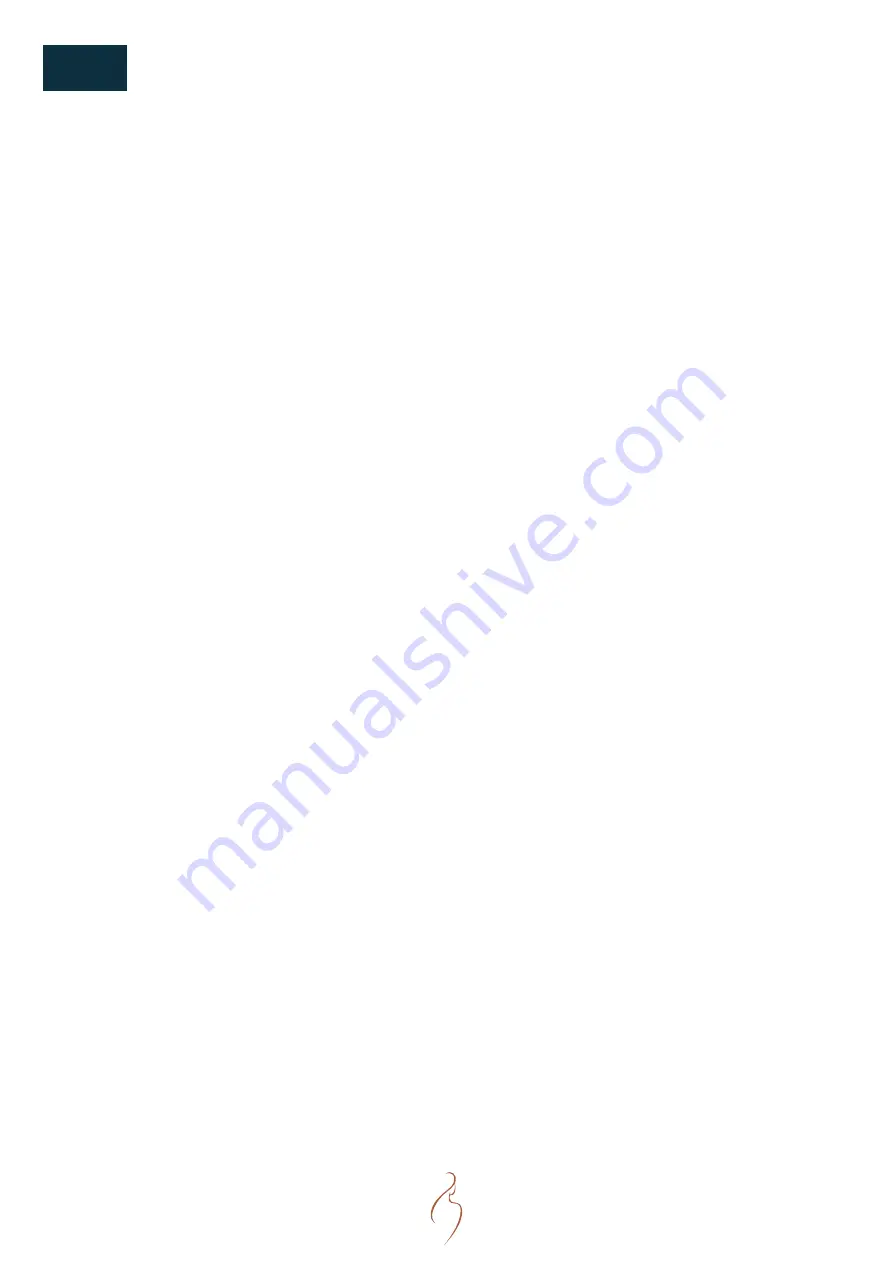
27
S04
ENGINE WARRANTY
EPA WARRANTY
EPA and CARB warranties only apply to new engines
having the certification label affixed to the engine and
sold as stated above in the geographic areas.
The presence of an EU number signifies that the engine
has been certified with the European Union countries
per Directive 97/68/EC. The EPA and/or CARB emissions
warranties do not apply to the EU countries.
When applied onto engine, Emission Control label must
never be removed from engine block neither covered
with a layer of paint. This label is the evidence showing
that the engine is meeting U.S emissions regulations. It
must be kept available at anytime once the vessel has
entered waters being in the scope of the North American
Emission Control Area (ECA).
EMISSION CONTROL SYSTEM(S) LAWS
The U.S. EPA and CARB prohibit the removal or render
-
ing inoperative of any device or element of design in
-
stalled on or in engines/equipment in compliance with
applicable emission regulations prior to or after the sale
and delivery of the engines/equipment to the ultimate
purchaser.
EUROPEAN UNION (EU) DECLARATION OF EMISSIONS
CONFORMITY
The presence of an EU number on the label signifies
that the Marine Diesel Engine has been certified with
the European Union countries per Directives 97/68/EC
as amended by Directive 2004/26/EC. The EU engine
family is listed on the Emissions Label.
When installed in accordance with the manufacturer’s
instructions, Nanni Industries Marine Diesel Propul
-
sion Engines without integral exhaust certified under
Directive 97/68/EC as amended by Directive 2004/26/
EC produce exhaust emissions of carbon monoxide,
hydrocarbons, nitrogen oxides and particle emissions
complying with the requirements of the Recreational
Craft Directive 2003/44/EC.
Summary of Contents for Z4.205
Page 2: ......
Page 4: ......
Page 39: ...39 S06 COMPONENTS ENGINE VIEWS T4 205 T4 230 T4 270...
Page 40: ...40 S06 COMPONENTS ENGINE VIEWS Z4 205 Z4 230 Z4 270...
Page 97: ......