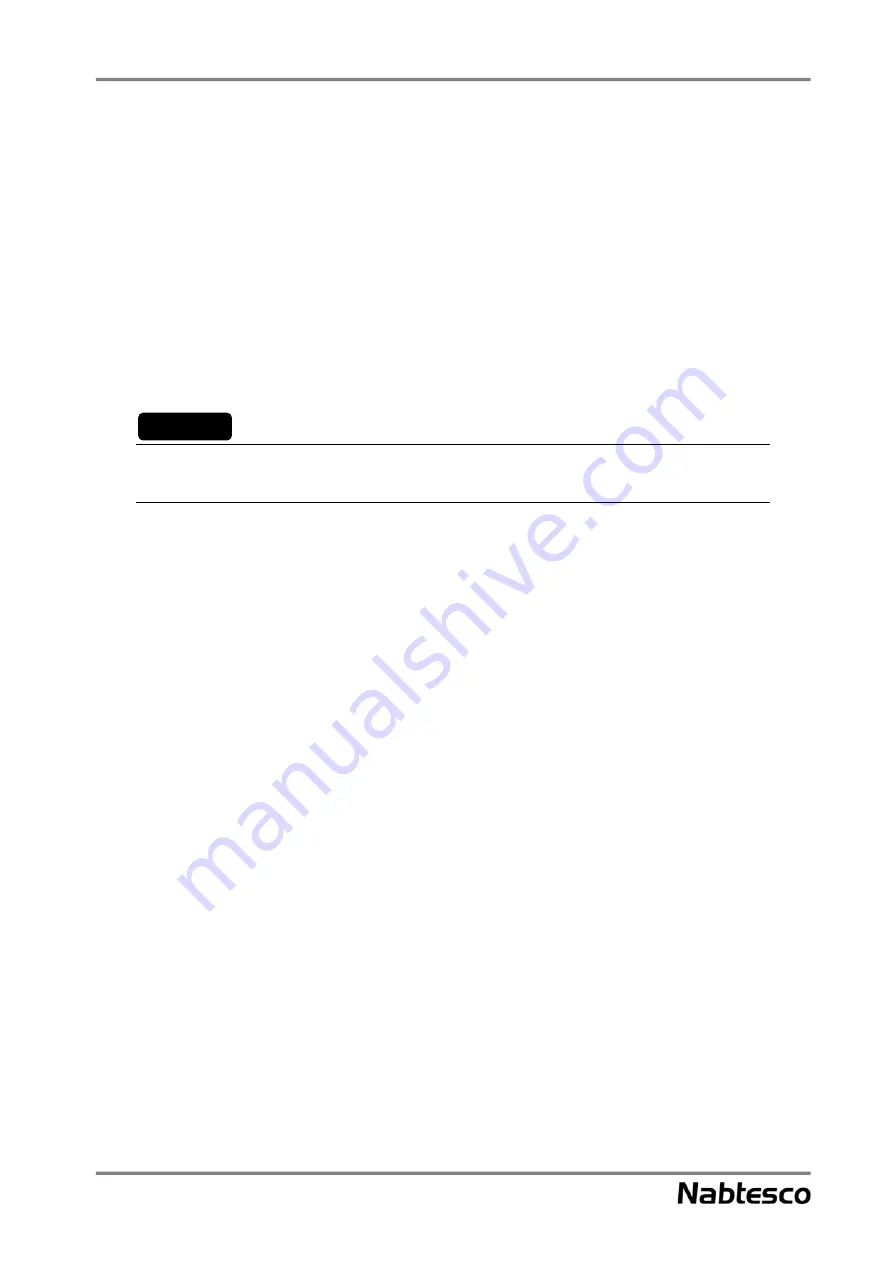
Chapter 7 Maintenance and Inspection
32
Step 9
• Repeat
steps 4 to 8
until the reduction gear is filled with the same amount of lubricant as that was
drained.
Step 10
• It is recommended that the inside of the reduction gear is flushed so that the lubricant can be
replaced more efficiently.
• When flushing the inside of the reduction gear, remove the injector from the tapped hole on the
supply side, and insert a hexagon socket head cap plug into the tapped hole on the drain side.
(Reference: Table 7-3 “Plug size and tightening torque”)
• Calculate the output shaft conversion and set the servomotor rotation speed so that the output shaft
rotation speed is 5 to 10 rpm. Then, rotate the motor for about one minute.
• Perform
steps 1 to 9
again.
Set the rotation speed based on the output shaft conversion by taking the customer’s operation
conditions into account.
Step 11
• Attach the hexagon socket head cap plugs and other parts removed in step 2 above to the tapped
holes for injecting/draining grease with the specified tightening torque.
(Reference: Table 7-3 “Plug size and tightening torque”)
• Replace with new seal tape.
• If the customer’s component is flush with the tapped holes for injecting/draining grease, tighten it
so that the plugs will not protrude from the edge surface. However, tighten the hexagon socket head
cap plug GM-1/8 to a maximum tightening torque of 14.75 (Nm).
Step 12
• Wipe off the lubricant adhering to the surrounding completely.
Important