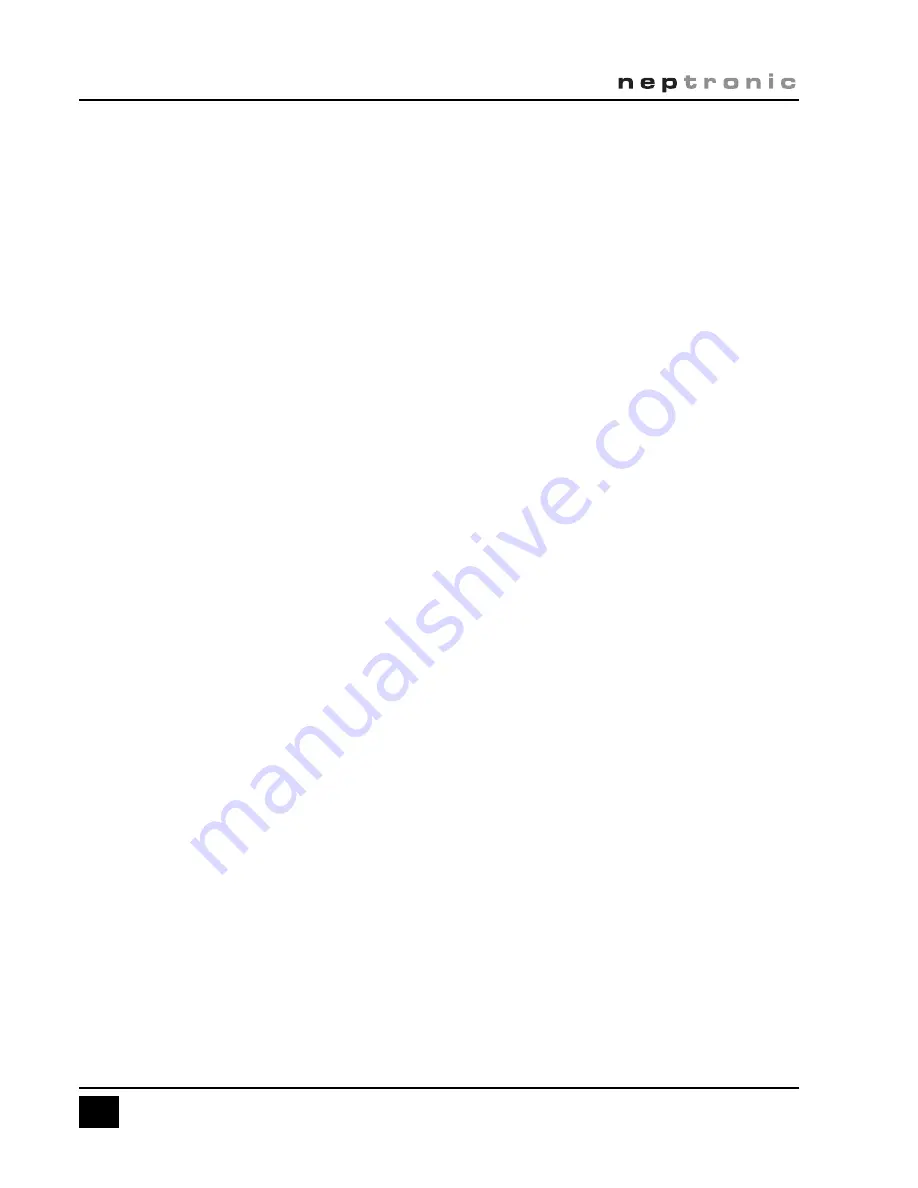
32
Neptronic
®
www.neptronic.com
Evaporative Humidification / Cooling System
De-scaling Method Statement
Descaling
In exceptional circumstances it may become necessary to descale the system. It is recommended that visual inspection
is carried out 3 months after commissioning and then annually thereafter. De-scaled and rinse with clean water if nec-
essary.
Do not use metal objects or high pressure washers to clean any part of the SK VAP .
The recommended de-scaling equipment is:
1. Suitable de-scaler
2. Descaler neutraliser
3. Two containers of adequate size to completely immerse a matrix cassette.
Step 1 - Refer to the risk assessment
• Refer to the manufacturers instructions and safety advice.
• Ensure the SK VAP system is OFF and the area well ventilated.
WARNING: When working with de-scaling solution always wear appropriate personal protective clothing,
protective gloves and eye protection.
Step 2 - Dismantle the SK VAP Evaporative Module
• Turn off and isolate all electrical and water supplies to the SK VAP.
• Dismantle the SK VAP Matrix into individual cassettes.
Step 3 - Prepare de-scaling solution
• Note the various control settings.
• All cleaning must be carried out outside as dangerous gas is being produced.
• Mix the appropriate concentration of descaling solution into adequate sized container.
Step 4 - Prepare clean water bath
• Ensure the clean water container is of adequate size to fully immerse cassettes.
• Fill the container with fresh, clean water.
Step 5 - Remove scale from individual cassettes
• Using a soft brush, lightly brush any loose scale from the surface of the matrix
• Lower the individual cassettes into the descaling solution.
• Keep each matrix cassette in the solution until the reaction between the calcium on the matrix and the
descaling solution is complete.
Notes:
1. The effect of the descaling solution will vary depending of the condition of the matrix material. The above
process may need to be repeated for an improved effect.
2. It may be necessary to descale the humidifier water tray. If so, please consult Neptronic® for advice.
Step 6 - Clean individual cassettes in water
• Lift the individual cassettes out of the acid solution, allow any excess descaling solution to drip and directly
submerse into the water tub.
• Gently wash the cassettes in the clear water until there is no evidence or odour of any acid left. Ensure that
no damage is done to the fibres of the matrix.
Step 7 - Reassemble the matrix
• Reassemble the individual cassettes into the SK VAP evaporative Module.
Step 8 - Flush the SK VAP to remove traces of acid
• Before normal operation of the SK VAP the matrix must be flushed and drained several times to ensure no
acid is left on the cassettes.
• Leave the AHU switched off and flush the unit by filling, operating and draining for at least 5 times.
This procedure should approximately last one hour.
Step 9 - Restart
• Where required, reset to original setting and put unit back into operation. Test for correct operation as per
commissioning section of the manufacturers manual.
• Check for and complete maintenance requirements as per manufacturers manual.
• Always leave work area clean, dry and tidy.
Summary of Contents for SK VAP
Page 4: ...4 Neptronic www neptronic com Evaporative Humidification Cooling System...
Page 17: ...17 Neptronic Evaporative Humidification Cooling System www neptronic com Wiring Diagram...
Page 18: ...18 Neptronic www neptronic com Evaporative Humidification Cooling System...
Page 19: ...19 Neptronic Evaporative Humidification Cooling System www neptronic com...
Page 20: ...20 Neptronic www neptronic com Evaporative Humidification Cooling System...
Page 21: ...21 Neptronic Evaporative Humidification Cooling System www neptronic com...
Page 22: ...22 Neptronic www neptronic com Evaporative Humidification Cooling System...
Page 34: ...34 Neptronic www neptronic com Evaporative Humidification Cooling System...
Page 35: ...35 Neptronic Evaporative Humidification Cooling System www neptronic com...