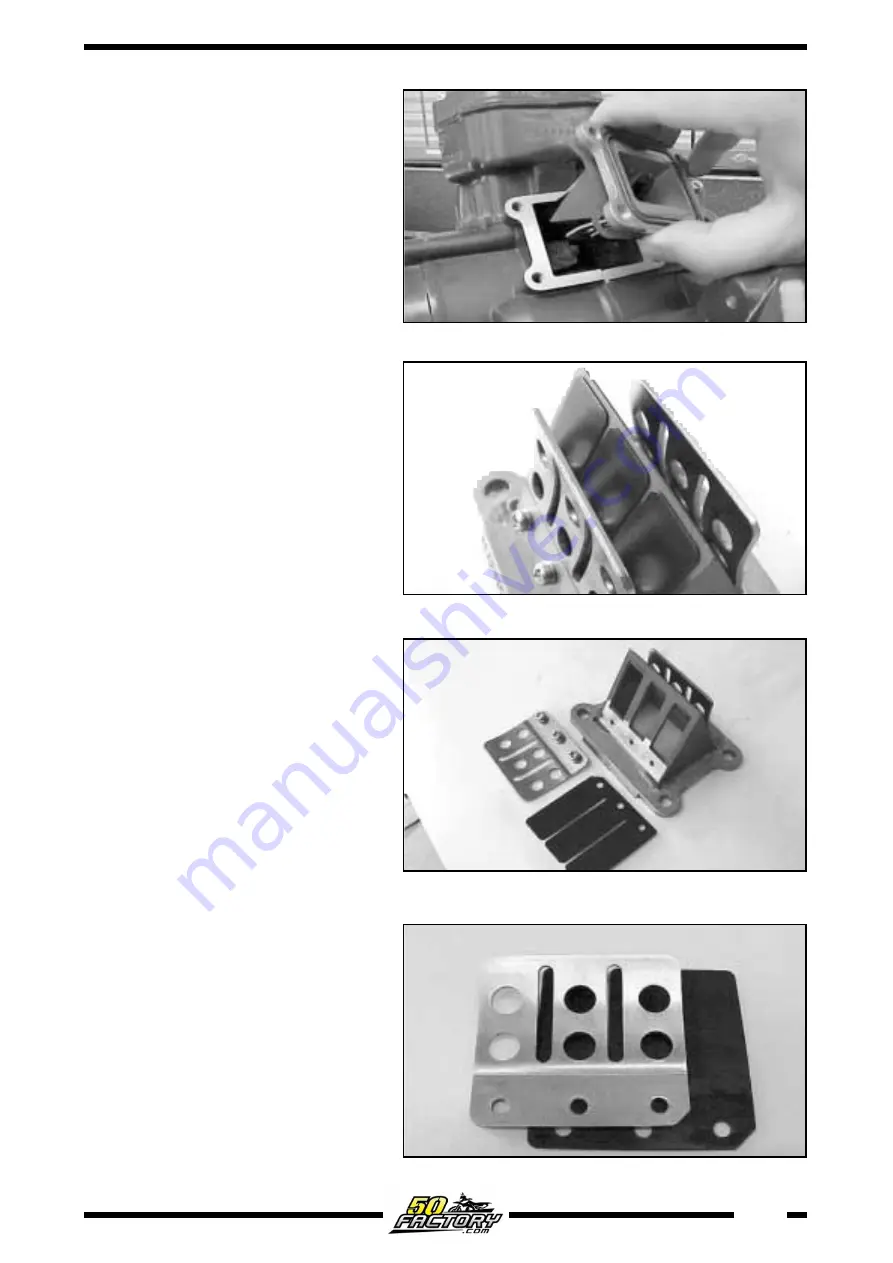
STRIPPING DOWN THE
REED VALVE
- Withdraw the carburettor from the
engine
- Remove the inlet nozzle securing
screws, as is, and then it is possible
to gain access and withdraw the
reed valve.
- Check that there are no signs of
cracking, deformation or breaking in
the valve reed petals. If signs of
damage are present, replace them.
- Remove the opening limiter plate
and inlet valve reed petal securing
screws and check that there are no
cracks in the securing base of the
petals. If cracks are found, replace
the valve reeds.
ASSEMBLING THE VALVE
REEDS
- Assemble in reverse order to strip-
ping down, paying particular atten-
tion to the correct positioning of the
opening limiter plate and the reeds
(it is necessary to mate the beve-
lling). Elimination of the opening
height limiter will change the perfor-
mance of the engine and may affect
engine reliability.
- Check the reed valve box O-ring
and replace if it shows signs of
damage. Install a new gasket.
5-1
Summary of Contents for Derbi Euro 2
Page 1: ...moteur derbi euro 2 documentation atelier EN ANGLAIS ...
Page 3: ......