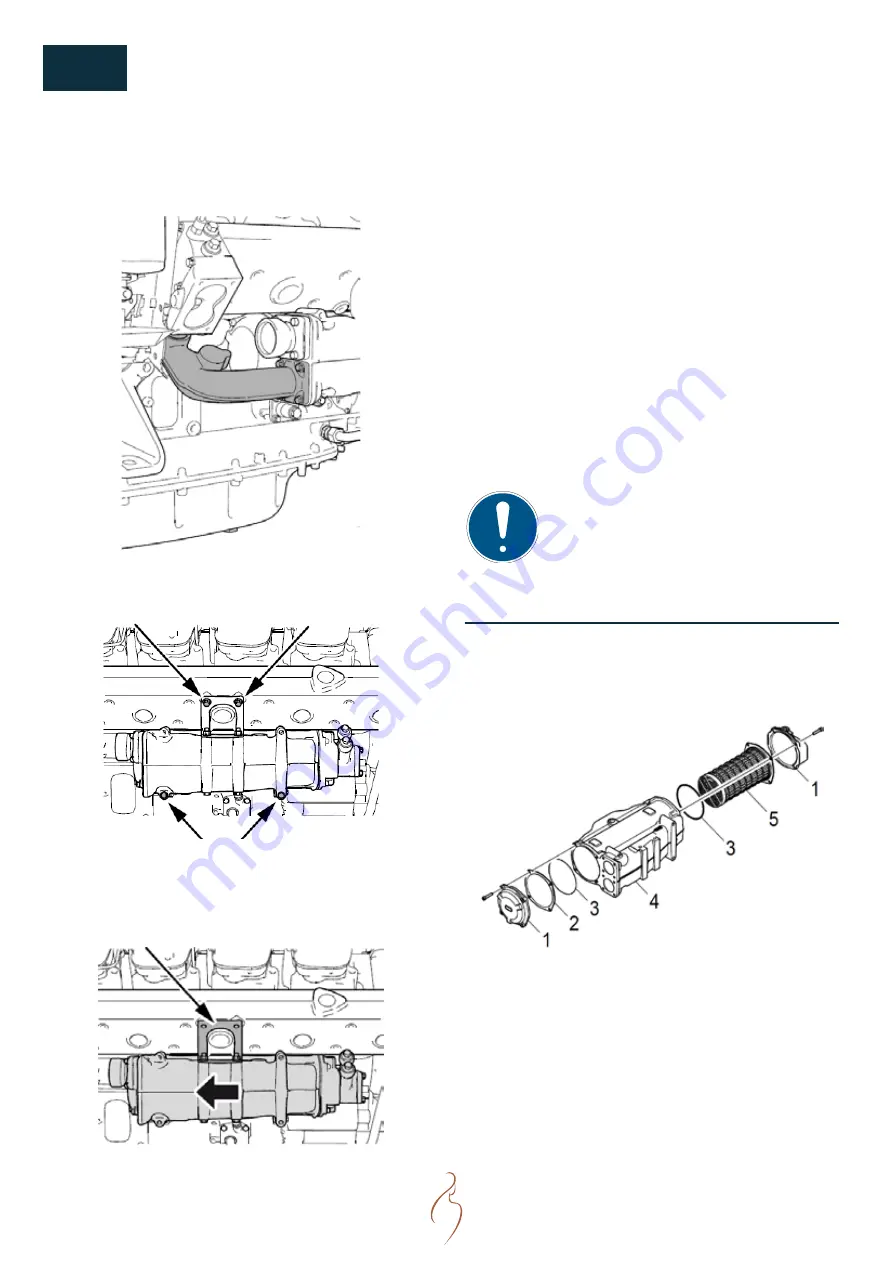
77
5. Remove the coolant pipe from the heat exchanger:
6. Remove the screws on the heat exchanger and the 2
upper screws on the exhaust manifold bracket:
7. Remove the heat exchanger by holding it in the brack-
et, moving the heat exchanger slightly to the side and
removing it:
S08
MAINTENANCE
CLEANING THE HEAT
EXCHANGER
1. Remove the screws on the heat exchanger covers (1)
and remove the covers. Mark the covers so that you can
put them back on the correct side.
2. Press in the cooler core (5) slightly on one side and
pull it out from the other side.
3. Clean the cooler core on the outside with paraffin-
based engine detergent. Remove any internal deposits
using a round rod. Renew the cooler core if it is dam-
aged.
IMPORTANT !
Do not use caustic soda as this could damage the alu-
minium.
4. Renew damaged or hard O-rings (3).
5. Assemble the heat exchanger. Tighten the M8 screws
on the covers to 15 Nm (11 lb/ft).
Legend:
1. Cover.
2. Spacer.
3. O-rings.
4. Heat exchanger housing.
5. Cooler core.
Summary of Contents for N16.1000 CR3
Page 2: ......
Page 4: ......
Page 34: ...34 S05 COMPONENTS ENGINE VIEWS N16 CR3...
Page 35: ...35 NOTES...
Page 48: ...48 S06 INSTRUMENTATION SYSTEM LAYOUT INCLUDING OPTIONS...
Page 118: ......