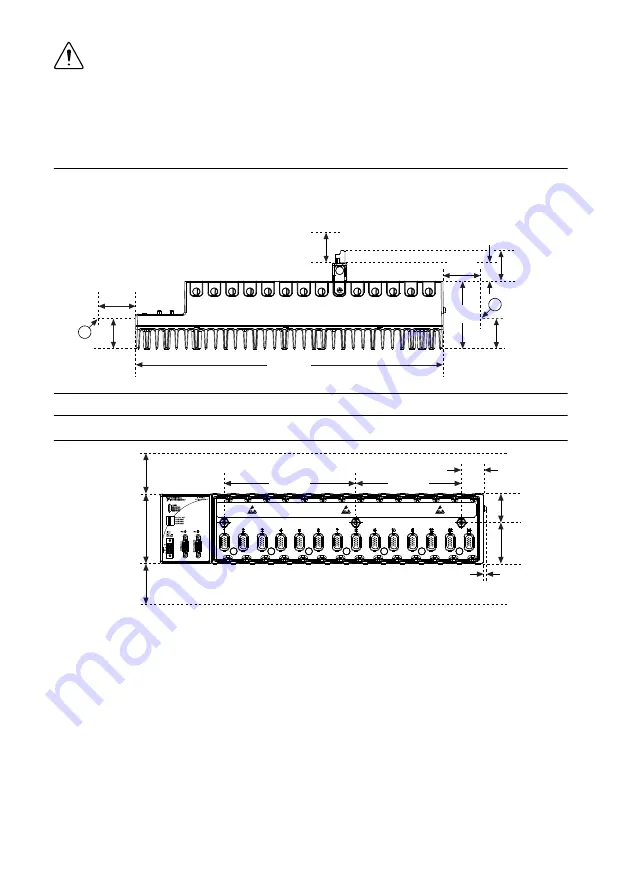
Caution
Your installation must meet the following requirements for space and
cabling clearance:
•
Allow 50.8 mm (2 in.) on the top and the bottom of the chassis for air
circulation.
•
Allow 50.8 mm (2 in.) in front of modules for cabling clearance for common
connectors, such as the 10-terminal, detachable screw terminal connector.
Figure 3.
NI 9157/9159, Bottom View with Dimensions
63.5 mm
(2.50 in.)
50.8 mm
(2 in.)
406.3 mm
(16 in.)
50.8 mm
(2 in.)
48.4 mm
(1.91 in.)
1
1
89.4 mm
(3.52 in.)
63.5 mm
(2.50 in.)
29 mm
(1.14 in.)
Cabling Clearance
50.8 mm (2 in.)
1. Measure ambient temperature here.
Figure 4.
NI 9157/9159, Front View with Dimensions
51.7 mm
(2.04 in.)
28.0 mm
(1.10 in.)
4.1 mm
(0.16 in.)
Cooling Outline
50.8 mm (2 in.)
88.1 mm
(3.47 in.)
Cooling Outline
50.8 mm (2 in.)
36.4 mm
(1.43 in.)
132.6 mm
(5.22 in.)
165.1 mm
(6.50 in.)
NI 9157/9159 User Manual and Specifications
|
© National Instruments
|
5