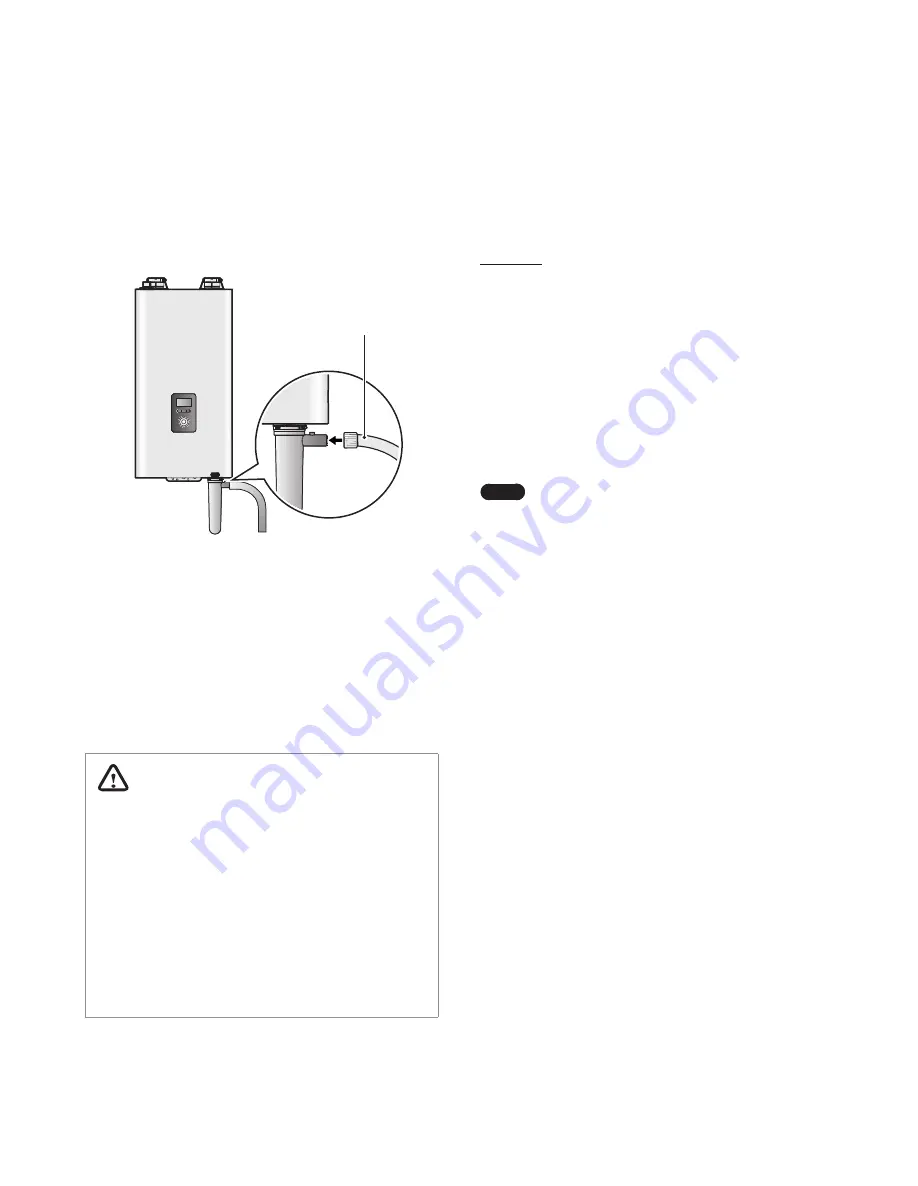
27
Installing the System Piping
To connect the condensate drain:
1. Connect a drain line to the
1
/
2
in fitting at the bottom of the
boiler.
Use only corrosion-resistant material for the drain line, such as
PVC or CPVC. Do not reduce the size of this fitting or the drain
line to less than
1
/
2
in.
NPT 1/2”
2. Place the free end of the drain line into an appropriate drain.
3. If you are using a condensate pump, ensure that the pump
allows for up to 3 GPH of drainage for each boiler in the
system.
4. If you are not using a condensate pump, ensure that the drain
line is pitched downward at a minimum slope of
1
/
4
in per foot.
3.3.1 Condensate Neutralizer Kit
WARNING
●
To avoid damaging the appliance, the neutralizer inlet and
discharge must be lower than the condensate drain.
●
Do NOT allow exhaust flue gases to vent through the
neutralizer. Leakage can cause injury or death from carbon
monoxide.
●
The connection between the appliance and the neutralizer
must be installed at a lower point than the condensate
drain fitting on the appliance to prevent the backflow of
condensate.
●
Do not connect more than one appliance to the neutralizer.
If option 'b' (p. 25) is selected as the disposal option, the Navien
condensate neutralizer kit is recommended. The condensate from
the appliance flows through the neutralizing media and increases
the pH of the condensate. An increased pH prevents corrosion of
the installation's drainage system and the public sewer system.
Installation
●
The inlet has a center connection port and the outlet has an
offset connection.
●
Install the neutralizer on the wall or the floor and secure it using
the brackets supplied with the kit.
●
If the neutralizer is installed horizontally, rotate the neutralizer to
position the outlet at the highest point (Figure 1).
●
If the neutralizer is mounted vertically, ensure that the outlet is
higher than the inlet (Figure 2).
●
Ensure that the condensate runs freely to the drain.
●
Use corrosion resistant piping and secure all piping to prevent
movement.
Note
Do not install condensate piping in areas where the
temperature drops below freezing point. Protect piping
in high pedestrian areas from damage and vibration.
●
If local codes permit, install a Y-fitting as a bypass drain for
increased safety when the condensate drain is blocked. Connect
the Y-fitting as shown in the installation diagram and ensure that
the condensate runs freely to the drain.
●
Ensure that the discharge connection is accessible. Access to
the discharge connection is required for maintenance and pH
testing.
●
If there is insufficient gradient for drainage, install a drainage
pump designed for boiler and water heater condensate removal.
Summary of Contents for NFC-175
Page 122: ...Memo...
Page 123: ...Memo...