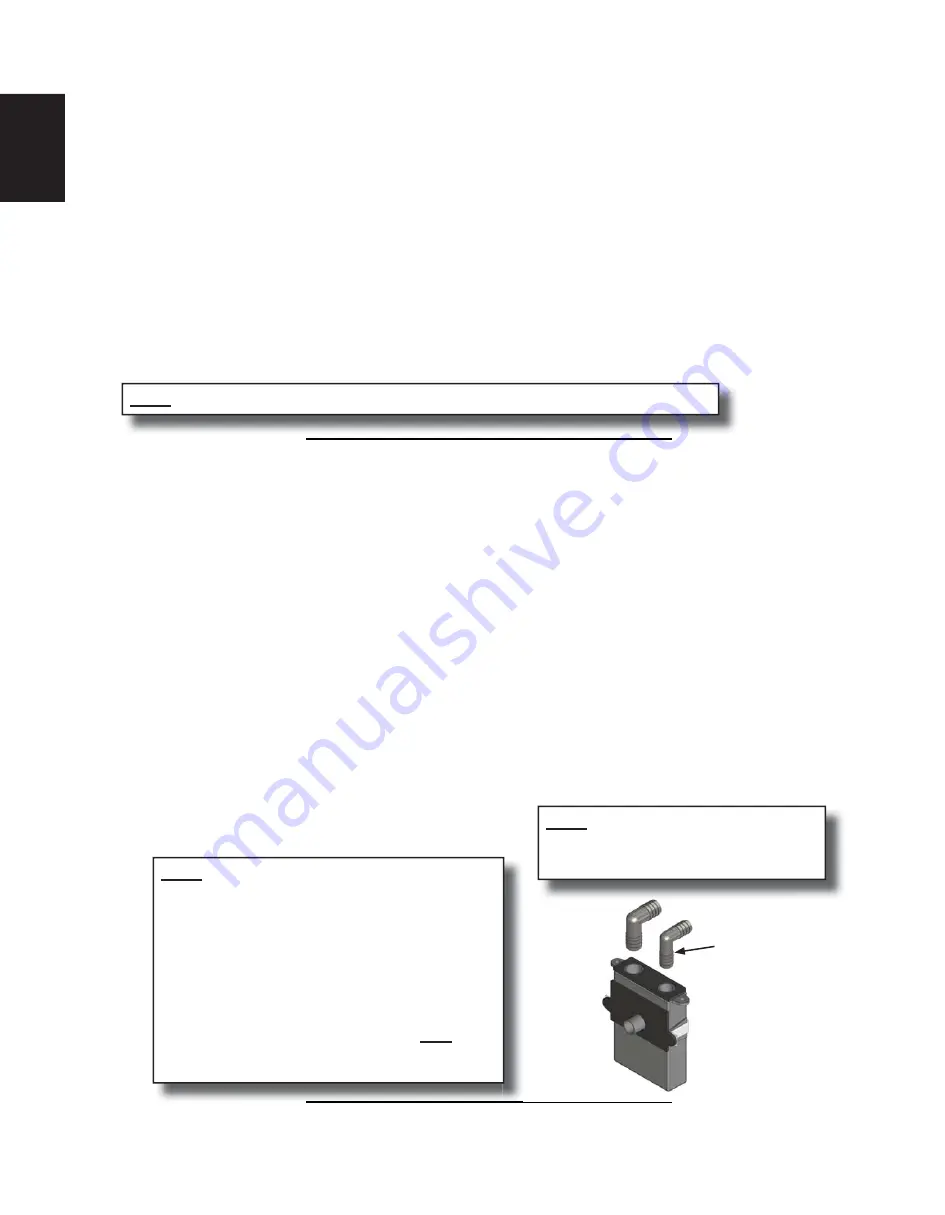
W415-2159 / D / 11.24.17
30
IOM
IOM
11.2 CONDENSATE DRAINS
11.3 PREPARATIONS FOR VENT AND DRAINING OPTION
H16.2.2C
The furnace may condense as much as 4-1/2 pounds of water per hour (approximately 2 imperial quarts, 2-1/2
U.S. quarts or 2-1/4 liters). It is necessary to make provisions for draining the condensate away. The furnace is
supplied with a drain trap assembly. See Figures 16-20 for possible locations of the drain trap.
Af
fi
x the condensate trap assembly to the interior of the side panel in the blower compartment for up
fl
ow
positions; the interior of the side panel in the burner compartment for down
fl
ow positions. For horizontal
positions af
fi
x the condensate trap assembly to the exterior side panels. See Figures 16-20.
Three plastic drain hose clamps are provided in the parts bag. The large ones are used for securing the drain
hose to the front manifold cover drain outlet, and securing the drain hose to the 5/8” barbed
fi
tting on the
condensate trap assembly. The small one is used to secure the drain hose to the 1/2” barbed
fi
tting on the
condensate trap assembly.
The drain coupling on the exhauster will work better if the drain holes are pointed down about 15 degrees. The
drain hose supplied with the furnace is long enough to reach either side panel; however, it must be cut to
fi
t each
application. This is to prevent kinking in the drain lines.
NOTE
: It is recommended that pliers be used to
fi
rmly clamp the plastic hose clamps.
H16.3.2A
1. Determine the most suitable vent and drain options for installation. See Figures 16-20 for reference, and
refer to Exhauster Rotation Instructions section if necessary.
2. Remove the 3-1/2” plastic exhaust vent cap (if required), and cover vent hole not in use. Install rubber
grommet (in parts bag) for 2” vent pipe. Connect vent pipe (field supplied). If using 1-1/2” or 3” vent, make
transition as close as possible to the unit and on a vertical section.
3. Connect 2” air intake pipe (field supplied).
The exhaust vent must be supported appropriately prior to
it being fitted to the exhauster. Under no circumstances shall the exhauster bear any weight of the
venting system.
4. Remove the plastic air inlet cap and connect the 2” PVC air intake connector with the rubber gasket on the
outside of the unit using the 2” lock nut (in parts bag).
5. Remove the two plastic caps attached to the blower division, and the one attached to the side panel if
applicable.
6. Affix the condensate trap assembly to the interior of the side panel in the blower compartment for upflow
positions using the two screws provided in parts bag. For horizontal positions affix the condensate trap
assembly to the exterior side panels.
7. Make sure combustion compartment is fully sealed.
NOTE
•
Condensate drain tubing must be cut to
appropriate length and slopping towards
condensate trap, ensuring that drain hoses
do not create traps prior to the condensate
trap assembly.
•
Condensate trap must be primed with
water prior to initial furnace start up.
•
Any increase of venting diameter must
be done on the vertical sections NOT
horizontal sections.
NOTE
Barbed
fi
ttings must be fully inserted into
condensate trap, seated to barb
fl
ange.
BARB FLANGE
Summary of Contents for 9600E E-STAR Series
Page 27: ...W415 2159 D 11 24 17 27 IOM FIGURE 14A DIRECT VENT TERMINAL CLEARANCES...
Page 28: ...W415 2159 D 11 24 17 28 IOM IOM FIGURE 14B NON DIRECT VENT TERMINAL CLEARANCES...
Page 57: ...W415 2159 D 11 24 17 57 IOM 23 0 SERVICE HISTORY 43 1...
Page 58: ...W415 2159 D 11 24 17 58 IOM IOM 24 0 NOTES 44 1...
Page 74: ...6 0 NOTES 44 1 W415 2159 D 11 24 17 UM 74...