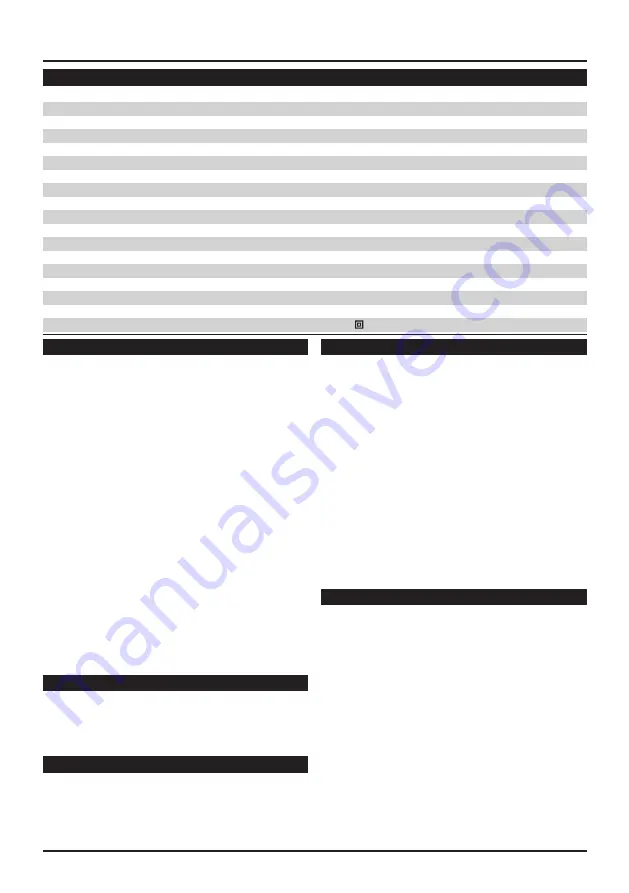
English
1
Technical data
Router
Type
EFH 36-E9
Voltage.
30–40.V
Frequency.
50-60.Hz
Input.
1,010.W
Output.power.
530.W
Rpm.in.idle.cycle.
8.000–5.000.min
-1
Constant.electronics./.Starting.current.limitation.
Rpm.preselection.
Spindle.lock.
Spring.collet.ø..
8.mm
Max..ø.of.forming.cutter.
36.mm
Max..ø.of.cylindrical.cutter.
30.mm
Hoisting.
50.mm
Depth.adjustment.range.
0-50.mm
Stepped.backstop.positions.
3x
Weight.(without.accessories).
..kg
Protection.class.
II./.
Controls
1 ............Switch
2 ............Rpm adjustment preselector (EFH 36-E9)
3 ............Air vents
4 ............Depth backstop
5 ............Indicator
6 ............Routing depth adjustment scale
7 ............Milling depth adjustment selector
8 ............Clamping lever
9 ............Self-locking bolt
10 ..........Additional handle
11 ..........Wing screws
12 ..........Stop screws
13 ..........Lock nut
14 ..........Stepped backstop
15 ..........Skid plate
16 ..........Stop lever for suction adaptor
17 ..........Foundation slab
18 ..........Wing screw for depth backstop detent
19 ..........Spindle lock
20 ..........Cap nut with clamping spring collet
21 ..........Spanner
22 ..........Suction adaptor
23 ..........Wing screws of longitudinal guide
24 ..........Longitudinal guide
25 ..........Interposer bars
26 ..........Milled bolt
27 ..........Gentle adjustment of guide with scale
28 ..........Cover ring
29 ..........Bolts (2x)
30 ..........Copying case
Depicted or described accessories need not necessarily become the in-
tegral part of delivery.
Double insulation
To ensure maximum safety of the user, our tools are designed and built
to satisfy applicable European standards (EN standards). Tools with
double insulation are marked by the international symbol of a double
square. These tools must not be grounded and a two-wire cable is suf-
ficient to supply them with power. Tools are shielded in accordance with
EN 55014.
Use
With the help of a solid support, the machine is designed for routing of
grooves, edges, profiles and longitudinal openings in timber, plastic and
light building materials, as well as for copying routing.
With reduced rpm and suitable routers, also non-ferrous metals can be
machined.
The user himself is liable for any damage caused by improper use.
Safety instructions
Wear suitable protective gloves and solid shoes when working with
the machine.
At work, wear googles and ear defenders.
Hold the machine with both hands and stand safely.
During work, lead the movable supply always away from the tool.
Always clamp the workpiece carefully.
Lead the machine into the material in activated state.
Before turning the machine on, remove the key from it.
Before putting in operation check the clapming of the cutter tool.
Press the spindle lock button only in stillstand.
Use only such cutter tools, allowed rpm of which is at least as high
as the highest rpm of the machine in idle cycle.
The shank diameter of the router must conform to that of the hold-
er (clamping spring collet).
Never route over metal objects, nails or screws.
Do not come close to rotating router.
When the work cycle is over, put the machine back to the upper
initial position by releasing the clamping lever.
Protect the tools from impacts and strokes.
Do not carry the machine by the cable.
Mounting the cutter tools
Selection of routers
Depending on the machining and purpose of mounting, cutter tools of
various designs and quality are available.
Cutter tools of (HSS) are suitable for machining of soft materials, such as
soft timber or plastics.
Cutter tools with razor edges made of hard metal (HM) are especially
suitable for hard and abrasive materials, e.g. hard timber and alumin-
ium.
The cutter tools used must be approved for highest rpm of rel-
evant machine type.
The shank diameter must conform to that of the tool holder
(clamping spring collet).
You can receive genuine cutter tools of the broad NAREX accessories
portfolio at your specialized dealer.
Cutter putting on (a)
Prior to any intervention into the machine disconnect the power supply
plug from the socket.
We recommend to wear protective gloves when putting on and replac-
ing the milling tools.