
START
REMOTE
STOP
PUNCH
NOTCH
NORMAL /
INCH
PUNCH
DOWN
LIMIT
SWITCH
PUNCH
UP
LIMIT
SWITCH
NEON
SOLENOID
VALVES
SPARE
TERMINALS
FOOT
SWITCH