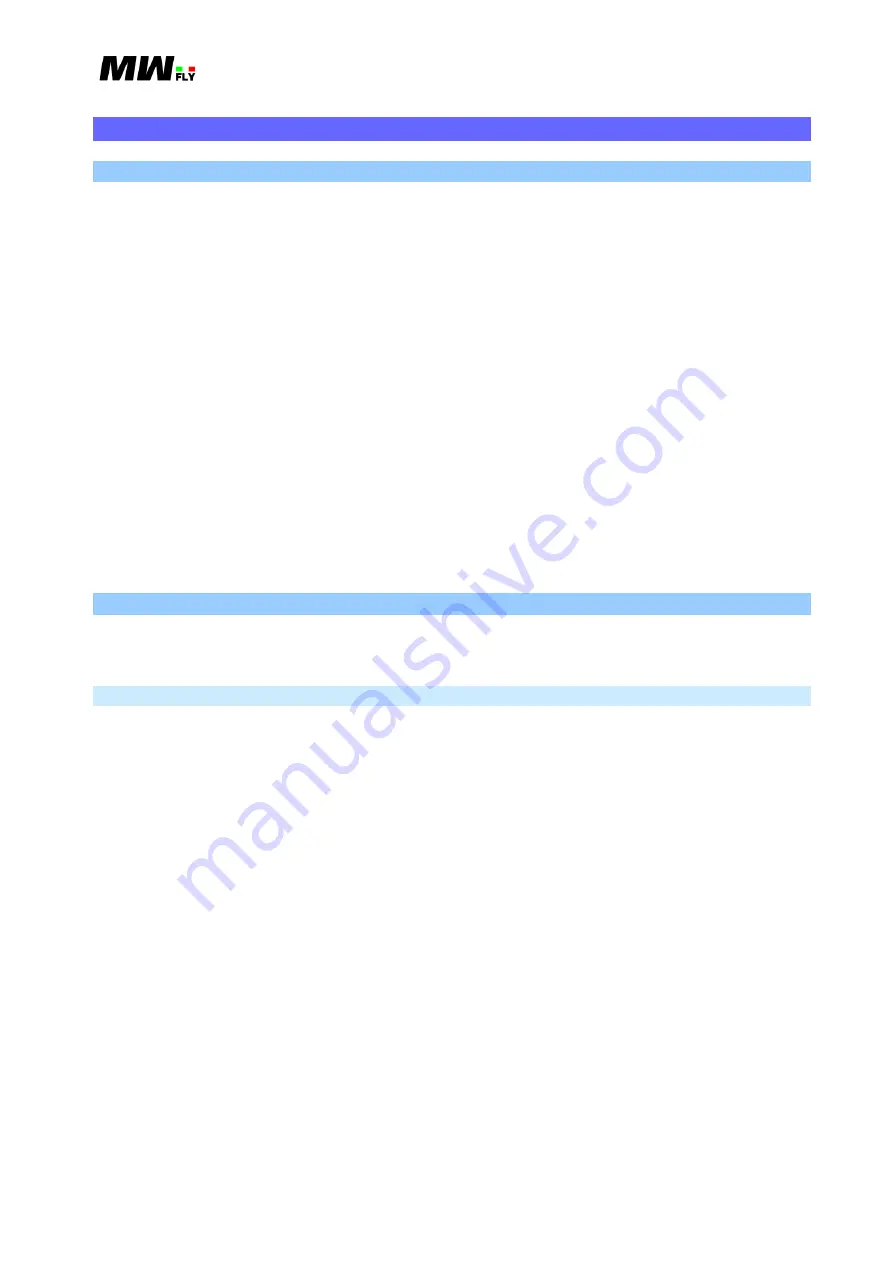
Applicable to: B22 and B25 (a ll versions)
Revision 1.3 – 02/24/ 2015
Manual B – Operations
-
10
B.3. SAFETY
B.3.1. Statement
Just by reading this manual will not eliminate the hazards connected to the installation and use of
the engine. However the understanding and application of the information herein is essential for a
proper and safe use of the engine.
The information, components, system descriptions, pictures, tables and technical data contained in
the present manual are correct at the time of publication. MW Fly, however, maintains a policy of
continuous improvement of its products without imposing upon itself any obligation to install
them on its products previously manufactured.
The onus to install MW Fly B22 engine is at the sole discretion and responsibility of the Original
Manufacturer, Home Builder or Aircraft Owner. MW Fly cannot assume responsibility for a
successful installation in a specific airframe due to the variety of designs existing in the market.
For this reasons MW Fly declines responsibility regarding damage to engine parts, accessories or
aircraft structure during the installation and use of this engine. The owner accepts the
responsibility and the risk in using this engine.
MW Fly reserves the right at any time to discontinue or change specifications, designs, features,
models or equipment without incurring obligation
.
It is forbidden to copy any part of the present
manual without authorization from MW Fly.
B.3.2. Safety Elements
It very important to understand all the safety aspects and to distinguish the two different safety
types; active and passive.
B.3.2.1. Passive Safety
Passive safety concerns the engine design and the engine installation criteria. The following is a
list of the main engine features designed to increase passive safety.
CRANK SHAFT ON BALL BEARINGS: This reduces the risk of engine stoppage in case of
lubricant system default or oil leakage. Moreover, unexpected wearing of the bearings is easy
to identify because it is characterized by a clear increase in noise on the lower side of the
crank case. Plain bearings do not provide any clear signa l in case of unexpected wearing.
MONOLITIC CONNECTING ROD: This reduces the risk of the default of the crank that is
often connected to the wrong installation of the rod cup.
MACHINED PISTON: This increases the safety by avoiding the risk of deformation due to
intrusion in the fusion, press residual stress, and use of low thermal dilatation coefficient
alloy.
SINGLE OVER HEAD CAMSHAFT (SOHC): By using this it is not necessary to adopt
hydraulic tappets (that are necessary with a push rod system) and it a voids the risk of breaking
the valve in case of a drop in oil pressure. Moreover, the use of SOHC reduces the dynamic
load on the timing command thereby reducing the friction and the wear of the timing
mechanical parts.
REDUCTION GEAR BOX WITH SEPARATE LUBRICATION: The use a specific oil for
the reduction gear box increases the reliability and reduces the risk of a fatigue fracture and
pitting wear of the teeth.
MONOLITIC PROPELLER SHAFT: This reduces the risk of a fatigue fracture of the
propeller shaft and also increases its strength.