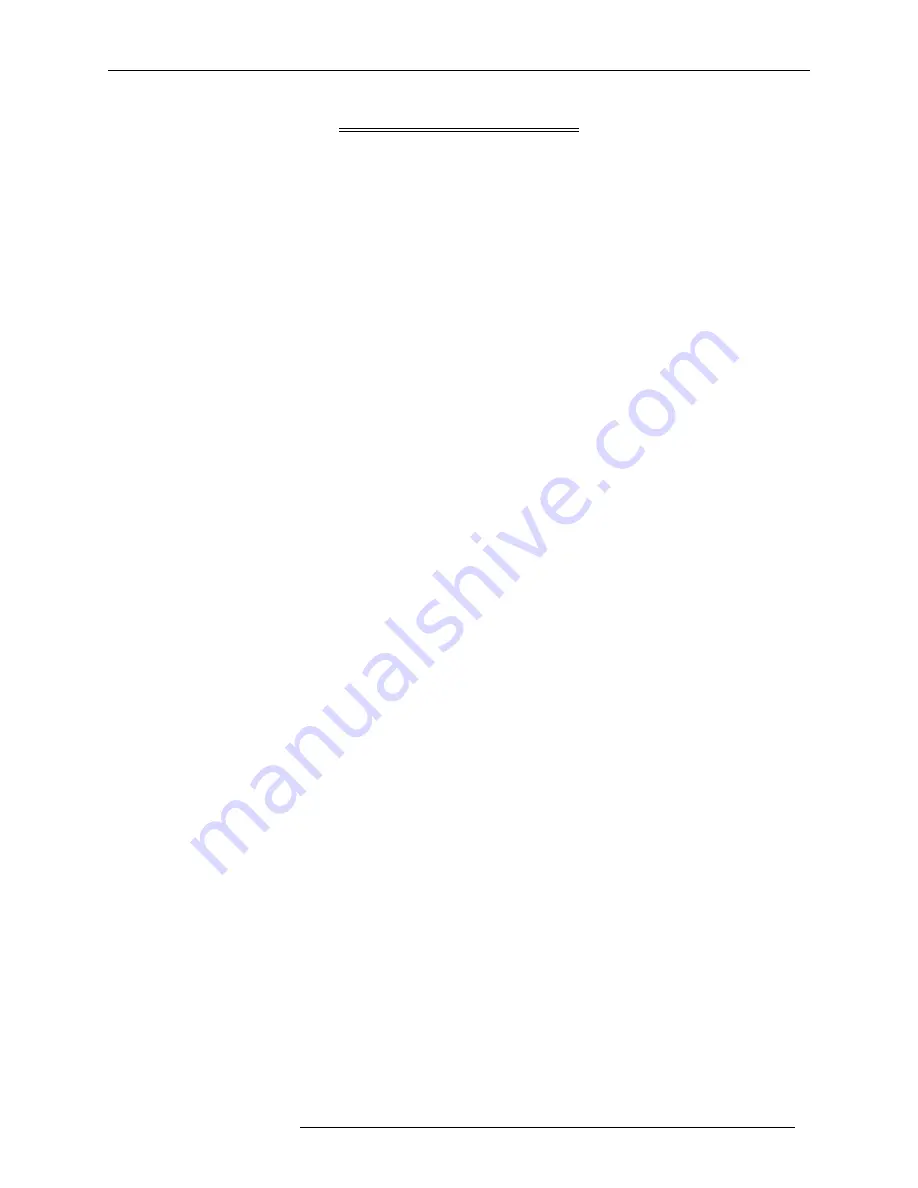
Mydax, Inc.
1M150W
Water Cooled Chiller
Designed for Lockheed Martin
14
SERVICE & WARRANTY
If a unit malfunctions, please contact the Mydax Service Department as soon as possible. Many small problems can lead
to large problems if not dealt with immediately. Please have the serial number and model number on hand when calling.
Mydax Service Department: (530) 888-6662 FAX: (530) 888-0962
Email:
service@mydax.com
RETURN OF UNIT FOR SERVICE
Many problems may be repaired by field exchanges of a module, pump, controller, etc. If return is required,
please obtain a return authorization number from the Mydax Service Department or the unit may not be
accepted at our receiving dock.
Please refer to the shipping instructions which follow.
SERVICE OF REFRIGERATION UNIT
Nearly all repairs to the refrigeration unit involve brazing or silver soldering. This should only be done by a
person trained in refrigeration service and familiar with the Mydax system.
NOTE: Before servicing any refrigeration unit involving brazing, remove all refrigerant from the system.
Evacuate to a 400 micron vacuum to remove refrigerant residues, then open all service valves to dry
air or dry nitrogen before use of a torch.
In particular, service of Mydax refrigeration circuits requires attention to the following:
1)
Use caution to protect components from heat damage.
2)
Prevent any moisture from entering the circuit, as Mydax proportional valves do not function with moisture
present. Once moisture has entered the system it cannot be removed.
3)
Remove insulation and instrumentation wiring or use heat shields to protect them from torch heat during work.
4)
Before recharging the circuit, evacuate it to 200 microns at a minimum room temperature of 75
°
F for three
hours, or longer for units with 4 horsepower or larger compressors.
ONE YEAR WARRANTY
Mydax, Inc. warrants that its temperature control system, and the component parts thereof, will be free from defects in
workmanship and materials for a period of one year from the date of delivery. In the event that warranty service is
required, the customer is requested to send the equipment freight prepaid to the factory for service. Mydax will then
perform the appropriate service and will return the equipment freight prepaid.
If field service is required during the warranty period, the customer will be responsible for all travel expenses including
airfare, car rental, lodging and meals. The customer will not be invoiced for any warranty service performed, with regard
to either labor or materials, during a field service visit.