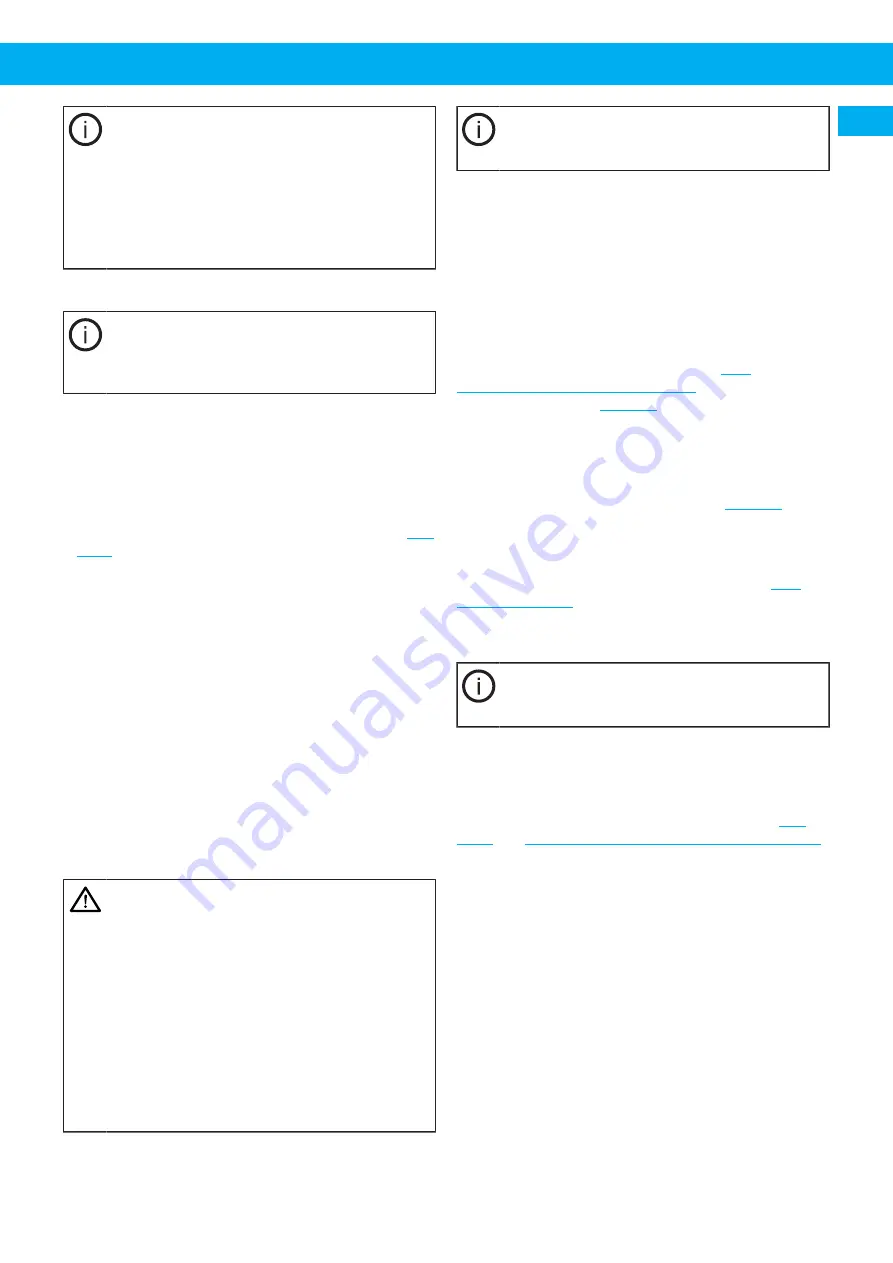
FlexPAK
NOTE!
• Some materials may undergo chemical reac-
tions in combination with humidity/water.
Such humidity may, for example, form if the
humidity in the extracted air is condensed in
the filter.
• Materials extracted by the unit is to be con-
sidered waste and is to be discarded.
5.1 Before initial start-up
NOTE!
The unit is NOT to be operated under any cir-
cumstances without directing the exhaust air
away from the unit.
It is important that no dust, objects or debris are al-
lowed to fall down into either the inlet or outlet of the
side channel fan.
The unit with its accessories are tested before deliv-
ery, and all functions are checked. Before the initial
start-up ensures the following:
• The maintenance switch has been installed, see
item 8.
• The room where the unit is located, if small, has ad-
equate ventilation. See the Installation and Service
Manual.
• The ducting is connected to the dust collector inlet.
• An exhaust air duct is attached to the outlet to dir-
ect hot exhaust air away from the unit.
• The compressed air supply is permanently connec-
ted. Idle mode and the filter cleaning will not work
properly without a compressed air supply.
• The PS cable is connected, but no valves at works-
ites are open.
• Make sure that the ground check measurement has
been performed. See the Installation and Service
Manual.
5.2 Initial start-up
WARNING! Risk of electric shock
• Unauthorized personnel may NOT remain in
the vicinity of the unit when the control unit
is open. Authorized personnel performing
inspections and adjustments on the control
equipment need to be careful to avoid elec-
trical shocks.
• Always disconnect the supply voltage using
the maintenance switch when performing in-
spections and adjustments. If the frequency
converter has to be opened, wait 5 minutes
after disconnecting power to avoid a static
electric shock.
NOTE!
Ensure that no valves at any workstations are
open.
• Remove the control unit lid since checks and adjust-
ments in the control unit may be necessary during
the initial start-up. The PLC and the software are
password-protected.
The initial start-up is to be performed with the acous-
tic enclosure removed to verify the direction of ro-
tation. Refit the acoustic enclosure when all checks
have been performed.
5.2.1 Check the filter cleaning function
When the unit is in Running mode, see
tion 6.1.3 Running (Running mode)
cleaning button, see
cleaning procedure starts.
The filter cleaning function consists of the Filter
Cleaning Valve (FCV), which is a pneumatic cylinder
with a valve disc. The FCV is located at the top of the
filter housing under the enclosure, see
6.
A distinct change in sound can be heard as the valve
releases atmospheric air into the filter, indicat-
ing that the function works properly. See also
5.2.2 Check the automatic start and stop
function
NOTE!
This procedure only works if default PLC set-
tings are used.
• Press the Standby/Running button to put the unit
into Standby mode.
The unit is not to start until a valve is opened at a
workplace activating its microswitch, or the test start/
filter cleaning button is pressed, see the top of
and
Section 8.3 Filter cleaning in Running mode
When the valve closes, the unit switches over to Idling
mode and after a delay of approximately 10 seconds, a
filter cleaning operation is performed.
After an additional time delay of approximately 12
minutes, the unit will go into Standby mode.
The filter cleaning delay is set by the DIR_time relay,
and the stop delay is set by the SSR_time relay.
• With all valves at the workstations closed, check
that the motor slows down (a distinct change in
sound can be heard) and that switching to Idling
mode with filter cleaning takes place after approx-
imately 10 seconds.
Approximately 12 minutes after the unit has switched
to Idling mode, it should go to Standby mode due to
the SSR function switching off.
EN
25
Summary of Contents for FlexPAK Standard
Page 9: ...FlexPAK 13 12 10 9 7 8 2 1 3 4 6 5 11 3 11 7 8 9 12 13 15 14 18 19 10 17 4 16 15 20 5 9...
Page 10: ...FlexPAK 6 1 2 3 6 7 8 9 16 15 14 13 11 10 12 4 5 7 10...
Page 12: ...FlexPAK 2 1 4 5 6 8 7 9 3 9 1 1643 1mm 65 662 1mm 26 2 1771 4 1mm 70 13mm 10 12...
Page 13: ...FlexPAK 11 12 13 14 13...
Page 14: ...FlexPAK 15 A B 16 14...
Page 15: ...FlexPAK A B C 4x 17 8x 18 15...
Page 16: ...FlexPAK A 4x B 19 Min 2 1m 83 20 1 0m 39 4 21 16...
Page 17: ...FlexPAK A B C 22 23 17...
Page 39: ...FlexPAK SUV Solenoid upper valve TVFD Twin valve feed out device EN 39...
Page 60: ...FlexPAK CS SUV Horn elektromagnetick ventil TVFD Za zen pro vypou t n dvojit ho ventilu 60...
Page 81: ...FlexPAK SUV verste magnetventil TVFD Udgangsenhed for tvillingeventil DA 81...
Page 127: ...FlexPAK SUV V lvula superior solenoide TVFD Dispositivo de vaciado por doble v lvula ES 127...
Page 148: ...FlexPAK FI SUV Solenoidin yl venttiili TVFD Kaksoisventtiilipoistolaite 148...
Page 171: ...FlexPAK SUV lectrovanne sup rieure TVFD Dispositif de vidage double vanne FR 171...
Page 194: ...FlexPAK HU SUV Fels m gneses szelep TVFD Ikerszelepes kiadagol berendez s 194...
Page 216: ...FlexPAK IT SUV Elettrovalvola superiore TVFD Dispositivo di svuotamento a doppia valvola 216...
Page 239: ...FlexPAK SUV Bovenste magneetklep TVFD Uitvoer van apparaat voorzien van dubbele klep NL 239...
Page 260: ...FlexPAK NO SUV vre magnetventil TVFD Utmatingsenhet med to ventiler 260...
Page 283: ...FlexPAK SUV G rny zaw r elektromagnetyczny TVFD Dwuzaworowe urz dzenie odprowadzaj ce PL 283...
Page 312: ...FlexPAK RU FlexPAK FlexPAK DX 5 1 9 8 5 2 5 5 2 1 6 1 3 Running 8 8 6 312...
Page 323: ...FlexPAK 9 1 9 2 N e d e r m a n 2 3 11 9 3 1 2 3 4 12 5 13 6 7 14 8 RU 323...
Page 326: ...FlexPAK RU N e d e r m a n 11 1 FlexPAK 93 6 326...
Page 328: ...FlexPAK RU SUV TVFD 328...
Page 364: ...FlexPAK ZH 9 3 Nederman CE 9 1 9 2 Nederman 2 3 11 9 3 1 2 3 4 12 5 13 6 7 14 8 364...
Page 368: ...FlexPAK ZH SUV TVFD 368...
Page 369: ...www nederman com...