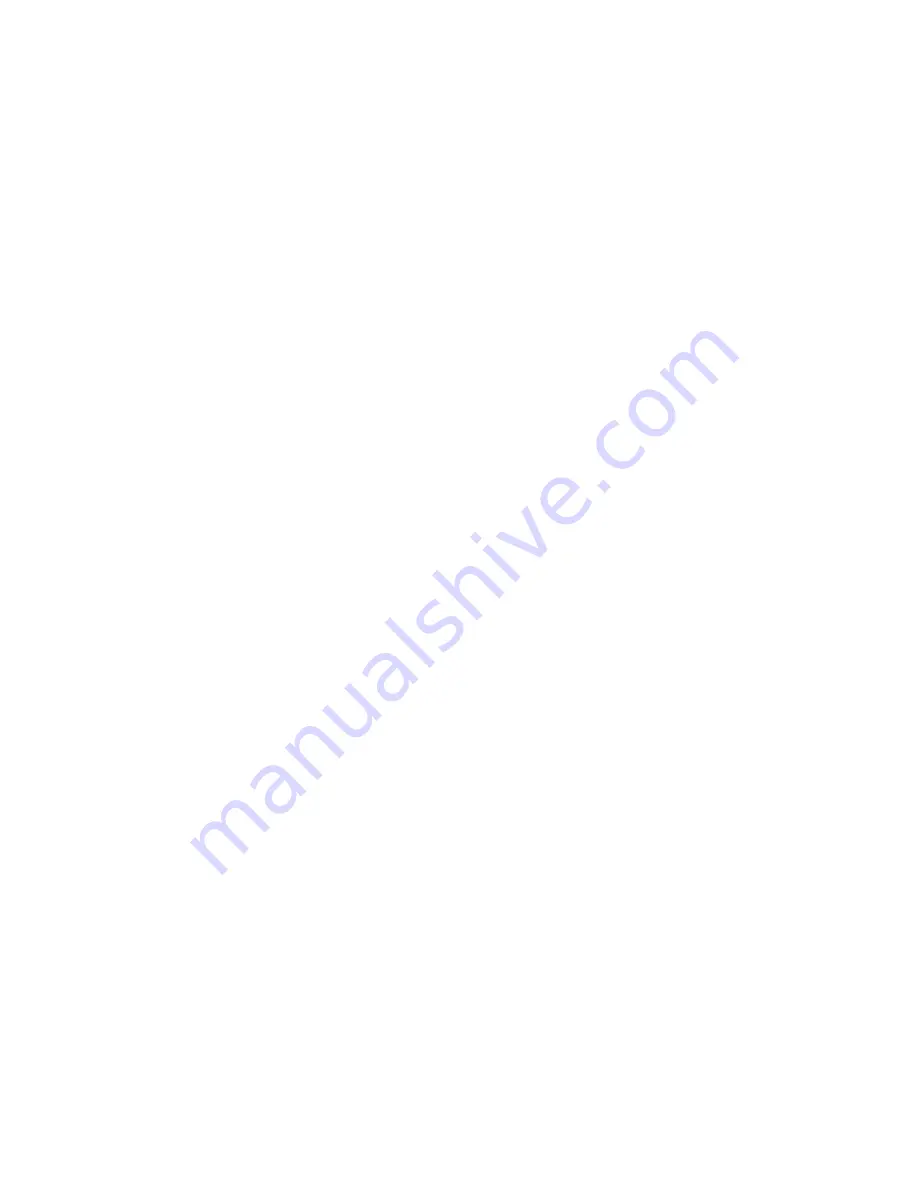
2. Contacts - breaker points that open and close to control current flow through
horn coil
3. Diaphragm - flexible membrane in horn that moves back and forth to produce air
waves and sound
4. Plunger - metal core that is attached by magnetic field of coil windings
5. Wire terminal - connector for making electrical connection with wiring harness
6. Outlet - opening of horn housing for directing sound to front of vehicle
When the driver presses the horn button, current flow enters the wire terminal and horn
coil. A magnetic field forms around the coil. The field attracts and pulls the plunger into
the coil. Since the plunger is attached to the diaphragm, the diaphragm is flexed back
toward the coil.
With enough movement, the edge of the plunger touches one of the contact point arms.
This pushes the contacts open and interrupts the current flow through the coil. Without
current, the magnetic field collapses, and the diaphragm snaps or flexes back into its
normal position.
Once the diaphragm and plunger move back, the contacts reclose. This reenergizes the
coil and the diaphragm is again pulled back toward the coil. The process is repeated
rapidly and the diaphragm vibrates back and forth in the horn housing. The resulting
vibration set up in the surrounding air can be heard as a "honking" sound.
A tone adjustment screw is normally provided for changing the sound of the horn. It can
be turned to affect the action of the contact points and frequency of the diaphragm
vibration.
Horn relay.
A horn relay is sometimes used between the horn switch and the horns. It
is used to reduce the amount of current flowing through the horn switch.
When the driver presses the horn switch, a small current flow enters the horn relay. This
energizes the small coil in the relay to close the relay contacts. Then, a larger current
flows through the closed relay points and to the horns.
Horn Service.
When a horn will not sound, check the fuse and connections, and test
the voltage at the horn terminal. If a horn blows continuously, the horn switch may be
bad. A relay is another cause of horn problems. The contacts in the relay could be
burned, or they may be stuck together.
A horn current adjusting screw is sometimes provided on the horn to set the amp draw
through the horn. To adjust horn current, connect an ammeter between the feed wire
and horn terminal. To prevent meter damage, be sure the ammeter can read more than
30 amps.
Get another person to sound the horn while you read the meter. If the current is not
within specifications (typically 4-5 amps), turn the amps screw on the horn until the
meter reads properly. Also, make sure you are getting adequate supply current/voltage
and there is not a high resistance in the horn circuit. If you cannot get the horn to read
within current specifications, replace it or isolate the circuit problem.
11.6.0 Small Accessory Motors
11.6.1 Windshield Wipers
A typical windshield wiper system is made up of a switch, wiper motor assembly, wiper
linkage, wiper arms, and wiper blades. Either a fuse or circuit breaker protects the
system.
NAVEDTRA 14050A
6-61