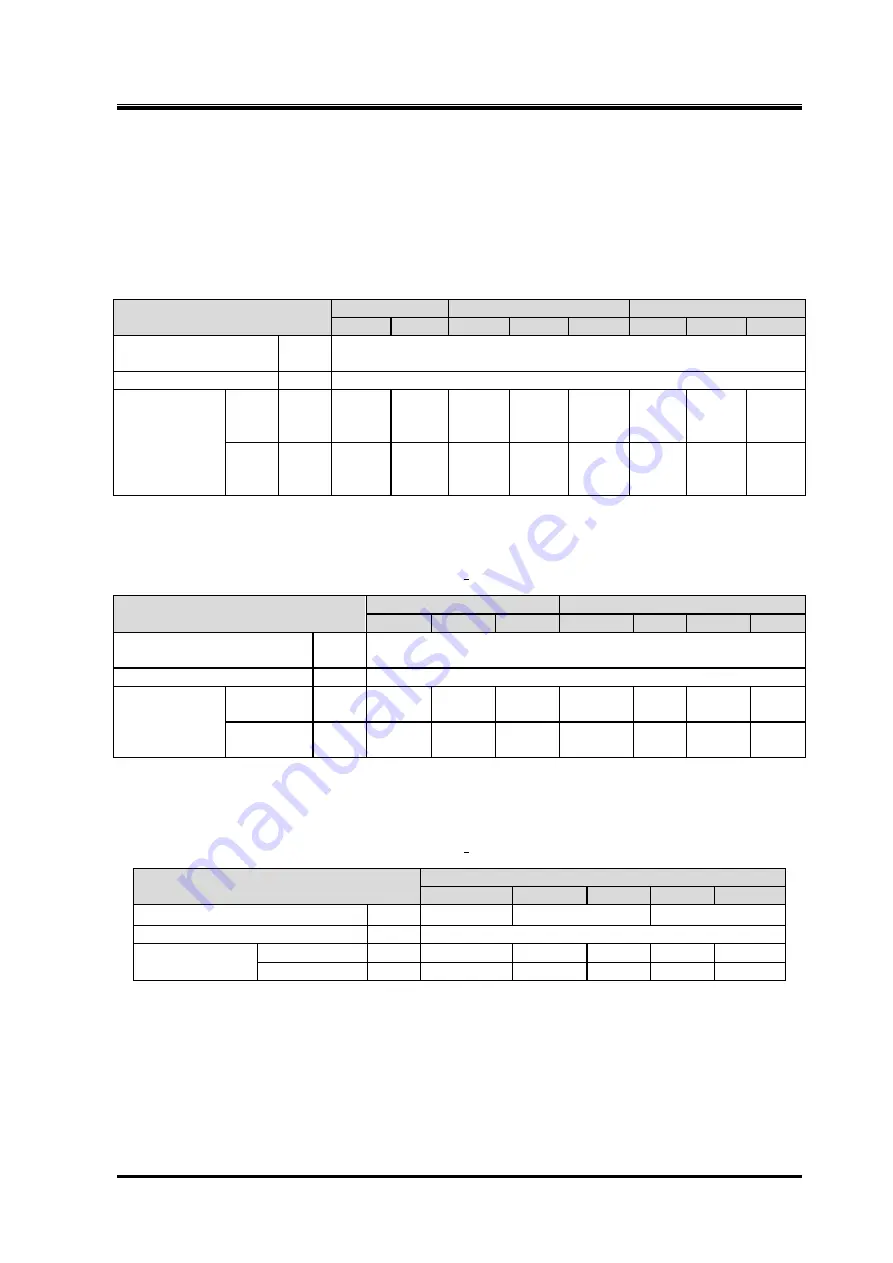
Chapter 2
Compressor Specifications and Structure
UD-series Screw Compressors
2.3
Compressor Specifications
2-4
2.3
Compressor Specifications
2.3.1 Standard Specifications
Table 2-1 UD-Series 125
Items
1 2 5
1 6 0
2 0 0
L U D
S U D
L U D
M U D
S U D
L U D
M U D
S U D
Capacity control
(actual load)
%
10
~
100
Direction of rotation
—
CCW seen from the motor
Theoretical
displacement
@
3550
min
-1
m
3
/h
356
237
749
624
499
1460
1220
975
@
2950
min
-1
m
3
/h
295
197
622
519
415
1210
1020
810
Table 2-2 UD-Series 250
Items
2 5 0
3 2 0
L U D
M U D
S U D
L L U D
L U D
M U D
S U D
Capacity control (actual
load)
%
10
~
100
Direction of rotation
—
CCW seen from the motor
Theoretical
displacement
@ 3550
min
-1
m
3
/h
2840
2380
1900
6740
5700
4760
3820
@ 2950
min
-1
m
3
/h
2360
1980
1580
5600
4740
3960
3170
Table 2-3 UD-Series 400
Items
4 0 0
X L U D
L L U D
L U D
M U D
S U D
Capacity control (actual load)
%
30
~
100
20
~
100
10
~
100
Direction of rotation
—
CCW seen from the motor
Theoretical
displacement
@ 3550 min
-1
m
3
/h
15600
13800
11700
9800
7800
@ 2950 min
-1
m
3
/h
12900
11500
9700
8140
6480