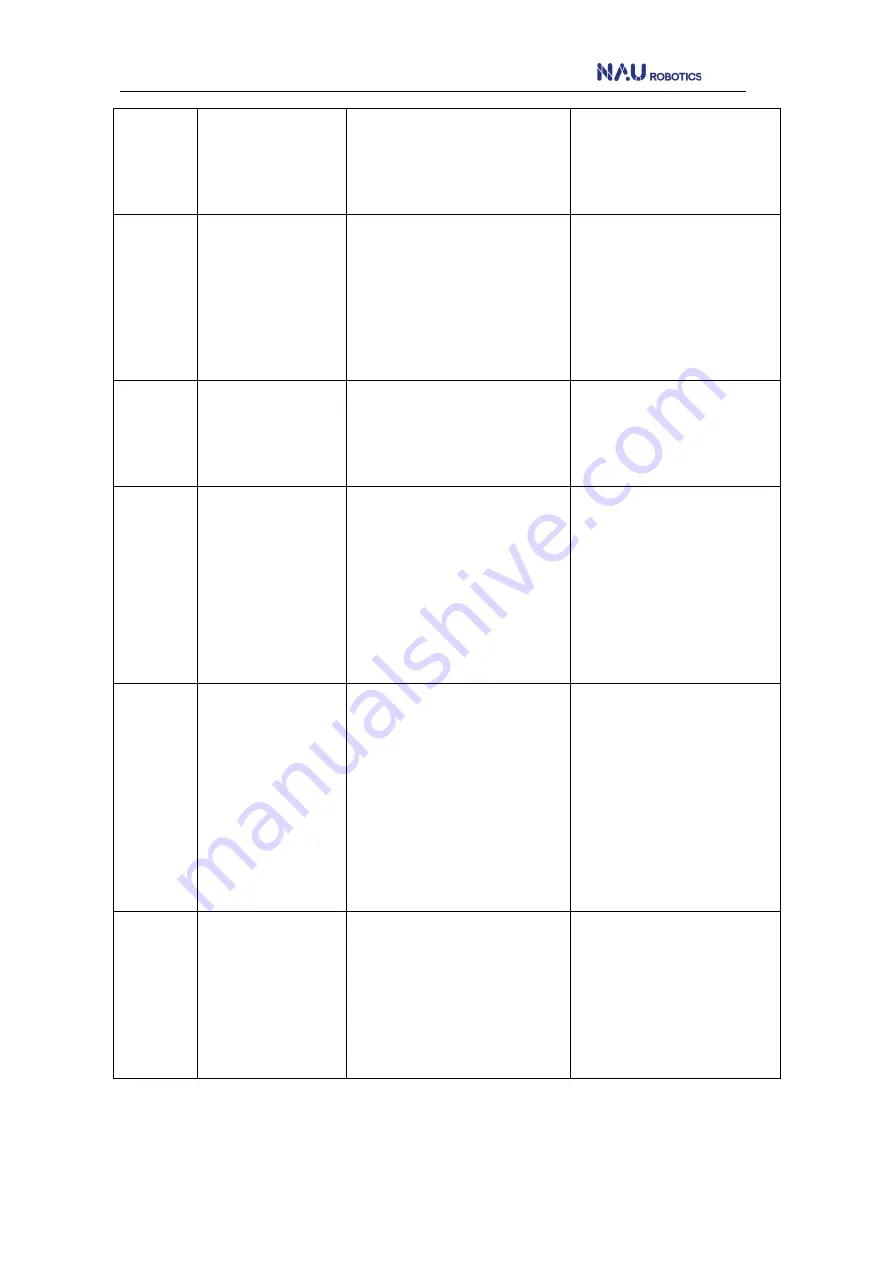
RC40 Control manual
88
e0xFF12
Programmable
device firmware
mismatch
Drive damage
Repair or replace the drive
e0xFF13
Power board
parameters
mismatch & Control
encoder speeding
fault
Drive damage
Repair or replace the drive
e0xFF1A
Motor phase
sequence wiring
error
Motor phase sequence
connection error
Check the motor connection
phase sequence
e0xFF00
System initialization
failed
1.Wrong setting of servo
parameters;
2.Wrong connection of motor
encoder or damaged
encoder;
3.Drive damaged;
1.Check encoder wiring and
encoder;
2.repair or replace driver;
e0xFF2B
Encoder internal
communication
abnormal
1.Encoder wiring error;
2.Encoder cable is damaged;
3.Encoder damage;
4.Encoder parameter setting
error;
1.Check the encoder
connection;
2.Check the encoder
cables;
3.Replace the encoder;
4.Check the encoder
parameters
e0xFF05
Encoder internal
fault
1.Encoder wiring error;
2.Encoder cable is damaged;
3.Encoder damage;
4.Encoder parameter setting
error;
1.Check the encoder
connection;
2.Check the encoder
cables;
3.Replace the encoder;