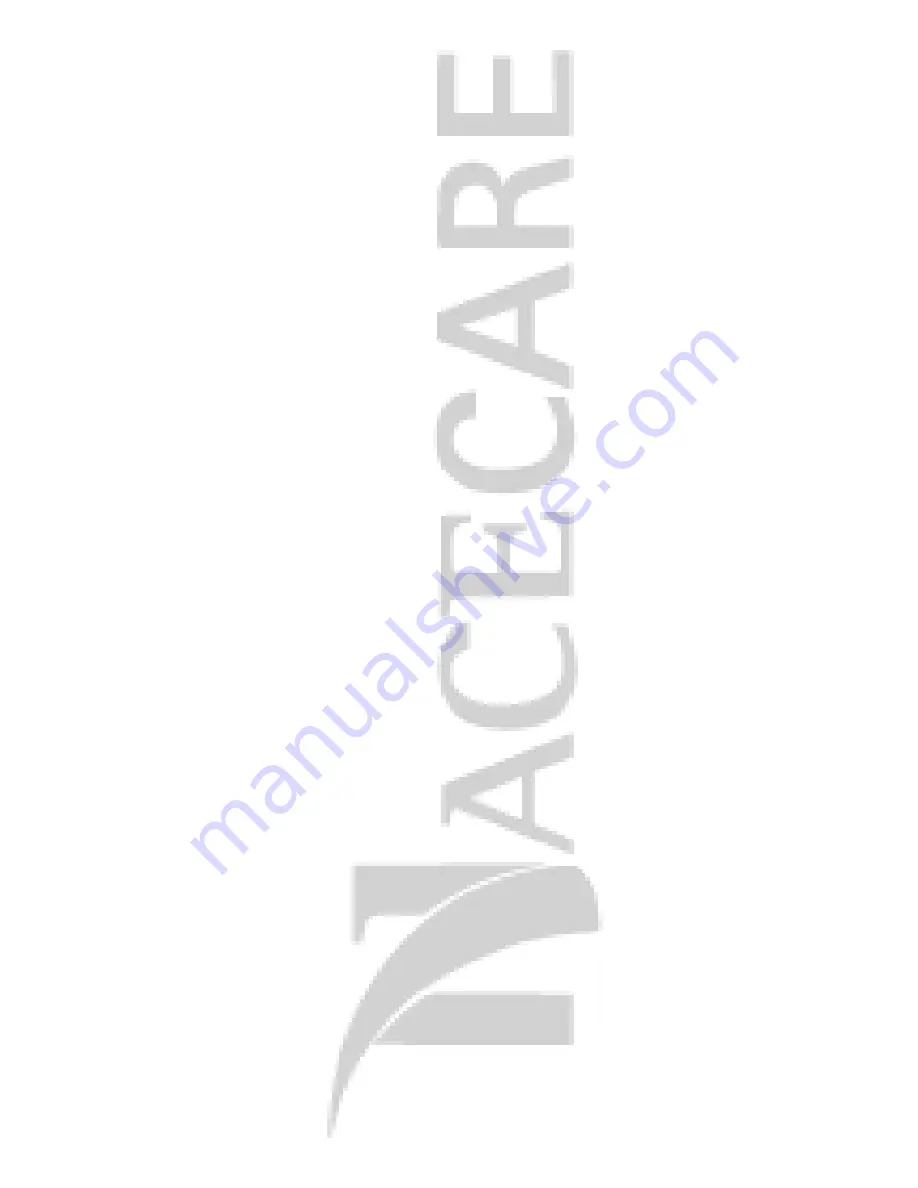
31
Notes:
.......................................................
.......................................................
.......................................................
.......................................................
.......................................................
.......................................................
.......................................................
.......................................................
.......................................................
.......................................................
.......................................................
.......................................................
.......................................................
.......................................................
.......................................................
.......................................................
.......................................................
.......................................................
.......................................................
.......................................................
.......................................................
.......................................................
.......................................................
.......................................................
.......................................................
.......................................................
.......................................................
.......................................................
.......................................................
.......................................................
Summary of Contents for TTV 678-300T
Page 26: ...26 WD 0359 A18 01 04 2014 ...
Page 27: ...27 ...
Page 29: ...29 Notes ...
Page 30: ...30 Notes ...
Page 31: ...31 Notes ...