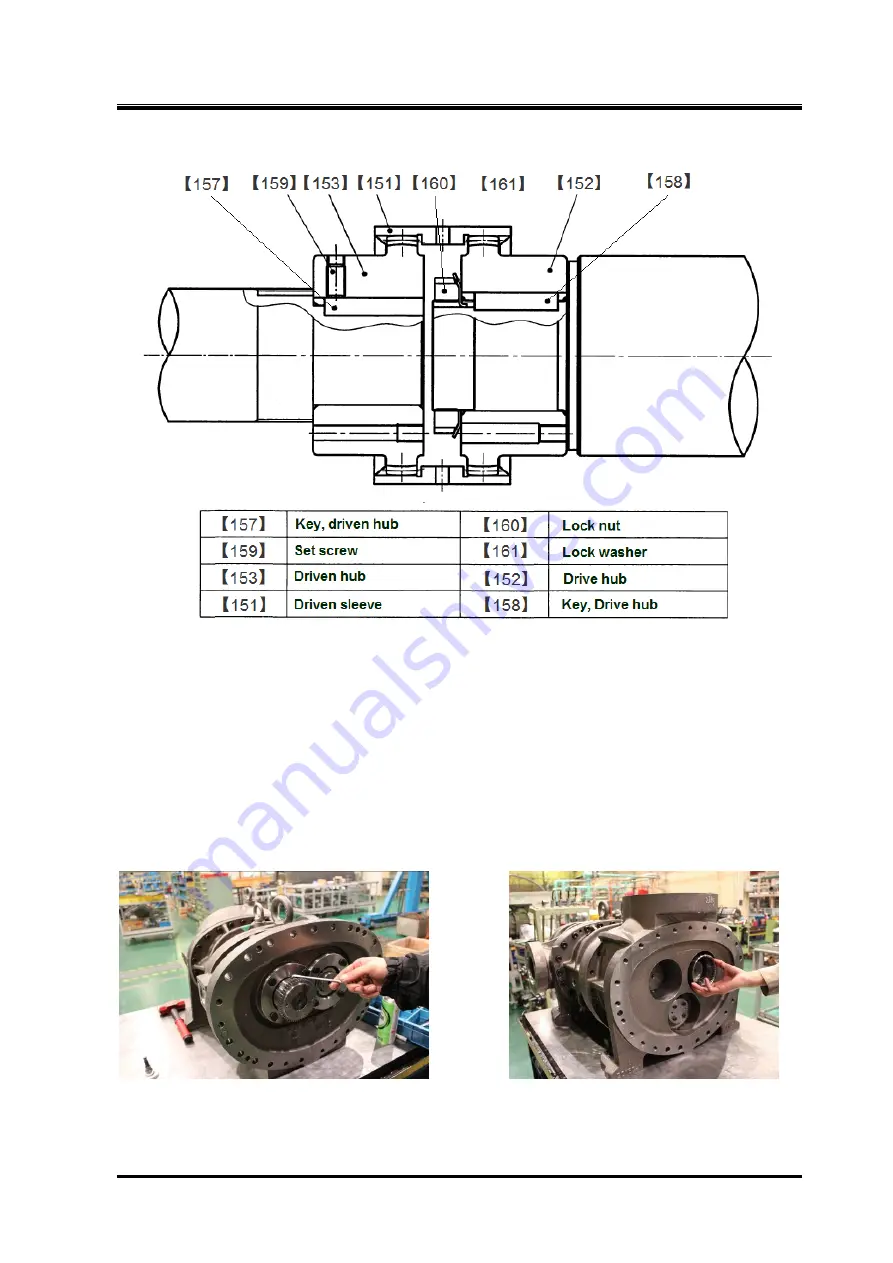
2200LZJE-HO-C6-N_2013.12.
Chapter 5 Maintenance
Compound 2-stage Screw Compressor 2016**C
5.7 Reassembly
5-53
5.7.9 Attaching High-stage and Low-stage
Figure 5-12 Assembly Drawing of Gear Coupling
a) On the high-stage, attach the driven hub
【
153
】
of the gear coupling, and fasten the M8 set screw
【
159
】
for securing the driven hub key
【
157
】
. This set screw is knurled and provided with
anti-loosening.
b) On the low-stage, attach the drive hub
【
152
】
, lock washer
【
161
】
and lock nut
【
160
】
in this order.
Fasten the lock nut with the specified torque or tightening angle range (see Chapter 7 "7.3
Tightening Torques for Bolts and Nuts" in this manual).
Align the lock washer claw with the notch of the lock nut, and bend it.
c) Set the driven sleeve onto the low-stage drive hub.
Photo 096 Tightening the Set Screw Photo 097 Setting Driven Sleeve onto Low-stage
for Securing Driven Hub