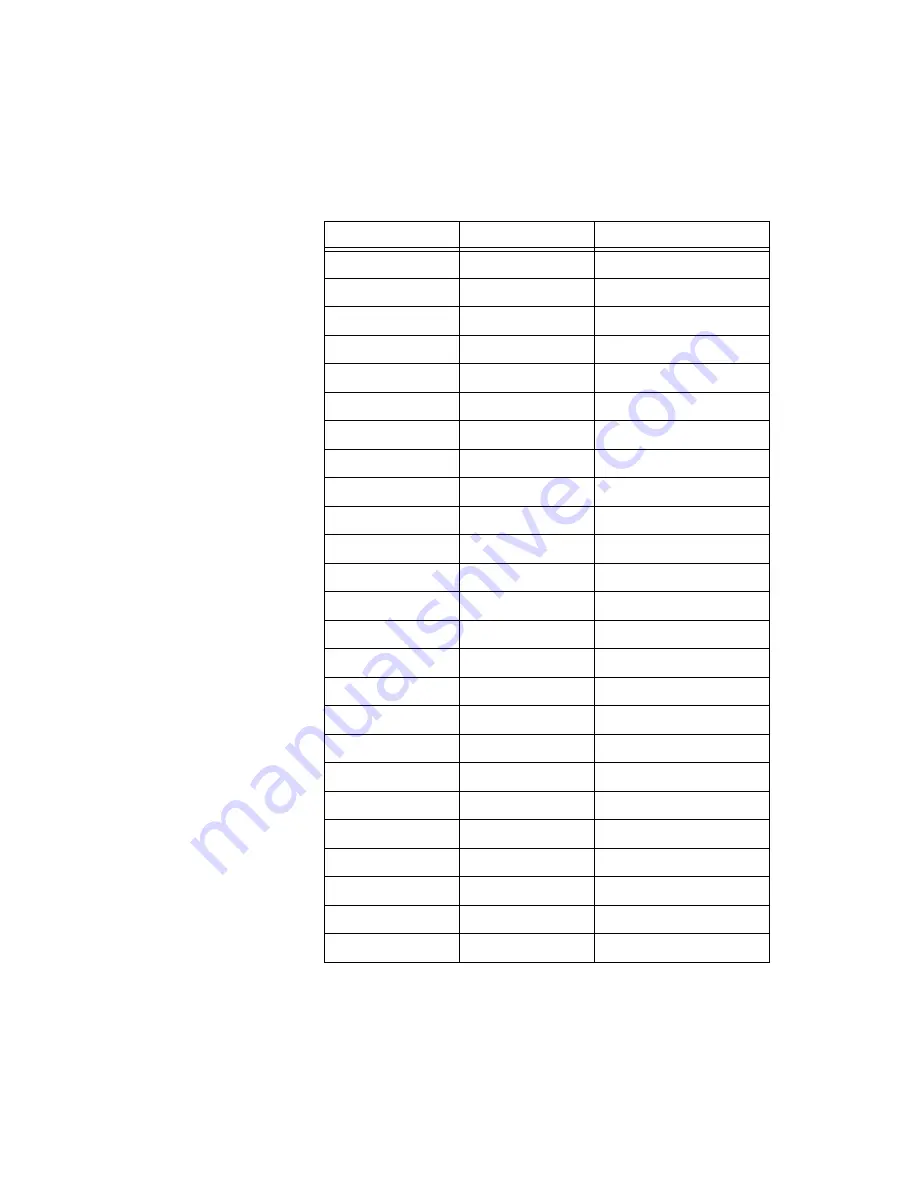
Chapter 3
Connecting the UMI-7774/7772 to Drives and Other Devices
©
National Instruments Corporation
3-17
National Instruments UMI-7774/7772 User Manual
Table 3-5.
Per Axis Feedback Connector Pin Assignment
Pin
Signal
Optically Isolated
1
Encoder Phase A
No
2
Encoder Phase B
No
3
Encoder Index
No
4
+5 V (Output)
No
5
Hall Sensor A
No
6
Hall Sensor B
No
7
Hall Sensor C
No
8
+5 V (Output)
No
9
NC
No
10
Forward Limit
Yes
11
Home Input
Yes
12
Reverse Limit
Yes
13
Iso Power (Output)
Yes
14
Encoder Phase A–
No
15
Encoder Phase B–
No
16
Encoder Index–
No
17
Digital Ground
No
18
Digital Ground
No
19
Digital Ground
No
20
Digital Ground
No
21
NC
No
22
Iso Common
Yes
23
Iso Common
Yes
24
Iso Common
Yes
25
Iso Common
Yes