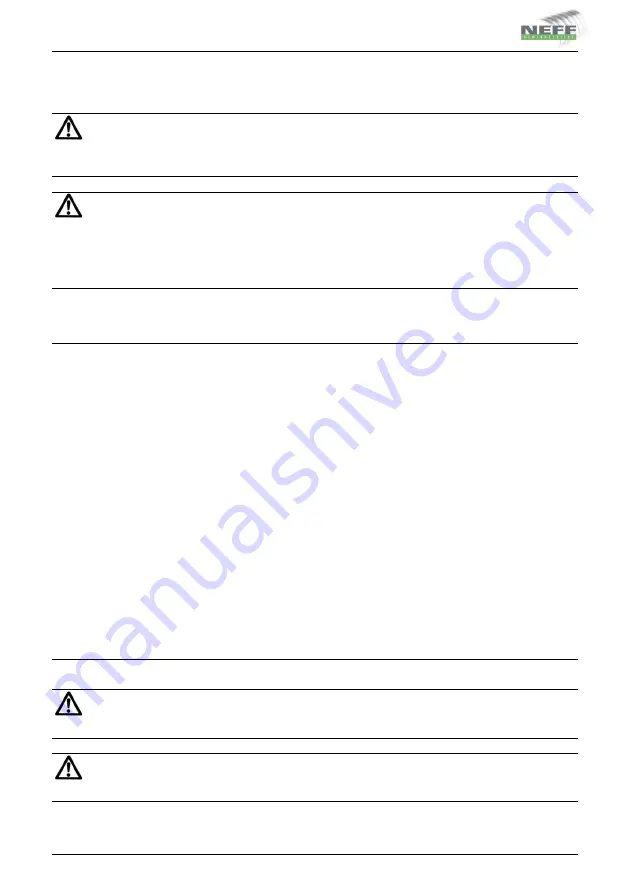
NEFF High Speed Screw Jack G1-G3
10
5
Commissioning
Attention!
Screw Jack oil filled and with vent valve: Install enclosed vent valve before operation.
Note install position, vent valve must be mounted above the oil level.
Attention!
Check the operation of the limit switch. If possible, start the High Speed Screw Jack without
any load and increase the load slowly.
During commissioning, continuously check the operating temperature, power consumption of
the motor and the screw contact pattern.
6
Maintenance
With trapezoidal screws, regularly lubricate the screw.
With ball screws, observe the following guideline: lubricate approx. every 200 hours with
1ml per 10mm of screw diameter
For version VK: The anti rotating block must be regularly lubricated. Move the Screw Jack
to the start position, carefully disount the square pipe plug and lubricate through the
recesses in the anti rotating block. Prevent dry running! Recommendation for the interval:
check once a month and if necessary relubricate (depending on application)
Approx. 5 operating hours after commissioning: Retighten all attachment bolts.
After approx. 50-100 operating hours: Lubricate the gear at the lubrication nipples once
again.
After approx. 200 operating hours or 1 year (sooner in tough operating conditions):
Check the screw nut for signs of wear and tear.
Clean the screw of old grease and relubricate.
After approx. 1000 operating hours or 5 years: Disassemble gear, clean it of old oil and
relubricate:
Attention!
For mounting new oil screw plugs: Take new seals!
Attention!
Change the screw nut if the axial play exceeds 1/4 of the thread pitch (trapezoidal thread).