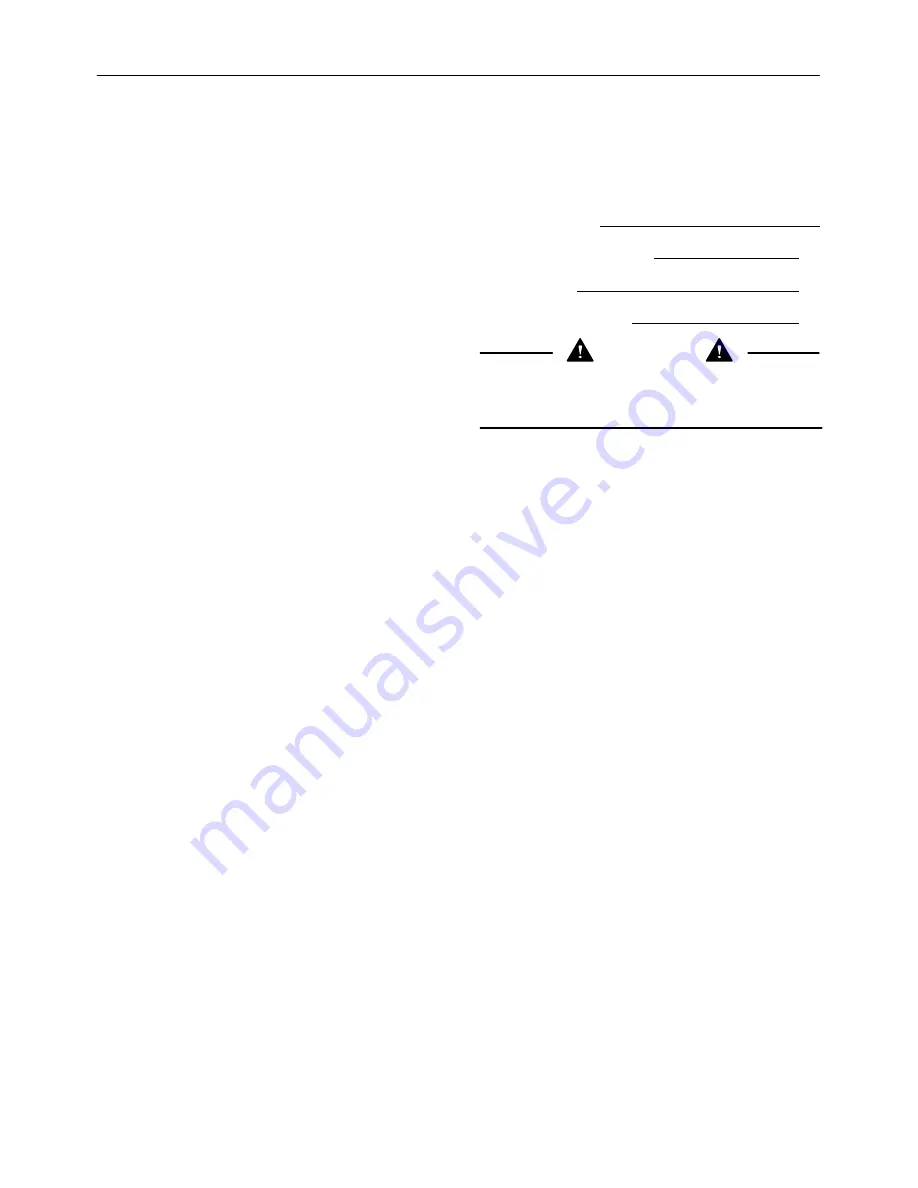
SECTION 00 - GENERAL INFORMATION
00-2
INTRODUCTION
This service manual provides the technical
information needed to properly service and maintain
the Models LS160 and LS170 skid steers. Use it in
conjunction with the operator’s manual which is
supplied with the skid steer. Keep both manuals
available for ready reference.
The L160 and L170 have many similarities with the
major differences being engine horsepower and
lifting capacity.
Whenever working on New Holland equipment, left
and right sides of the machine are determined by
standing behind the unit, looking in the direction of
travel.
The easiest and least time-consuming removal,
disassembly, and reassembly procedures are
detailed in the manual. Modifying these procedures
is not recommended.
New Holland skid steers are designed with emphasis
on safety for operator protection. However, careless
and negligent operation can still result in serious
injury to persons or damage to property. Be sure to
read and follow all safety instructions in this manual.
Your New Holland dealer is interested in your
obtaining the most from your investment and will be
glad to answer any questions you may have about
your skid steer. When major service is required, your
dealer’s staff of trained service technicians is ready
to serve you.
When in need of parts, always order genuine New
Holland service parts from your New Holland dealer.
Be prepared to give your dealer the model and serial
number of the engine and skid steer (the location of
these numbers is described later in this section).
Record the serial numbers here.
Skid Steer Model
Skid Steer Serial Number
Engine Model
Engine Serial Number
CAUTION
This symbol is used throughout this book
whenever your own personal safety is involved.
Take time to be careful!
ABOUT IMPROVEMENTS
New Holland is continually striving to improve its
products. We must, therefore, reserve the right to
make improvements or changes when it becomes
practical and possible to do so, without incurring any
obligation to make changes or additions to the
equipment sold previously.
ALL SPECIFICATIONS ARE SUBJECT TO
CHANGE WITHOUT NOTICE.
Find manuals at http://best-manuals.com/search?&s=NH-60413607